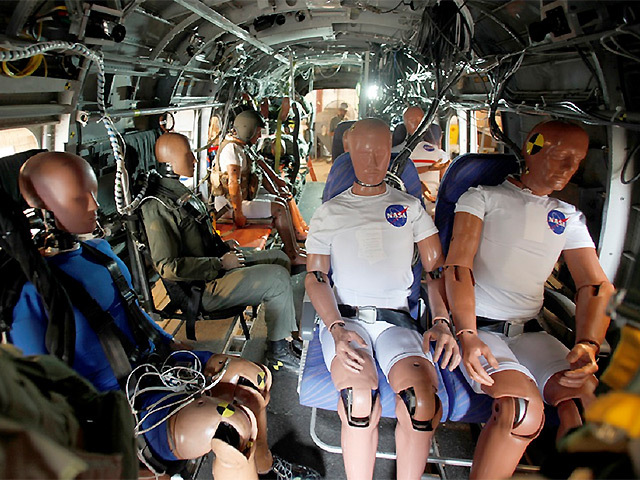
A helicopter was deliberately crashed on August 28 at NASA’s Langley Research Center in Hampton, Virginia as a part of the US agency’s quest to improve aircraft safety.
A 14m (45ft) helicopter fuselage full of crash-test dummies was deliberately dropped 9.5m (30ft) or so into a bed of soil to test improved seat belts and seats and to collect crashworthiness data.
Impact speed was around 30mph, which is deemed survivable.
The globally famous space agency is collaborating with the US Navy, Army and Federal Aviation Administration on the Transport Rotorcraft Airframe Crash Testbed for full-scale crash tests at NASA Langley’s Landing and Impact Research (LandIR) Facility.
LandIR, a 73m (240ft) high by 122m (400ft) long gantry, has an almost 50-year history.
It started out as the Lunar Landing Research Facility, where Neil Armstrong and other astronauts learned to land on the moon.
Then it became a crash test facility where engineers could simulate aircraft accidents. And recently it added a big pool where NASA is testing Orion space capsule mock-ups in anticipation of water landings.
Energy wonders whether that pool could be used to test helicopter types currently used in the North Sea, especially the Super Puma, four of which have failed in less than four years.
This latest drop test is one of the most complicated and ambitious aircraft crash experiments at NASA Langley in recent memory.
In essence, NASA engineers instrumented a former Marine helicopter airframe with cameras and accelerometers.
According to lead test engineer Martin Annett, almost 40 cameras inside and outside of the helicopter were fitted to record how 13 crash test dummies reacted before, during and after impact. Onboard computers also recorded more than 350 channels of data.”
External cameras captured images of an unusual looking helicopter. Instead of the usual Marine Grey, technicians painted one entire side in black polka dots over a white background.
It wasn’t a fashion statement, but a photographic technique called full field photogrammetry. Each dot represents a data point. High speed cameras, filming at 500 images per second, track each dot, so after everything is over, researchers can plot and “see” exactly how the fuselage buckled, bent, cracked or collapsed under crash loads.
Also pressed into service was a well-known video game motion sensor . . . an Xbox Kinect, which was fitted inside the fuselage.
Justin Littell, test engineer, said the team wanted “to see if it can be used as an additional instrument to track dummies’ movements.”
Another crash test of a similar helicopter equipped with additional technology, including composite airframe retrofits, is planned for next year.
Both tests are part of the NASA Aeronautics Research Mission Directorate’s Fundamental Aeronautics Program Rotary Wing Project.
The US Navy provided the CH-46 Sea Knight helicopter fuselages, seats, a number of crash test dummies and other experiments for the test.
The US Army contributed a crash test dummy that was laid down similar to a patient on a medical evacuation litter.
The FAA provided a side-facing specialised crash test dummy and part of the data acquisition system.
A private company, CONAX Florida Corporation DBA Cobham Life Support in St Petersburg, Fla., also contributed an active restraint system for the cockpit.
NASA will use the results of both tests to try to improve rotorcraft performance and efficiency, in part by assessing the reliability of high performance, lightweight composite materials.
Researchers also want to increase industry knowledge and create more complete computer models that can be used to design better helicopters.
The ultimate goal of NASA rotary wing research is to help make helicopters and other vertical take-off and landing vehicles more serviceable – able to carry more passengers and cargo – quicker, quieter, safer and greener. Improved designs might allow helicopters to be used more extensively in the airspace system.
So what tests have Eurocopter products been subjected to? That is not clear at this time, though the company participated in the so-called HeliSafe TA project launched at the end of the 1990s.
The trial was initiated by the aeronautical industry in Europe to develop equipment purpose-designed to reduce the risks of serious or fatal injury in the event of a helicopter accident.
Devices used in cars, such as airbags, safety restraint harnesses, special seats and safety belt pre-tensioners, for example, could be introduced for helicopters.
HeliSafe was kicked off by Autoflug of Germany in 1999 and came to an end in 2007.
The company specialises in the development and production of safety equipment, seats and electronic sensors for helicopters. The original consortium initially included eight partners from seven EU member countries, but as the project advanced, four further partners joined.
The core goal was to provide better protection for people in helicopters.
The first step was to gather all the available information throughout the world on helicopter accidents. Then Autoflug was able to devise standard crash scenarios that were used to perform accident tests in “real-life conditions”.
In time, this led to the development of a digital simulator, which paved the way to designing a safety and protection concept that was then translated into mock-ups that were then tested.
The upshot is that Autoflug has developed a safe cabin concept that includes special safety seats, airbags, optimised safety restraint harnesses with automatic inertia reels, safety belts with pretensioners and load limiters.
It has been calculated that in horizontal or vertical crash test scenarios, injuries are reduced by 30 to 40%. The research and results were then sent to regulatory authorities across Europe.
Recommended for you
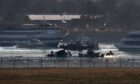