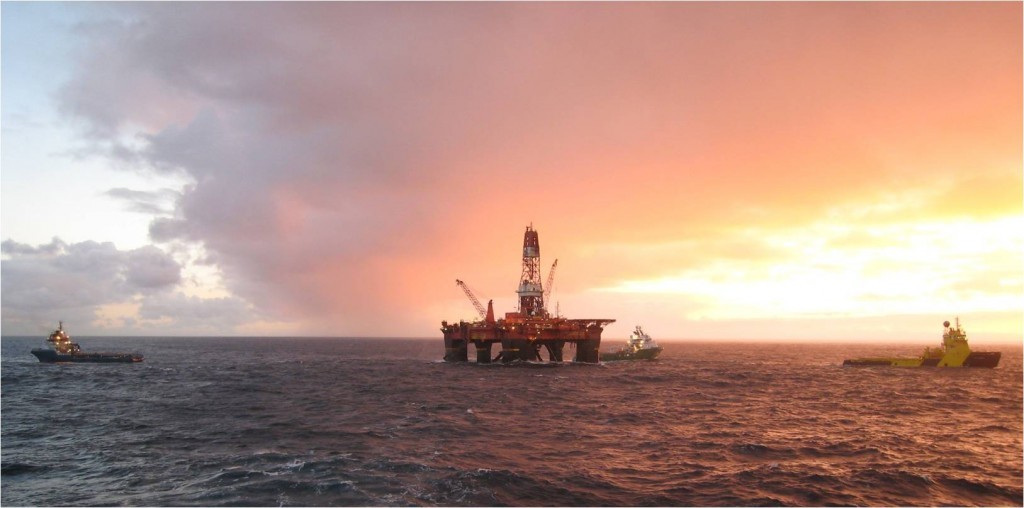
The struggling oil and gas industry could unlock £1billion worth of revenues by developing new techniques for inspecting offshore infrastructure, a new report says.
The study said companies’ efforts to check installations for corrosion and inspect vessels used to extract oil and gas were being hindered by technology gaps, which were lowering efficiency and increasing costs.
It set out to identify new and existing technologies which could cut costs associated with these two key areas of asset integrity, without compromising on safety.
It was put together using input from more than 90 technology-focused employees working for operators, contractors, government, innovation centres and academia.
The authors said vessel inspection is done manually, which is time-consuming and potentially hazardous, as the technician has to enter confined spaces.
And corrosion is difficult to trace because surfaces are covered with insulation, which is costly to remove and may require scaffolding, according to the research, which Oil and Gas UK (OGUK) commissioned from Lockheed Martin.
The study, titled, “The Asset Integrity Theme Landscaping Study”, picked out a number of technologies that could close the gaps, including “pulsed eddy current technique”.
This method involves driving an electromagnetic field though the insulation and into the pipe. Sensors then detect variations in the field that are caused by changes in the pipe.
But it said no single technique stood out as a silver bullet and that operators would likely have to combine several different ones to get a result.
Pairing sensing technologies with remotely-operated vehicles for vessel inspection could be one of the more profitable avenues, said the report, which was ordered on behalf of the Technology Leadership Board (TLB).
The government and industry-led TLB was set up to develop technologies which can help maximise economic recovery from the UK North Sea.
The authors called for a shortlist of the most promising technologies to be drawn up and for the establishment of industry partnerships to develop and trial new techniques.
They also recommended handing a single organisation the responsibility for drawing up industry standards for new inspection techniques and data sharing, among other things.
Paul White, director of subsea technology at GE Oil and Gas and TLB co-chair, said: “Delivering improvements in these key areas will help efforts to improve asset integrity, contribute to production efficiency and safely extend the operating lives of oil and gas fields.”
But the report’s authors said oil and gas companies might have to be cajoled into embracing new approaches.
They said: “Upstream oil and gas has a conservative culture and some resistance to change is inevitable. It is therefore essential that management and cultural factors are taken into consideration when selecting among technical options that have potential … for reducing costs.”
On the prospects for combining technologies effectively, they said: “It is likely that this will require some encouragement and support to get the different vendors and developers to work together.”
However, a poll by Deloitte published just last week indicated that North Sea oil and gas operators and suppliers are getting better at working together.
The research, again commissioned by OGUK, found that operators are engaging with suppliers earlier in projects are also showing a willingness to look beyond traditional partners to see what other companies can offer.
Recommended for you
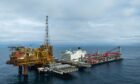