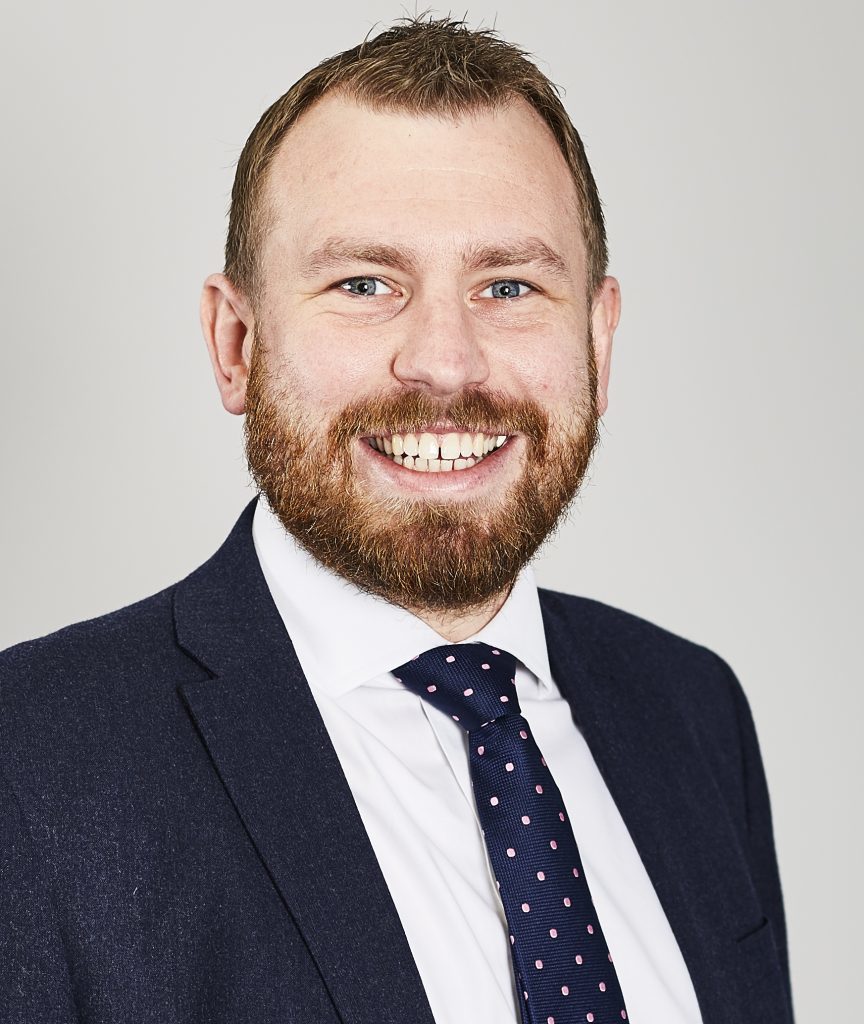
In the UK North Sea, a lower for longer environment has seen a number of operators accelerate their decommissioning programmes. But even an industry downturn has its silver lining. The start of decommissioning offers significant revenue for the UK’s supply chain. However, operators are faced with a lack of experience, so having the right team in place will be vital to success. If not they could face delays, rising costs and significant safety issues. Andrew Greenwood, Recruitment Director – Europe and Africa at Airswift, discusses this challenge, the decommissioning ‘dream team’ and the opportunity that lies ahead.
Shell’s North Sea Brent field is a cornerstone of the region’s oil and gas industry. Upon discovery in 1971 its lifespan was expected – at most – to be around 25 years. But with reserves drying up and many assets nearing the end of their operational lives, a wave of UK decommissioning has begun.
A largely unexplored frontier, decommissioning offshore assets offers a significant opportunity for the UK supply chain and workforce alike. Oil and Gas UK estimates an investment of nearly £17 billion will be required over the next 10 years to remove around 80 platforms and associated infrastructure from the UK North Sea.
As the numbers rise, the scale of the task at hand becomes clear. Oil and gas companies will require the right skills and expertise to complete projects safely, on time and on budget, without harming the environment – especially as decommissioning offers operators no return.
But with more than 600,000 tonnes of steel requiring decommissioning, it’s never been done on this scale before. So it makes sense that operators should now be thinking about sourcing a decommissioning team capable of tackling the unknown and writing the rules.
Engineered for success
With a number of projects being sanctioned, having the right expertise in place to execute projects will be crucial to ensure they are delivered on time and on budget. There will be a monumental focus from the UK Government and the OSPAR Commission on safe and environmentally responsible decommissioning.
The issue is these assets – some as big as the Eiffel Tower – were not engineered with decommissioning in mind. During the energy crunch of the 1970s, the main priority was getting operational as quickly and efficiently as possible. Little thought was given to how these platforms would be dismantled at the end of their production life.
These major assets need to be deconstructed and removed safely without leaking hydrocarbons or harming the surrounding marine environment. But dismantling massive structures will be a big task for a sector with little decommissioning experience.
However, for operators considering their decommissioning programmes, the industry downturn does mean there is an enhanced pool of highly skilled talent available. Now is the perfect time to source a team that can think on its feet to solve the problems of the unknown and execute projects without a hitch.
To recruit a ‘dream team’, companies will need five key features to ensure success:
- Local experts: a key requirement for a decommissioning team will be candidates with extensive North Sea experience due to the region’s harsh conditions and the unique engineering and safety challenges.
- Reverse engineering: the next recruits will need to have solid engineering knowledge. Candidates who have the creative thinking and mindset to reverse engineer these projects and understand how to deconstruct infrastructure. This will not only save time, but will ensure the project can be delivered safely.
- Experience: if operators can attract seasoned professionals who were involved in designing, constructing and commissioning these assets, then they will have an invaluable knowledge source at their disposal. Understanding the intricacies of these structures will mean that operators can solve problems quickly – helping projects to stay on track and on budget.
- Proficient planning: project planners who can write the rulebook to keep projects running safely on time and on budget in the North Sea will be vital for reducing costs.
- HSE excellence: no ‘dream team’ would be complete without skilled health, safety and environmental professionals who can establish robust working practises are in place and being carried out in line with regulations and safety protocols ensuring risk mitigation. Especially as industry bodies begin to clamp down on decommissioning as it heats up.
But even with an inflated talent pool, finding the right team necessary to successfully execute a decommissioning project, could still prove to be a huge administrative undertaking. Especially as oil and gas talent is transitioning to other industries – Energy JobLine reported that in the last 12 months, it has seen a 40 per cent increase in the number of oil and gas candidates applying for roles in renewables. And what’s more, developing a profile of these dream candidates can be difficult, time consuming and costly for operators.
This requires a big picture approach – understanding the holistic skill set on offer and where key transferable attributes lie. Partnering with a specialist workforce provider can ease the pain because they will already have candidates identified for decommissioning work and will have a solid foundation on how to recruit for this type of project.
Training for the future
If these skills can’t be found, operators will need to invest in their existing workforce to ensure they can hit the ground running, for example by introducing training, mentoring and knowledge sharing programmes throughout their organisation. This is not just an area for operators to tackle – there is a gap for oil and gas training academies across the UK to fill by developing courses addressing this challenge.
The sector as a whole can go one step further to prepare for the future by voicing the need for mandatory decommissioning modules to be incorporated into engineering degrees. Graduates now entering the industry could potentially spend their entire career in decommissioning – so it makes sense to ensure they are equipped from the get-go.
Exporting talent
If the UK takes the time to invest in decommissioning training and expertise, cities such as Aberdeen may become decommissioning centres of excellence.
The UK could then export this talent around the world with individual companies establishing themselves as experts in running large-scale decommissioning programmes. And it’s not just companies that can carve out a niche – candidates can also hone their skills and become specialists in their own right. These skills will be in demand, no questions asked.
For operators, it will always be difficult and costly to contract specialist decommissioning knowledge when the experience pool is small. By strategically sourcing candidates now, operators can be on the front foot to build their knowledge base and internal expertise in a cost effective way.
The start of decommissioning will be a poignant time for the UK oil and gas industry. But every cloud has its silver lining, and for the UK supply chain and candidates alike it’s the opportunity that lies ahead.
Like the silver tint of a dark cloud’s edges, opportunity always lurks behind the darkest hour. And the industry must be ready to take it when it comes.
Recommended for you
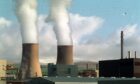