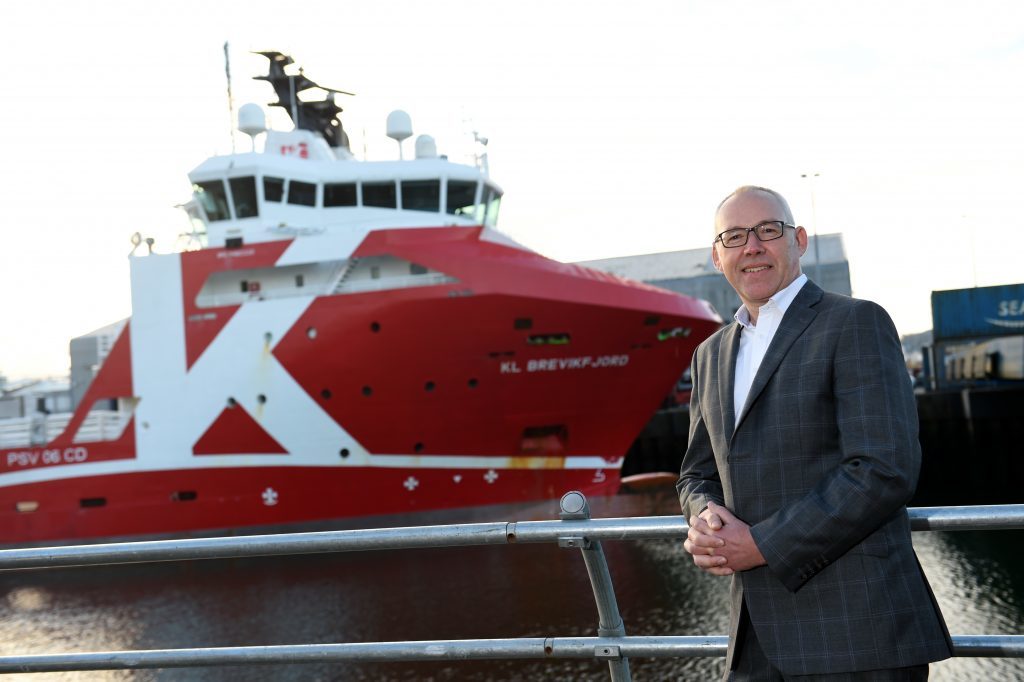
As the North Sea industry grapples with its cost base, has it done enough to ensure its place at the table to attract investment in order to realise the enormous potential left in the basin?
Where should it spend it’s time? Should it be on manufacturing barrels through production efficiency gains or inventing barrels through exploration activities?
For a start, significant strides have been made on improving production efficiency in the UK sector, reducing unit operating costs to $16/boe, according to the latest figures released by Oil and Gas UK.
This represents a year-on-year decrease of circa 24%. A significant gain no doubt, but with the economic reports suggesting that at prices below $50/bbl a large number of oil fields are still cash flow negative, more work on the cost base needs to be done in an environment of “lower for longer”.
Enough juice has been squeezed out of an increasingly distressed supply chain and more intelligent approaches are required for a viable business model.
This obviously needs a new way thinking and working to ensure sustainability going forward. Gone are the days where oil companies can employ large incumbent engineering companies on term contracts, attracting management overheads and creating an inefficient working environment by forcing all engineering through one non-competitive engineering and construction machine.
Rather, we see the emergence of leaner, more nimble engineering companies used to working in a competitive environment along with ad-hoc working arrangements. A much more efficient mode of working than traditional practices. A great example of this is the recent contracting strategy put into place by Repsol-Sinopec Resources UK Ltd replacing the a 10-year Wood Group modifications and operations contract to a much more efficient economic model, intelligently extracting value from the supply chain.
Engineering itself must become more pragmatic with solutions taking into account end of field life rather than traditional approaches of repair and replace. It is a lot more efficient to spend a few engineering hours on analysis proving that a defect is safe to defer until dismantlement rather than engineering, fabricating and installing a new replacement.
Gone are the days of exorbitant, unsustainable salaries and day rates which inflated project costs and behaviours to such an incredible point. A recent Aberdeen and Grampian Chamber of Commerce report suggests over 40% of companies have adjusted their payroll in line with market conditions. The oil and gas industry must align itself with national averages in order to re-balance its wage bill, and support justifiable costs on an ongoing basis.
We also need to make better use of the data that we already have for quicker decision making. Whilst large corporate ERP solutions are good at managing businesses on a global basis they do not lend themselves to easy visualisation of data at a local level. This drives a lot of end users to try and manipulate business critical data in spreadsheets. Innovative middleware cost effective, creative business compliant solutions can be put in place easily and quickly allowing a project team instant access and visualisation of relevant data, ensuring better use of professional’s time.
Which brings be back to my original question – manufacturing vs inventing? The answer is both. We need to focus on our cost base in order to “manufacture” our remaining bbls more effectively. This in turn will lead to the investment in the basin that will allow us to “invent” the huge potential still remaining in the North Sea.
Jonathan White is the business development director of Apollo. Get in touch here.
Recommended for you
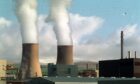