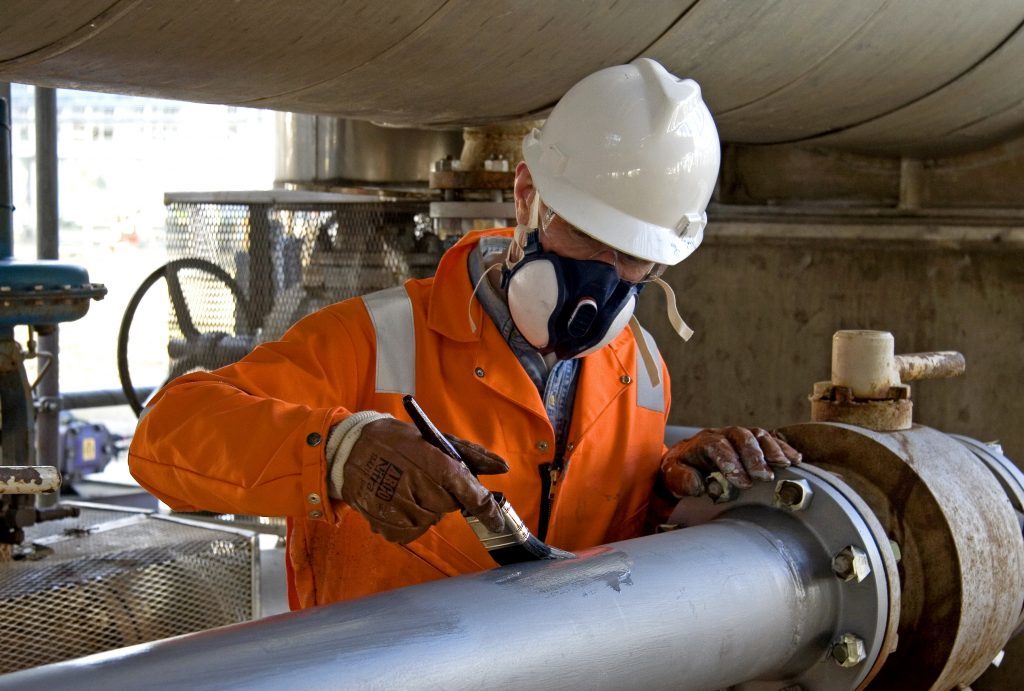
During 2016 alone, 17 decommissioning projects were postponed as operators extended field life.
With many opting to delay decommissioning for as long as possible, late life maintenance is top of the agenda for many companies in the UKCS.
The challenges associated with these assets are very different than those associated with new-build platforms.
The coatings used to prevent corrosion on new-build infrastructure can be expected to deliver protection of 25 years or more – an impressive achievement given the conditions that offshore assets and equipment are subject to.
This is made possible by three-layer epoxy coatings that have become the industry standard.
When an asset’s life is extended it can leave businesses in a tough predicament. In these ageing platforms, excessive corrosion can compromise the asset’s pipework, vessels and structural steelwork, so they cannot be left without an effective coating solution.
But with efficiency another key factor, why invest in a long-term protective system for an asset which may only be expected to be in service for another five years?
Jaco Naude, coatings technical authority at Aberdeen-headquartered Bilfinger Salamis UK, said the company has developed an innovative coating system which delivers on both integrity and efficiency.
“Bilfinger has developed a range of fit-for-purpose coating strategies based on the remaining operating life of installations, whether that be two years or 10 years,” says Naude.
“To tackle the challenges associated with this issue, we’ve launched a new two-coat system, specifically for late-life applications, that requires minimal surface preparation compared with the conventional approach, reducing both man hours and costs.
“It also removes the need to use solvents and reduces the overall volume of materials for shipping, waste and associated risk during fabric maintenance operations.”
Simplifying the process
One key benefit of the system is the speed of preparation thanks to the use of hand tools.
Once a corroded item is identified for coating, any heavy scale and debris is stripped away using a combination of hand chipping and power tool cleaning, with the remainder of the loose coating removed by a light wire brush.
“This also removes the process of setting up encapsulation as no grit blasting is required, which saves on equipment cost and man hours,” says Naude.
A powerful degreaser and corrosion remover is then diluted in water to produce a 15% solution and worked into the surface by hand or pressure jet, removing grease, grime and contamination.
The mixture is then left exposed for at least 30 minutes. This allows the process of passivation to take place, where the surface reacts with the environment creating a micro-coating that stands in the way of further corrosion.
A second solution, a corrosion inhibitor, is then used as a final rinse to neutralise and provide temporary inhibition to the surface beneath before a thin layer of water-based, low dirt pick-up enamel primer is applied. The reduction in preparation and application time provides significant cost savings for operators, while providing a fit-for-purpose solution which delivers excellent short term protection whilst still aesthetically enhancing an asset.
Naude adds: “The savings that can be achieved with our modern two-coat system over a conventional approach are compelling. Using Bilfinger’s late-life coating to cover a 2sq.m surface can provide an 85% reduction in cost compared to the use of a traditional three-coat epoxy system.
“With the opportunity to deliver such savings on bottom-line costs, the argument for tailoring coating systems to expected lifespans is clear.”
Recommended for you
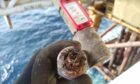