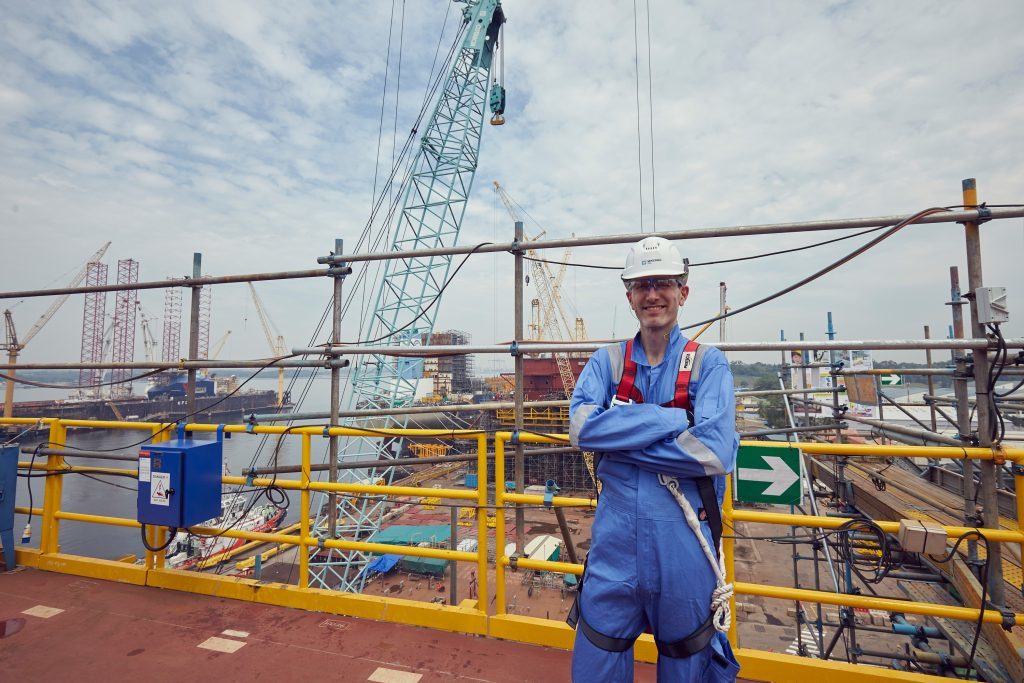
Maersk Oil’s Culzean field was hailed as the biggest find in the UK North Sea in 10 years at the time of its discovery in 2008 and approval for the development came seven years later. The project partners now seem to be reaching milestones every week. Mark Lammey went to Singapore in mid-March for a progress update.
The construction phase for the Culzean field’s topside and floating storage unit rumbled past the halfway stage in a sweltering Singapore last month.
Nearly 4,000 people are working like Trojans across two yards to get the installations ready for sail-away next year, followed by first gas in the second half of 2019.
On the northern coast of the island state, with Malaysia just visible through the haze on the Johor Strait, the three topsides are lined up like squat towers on the quayside at Sembcorp Marine’s Admiralty Yard.
The floating storage and offloading (FSO) unit, meanwhile, is taking shape on the south-west tip of Singapore, in the Tuas district.
The two yards are very different. While traces of the Admiralty Yard’s military past remain, in the form of naval housing near the entrance, it now has a feel of Amsterdam to it.
It is jam-packed with workshops and warehouses, but the sides of the roads are lined with racks holding myriad bicycles belonging to the 2,500-strong workforce.
The topsides will be bridge-linked once they reach Culzean, about 145 miles east of Aberdeen.
Drilling and production will take place on the wellhead platform, gas will be exported from a central processing facility via the CATS pipeline, and the crew will be put up in the third topside with 140 accommodation spaces.
First steel was cut for the modules in April 2016 and, so far, the build is going to plan. The amount of scaffolding erected around the structures makes them look more like giant metal haystacks, however.
Martin Urquhart, project director for Culzean at Maersk Oil, is encouraged by the progress being made on the £3.3billion project.
“We’re just reaching the critical phase now,” Mr Urquhart said.
“What we’ve done so far is build the pancake decks and put long-lead equipment inside.
“Now we’re going to plug all that together with pipes, cables, valves, instruments and junction boxes.
“That work needs to be very well coordinated to have a successful fit-out and installation phase.
“That’s important because the more we get commissioned here, the less work we are taking offshore to Aberdeen. We’re minimising carryover. So 2017 is a really big year, as is early 2018.”
Across the island, Sembcorp Marine’s Tuas Boulevard Yard is modern and expansive with vast, tall cranes.
There, some 1,300 people are responsible for bringing the FSO to life in the dry dock.
They appear to be immune to the heat and humidity that made visiting the yard such a draining experience.
First steel was cut for the FSO in summer 2016 with delivery expected in 2018.
The vessel will be roughly two football pitches long once complete.
It will store and heat the thick, waxy condensate from Culzean before offloading it onto a tanker.
The storage tanks inside the giant, whale-like hull of the FSO are being kitted out with rows of pipes, while the walls are being lined with anodes to prevent corrosion – they also create a visual effect similar to a climbing wall.
Back in the North Sea, preparations for the arrival of the topsides and FSO are not standing still.
Vessels were clearing boulders to make way for the gas and condensate lines, while in Rotterdam, a pipelay vessel was getting ready to mobilise in mid-March.
The Maersk Highlander rig started drilling the first of six planned production wells on the high pressure/high temperature field in September.
It was drilling through the wellhead platform jacket and well access deck, which were installed earlier.
The deck was built in Hartlepool and the jacket and piles were constructed at Heerema’s yard in Vlissingen, the Netherlands.
When the three topsides are installed in 2018 and hooked up in 2019, three of the six production wells will be ready for first gas.
Mr Urquhart said drilling was one of the areas where Maersk Oil had managed to uncover substantial savings.
In December, the company revealed costs on Culzean had been trimmed by £410million to £3.3billion.
“We had a plan to drill each well to its TD (total depth) sequentially,” he said.
“Then we realised the different types of cement we have designed to make these wells as strong as possible − because of the HPHT nature of Culzean – changes down that sequence.
“So you’ve got boats sitting offshore with different types of cement and you’ve got a constant logistical change because as you go deeper the cement changes.
“So we thought, hold on a minute, why don’t we just get all of the top-hole sections on all the wells drilled. It’s the same type of cement, the same type of tools.
“It’ll be a fantastic learning experience for a brand new rig. It’ll get the drill crews working together, it’ll get the logistics systems up and running and it’ll get safe operations working.
“So, when we analyse the top-hole drilling, we realised that we will get a significant amount of efficiency out of that and reduce our pre-spud estimates for the wells.”
The first production well will be drilled to its final depth by the end of 2017, while the remaining two topside jackets will be installed on Culzean later this year.
Dutch heavy lift specialist Dockwise has been chosen to pick up the topsides in May 2018 and take them on their month-long voyage to the North Sea.
Bids for hook up and commissioning work are being evaluated and awards will be announced in the next couple of months.
Mr Urquhart said Maersk was driven by a desire to get as much work done as possible in both the UK and Singapore to de-clutter the topside installation campaign.
The company wants to make sure it does not miss its seasonal-windows for installation and commissioning.
Technology and data are also playing a big part in making sure all the pieces of the Culzean puzzle fit together with minimal fuss.
A raft of technologies and data access systems will save time on maintenance and make training and handovers more efficient.
A programme called “Walk Inside” is helping Maersk iron out the kinks early as the company strives to make Culzean the “best performing asset in the North Sea”, in terms of safety, efficiency and reliability.
Mr Urquhart said: “In the bottom hand drawer in my office in Aberdeen there is an Xbox controller. I can log on and use it to simulate walking inside the Culzean complex as an avatar.
“You can interact with the infrastructure. If you reach a door at the top of a stairwell and you have to pull it towards you to open it, that could be dangerous.
“You become very aware of little things that could save you time, instead of finding out two years down the line that there is a hazard.”
Digital technology also lets the project team log information about equipment and access it instantly at a later date, and play out the steps involved in certain tasks, for example, removing a valve.
A so-called electronic permit to work lets engineers track the progress of the different construction phases weeks before they finish, which should improve efficiency by making it easier to tie the threads together.
These are just a few examples of the gadgets and processes being adopted on Culzean.
Mr Urquhart said: “On Culzean, we’ve been very fortunate to be able to take these technologies and actually marry them together.
“I don’t know if it’s a first-time deployment of all of these things working together but, certainly, we’ve had a very good opportunity to leverage elements of all of the technologies you see today.”
Mr Urquhart also said he is dabbling in the “soft sciences” for the first time through the Culzean project.
By that he means, paying attention to where people are sitting in their offices and making sure they are near the colleagues with whom they interact with most.
He said: “This is completely new for Maersk Oil. Because we’re all generally engineers, bringing in a science that is slightly softer and to do with human interaction takes a little bit of introduction.”
The logistical considerations associated with such a large project beggar belief. Against the background of a severe downturn, and a restructuring by parent company Moller-Maersk, It says a lot for the project team that they can stay on track.
- The Culzean field was discovered in 2008
- The field is expected to produce enough gas to meet 5% of total UK demand at peak production in 2020/21.
- First gas from the field is expected in 2019
- Resources are estimated at 250-300mmboe
- Co-venturers in Culzean are Maersk Oil (operator – 49.99%), BP (32%) and JX Nippon (18.01%)
Read the latest North Sea news in today’s edition of Energy. Pick-up a copy today in the Press and Journal.