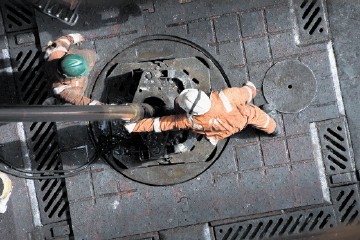
I got a wake-up call at a recent customer forum, where global contractors including GE were present: it was stated that a welcome reduction of “safety” incidents could be attributed to ‘talent density’, or a concentration of more experienced workers.
The suggestion was that the global oil price downturn had seen many less experienced workers leave the industry, with a much more experienced workforce left in place. It was said that this helped reduce the number of safety incidents from occurring.
That may well have been a factor, but I’d certainly like to think the industry-wide effort being made over the years to understand and address risk has played its part too.
“New norms” are needed for our industry. Not only for how high quality safety equipment is designed and produced, but for how oil and gas companies operate. At the customer forum, a discussion of “situation awareness” highlighted the need for true competency. This requires a cultural shift from normal safety practices to address the root causes of safety incidents, including lack of procedural discipline, lack of training, and lack of competence. A level of awareness is needed to fully appreciate the terrible potential consequences of getting it wrong.
So, what can we do?
For one, we can take lessons from programs like ExxonMobil’s “Mining the Diamond” which offers valuable insights on situational blindness to safety incidents, high potential incidents and quality misses. But we should also take a look outside our industry.
BMW’s manufacturing platform is a great example. Since 2009, the company has increased model variety for customers and instead of a one, three, five and seven series, BMW offers a 1 through 8 inclusive series. They used a platform strategy involving a scalable vehicle base, fixed design reference, and modular engine design. Common elements include engine layout, drive architecture, information systems, and suspension setup. The cars manufactured are differentiated by factors such as brands, market, styling and option codes.
What many of us didn’t realize is that, over the same period, BMW’s revenues grew significantly, while their engineering per car declined. The engineering head count has stayed flat over the same period and vehicle quality per car improved by about a third.
At the heart of their success was how the company killed “part number proliferation”. Generating a new part number on BMW’s platform requires unanimous approval at a senior control board, and/or an escalation and sign off by the CEO’s direct reports. As I listened to this presentation, it underlined the importance of having proper road maps to the same results that BMW achieved.
I believe our industry can change forever. No longer can we pursue heavily engineered, fully-customized system solutions that are not only uncompetitive in a sub$50/barrel market, but carry limited monetary margin opportunity, make for very tough execution and, attract quality misses.
Now is the time to deliver much more structured offerings to our customers and through our supply chain. To achieve equipment quality that improves offshore safety, we need repetition, commonality, and less procedural divergence in our build and test procedures. We also need true opportunities for application/requisition engineering cycle reduction, for part re-use and build and test synergies. This opportunity will be necessary to ensure safety, operational excellence, better quality performance and improved On Time Delivery for customers.
The way quality has been transformed in the automotive segment over the past 20 years is incredible. Think about your own experience – most of the time, cars simply work, every time and all the time. Why can’t the same be true for our industry?
Neil Saunders is president and chief executive of Subsea Systems and Drilling, GE Oil & Gas