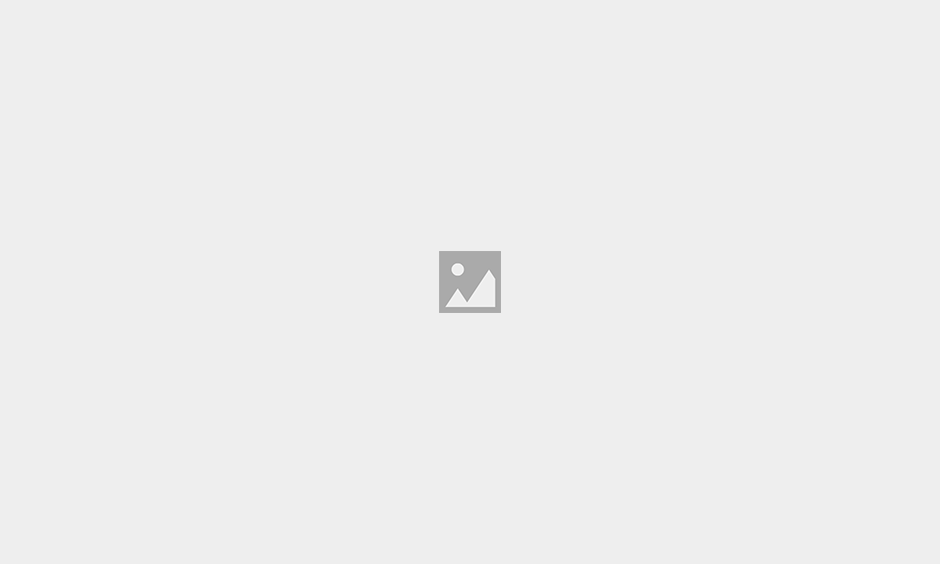
THE Alvheim production ship is, as indicated earlier, a rebuild of an existing vessel. The Odin had been competed as a tanker to a flexible design originally developed by Aker.
The so-called multipurpose shuttle tanker (MST) concept could be completed variously as a drillship, production ship or tanker. As a result, Odin was already strategically strengthened and fitted with a mooring turret compartment for a possible future role change.
The stresses that rack a trading tanker are quite different to a static production ship and the Aker design took account of this.
It was Keppel, in Singapore, that secured the job of modifying the hull, including raising storage capacity, before it was steamed to the Vetco Aibel yard at Haugesund for stripping of its propeller and rudder and fitting with the process package, gas turbines and so forth.
Part of the marine works included reconfiguring the “power station” style diesel-electric array in the engine room to provide four 8.5-megawatt generator sets.
On deck, at the back of the ship, are two enormous GE Nuovo Pignone gas turbines.
Roger Wilson said: “There are two large gas turbines; they are prototype, low emission units … the first of their type to be dual-fuelled to go out into the North Sea.”
APL won the contract for the turret mooring system – the largest in that company’s history. Basically, APL had to come up with a system capable of a service life of some 25 years and with 14 slots through the turret to accommodate risers and umbilicals for the initial subsea wells and for planned expansions.
Once in-field, the ship will be passively moored by 12 lines in an arrangement designed to withstand a 100-year storm with 14.6m significant wave height.
Marathon awarded Technip the EPCI (engineering, procurement, construction, installation and commissioning) contract for the installation of the subsea system.
The contract included design and supply of all line pipes, flexible pipes, umbilicals, riser bases and manifolds.
Space does not permit an endless rundown of who did what. However, the main equipment vendors include: gas compression – GE Thermodyne; power generation – GE Nuovo Pignone; swivel – Framo Engineering; water injection pumps – Sulzer; subsea multi-phase meters – Framo; topsides multi-phase meters – Roxar; separation – Kvaerner Process Systems; produced water treatment – Vetco Aibel; main cranes – National Oilwell; Xmas trees – and subsea controls – Aker Kvaerner Subsea; offloading system – Pusnes; turret and mooring – APL; risers – Flexifrance; umbilicals – Duco.