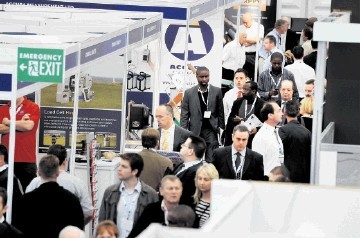
OFFSHORE Europe 2011 is just around the corner, construction of the temporary show halls at Aberdeen Exhibition and Conference Centre is well advanced and, in just a few weeks, Europe’s energy capital will host the most powerful upstream offshore oil and gas show outside Houston.
However, by way of sneak preview of the show, rather than pick through a selection of companies and products, we at Energy have decided to focus on four upcoming/still establishing technologies that are set to reshape current approaches to well construction and integrity.
According to Malcolm Pitman, chairman of new well technologies for this year’s Offshore Europe conference programme, mastered by the Society of Petroleum Engineers, such technologies are as important to new field developments as brownfield life extension work and most are appropriate for the North Sea, though oil company conservatism still remains an obstacle.
Mr Pitman, who is a vice-president at Tendeka in Aberdeen and a specialist in well construction, well intervention, new technology and mature field development, is someone who is not afraid to challenge the status quo.
On the underbalanced drilling front, a technique little used in the North Sea but widely applied in other energy provinces such as North America, Mr Pitman said a Norwegian company has been developing an exciting new approach involving a downhole piston.
“Their underbalanced drilling method uses an outer (piping) string and an inner string, and they circulate their fluids down the outer string and up the inner string in the drillpipe itself,” Mr Pitman told Energy.
“But they have a piston on the 9-5/8in casing annulus, and another hydraulic system that applies pressure to it so you can drill longer and deeper.
“It means you can do much longer horizontal sections (in a well). And you will no longer run out of (mud) weight on the drillfloor to put down because it’s laying on the low side of the well, as you’ve got this hydraulic piston that allows you to push it (the mud) farther down the well.
“During this application, the cuttings come up the inner string. And they come up at a high speed so you get cuttings from the reservoir that you’re drilling very quickly. They’ve not been rolled around the casing all the way until they get to the drillfloor, so they’re in pristine condition.
“Palaeontologists get access to cuttings of a quality they’ve never seen before. One can see every microscopic animal within.”
How a well is completed and managed thereafter is critical, and myriad technologies have been developed and applied.
Mr Pitman said: “Everybody is talking about the monitoring and control of a completion.
“So we have fibre-optics in a completion from top to bottom which is fairly easy to do.
There are hundreds of applications worldwide where you have temperature measured to 0.01C for every single metre of well every second of the day.
“But optical pressure reading is starting to be adopted too.
“This is a non-electrical pressure gauge where the optical fibres are bent. When you bend the fibres you can measure the bend on a diaphragm and this gives you pressure. That’s a state-of-the-art example of where completions are now going.”
The beauty of this approach is that it is non-mechanical, benign, and its use is gaining momentum.
Communicating wirelessly from the wellbore is good from an integrity perspective, as there are no electrical or optical cables or hydraulic lines between the surface and business end of a well.
Now the talk is of independent downhole devices that can transmit data/commands acoustically, magnetically – through the steel itself – or via a pulse in the produced flow that allows readings to be taken from the sensor of a wellhead.
“Also, the capability to read multiple wells from a single sensor on the seabed – electro-magnetically or acoustically – and being able to transfer that data to the surface is emerging,” said Mr Pitman.
“This is now a focus at Statoil. They would like an inflow control device that one can send a signal down to.
“It would adjust to open or close a portion of or even shut-in a reservoir.
“It needs to be autonomous and therefore it needs to have downhole power generation – perhaps a helical turbine or suchlike.”
This has to be key to the future and not just in the North Sea, according to Mr Pitman.
Moreover, it was at the heart of a forum run last year as Macondo unfolded.
It provided quite an insight into well integrity from development to abandonment, and looking at various technologies that could assist us.
“In Norway, a company called Sandeband is working with a heavy, quartz-type material which is ground extremely finely.
“If you pack that in your (well) annulus, you find that you don’t need much of it to generate a very good seal.
“Consider the UK and Norwegian governments’ view on well integrity, and a lot of the time when decommissioning a well you’re asked to cut casing strings and run cement around things, but in certain cases the shales that are there will produce better seals than the cement that you may use.
“In the context of ISO, the standard for well integrity, taking shale into consideration as a barrier in its own right is being considered.
“It’s better than cements, including rubber-based cement, which swells when it comes into contact with water to create a better seal.”