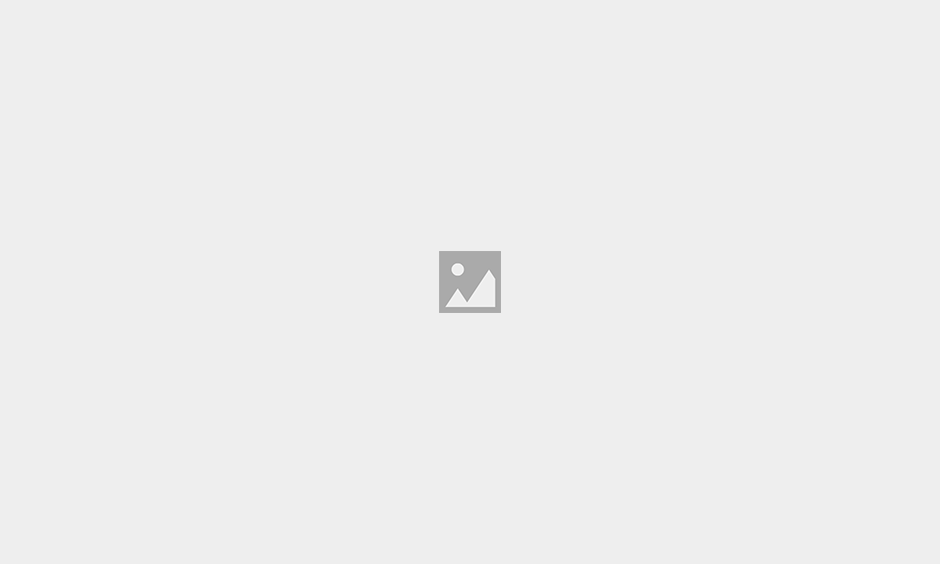
GustoMSC expects Keppel FELS in Singapore to have the first of the innovative “Bully” class drillships ready this summer for delivery to owners Frontier Drilling and Shell.
The second of the class is expected to be completed before the year-end.
The Bully design is a derivative of the PRD 12,000-class drillship, which was designed to work in Arctic waters. Crucially, the new vessels will be capable of working with subsea blowout preventer/marine riser systems and surface BOPs.
Frontier made its original approach in 2003 and, in 2007, Frontier, with Shell, signed up to the new-build programme.
According to Laurens Claassen who, together with three other colleagues from GustoMSC, delivered a paper on the company’s drillship designs at this year’s Offshore Technology Conference in Houston, the Bully provides “a competitive solution for the deepwater campaign which conventionally would require a sixth-generation drillship”.
The objective is to offer a smaller than normal vessel capable of operating at “lower rates” for deepwater operations, utilising surface BOP technology.
Claassen told his audience that the Bully requires less construction time and more yards have the capability to build them than current large deepwater units.
Lower power requirements on generators and thrusters and less fuel consumption can also mean potential savings of $25,000-35,000 per day.
Advantages of using surface BOP systems include less time required to run and pull the riser string due to faster handling joints; reduced circulation time; less time required to test the BOP, and less accumulation of cuttings in the riser because of more efficient hole cleaning, which results in a higher rate of penetration.
Well control will be facilitated because a smaller volume of drilling fluid will be required; there will be a reduction in overall logistics, storage, transportation and waste disposal, and there should be improved well control due to short choke and kill lines – and also a lower risk of hydrates formation.
Claassen said: “There are numerous advantages of surface BOP technology. They all originate from two requirements – reducing requirements on equipment and reducing time that it takes to drilling the well.”
The Bully is also expected to offer crews a safer working environment by decreasing the volume of drilling fluids and chemicals exposure, among other safety measures. Risk should be reduced as the design incorporates enclosed passageways to port and starboard below the main deck which also offer an easily accessible fore-to-aft escape route.
Such passageways protect workers from activities and incidents that can, on occasion, happen on the main deck, topsides or drill floor. They also offer valuable protection when working in Arctic conditions and, for that matter, when the vessels are operating in tropical/subtropical regions such as the US Gulf of Mexico.