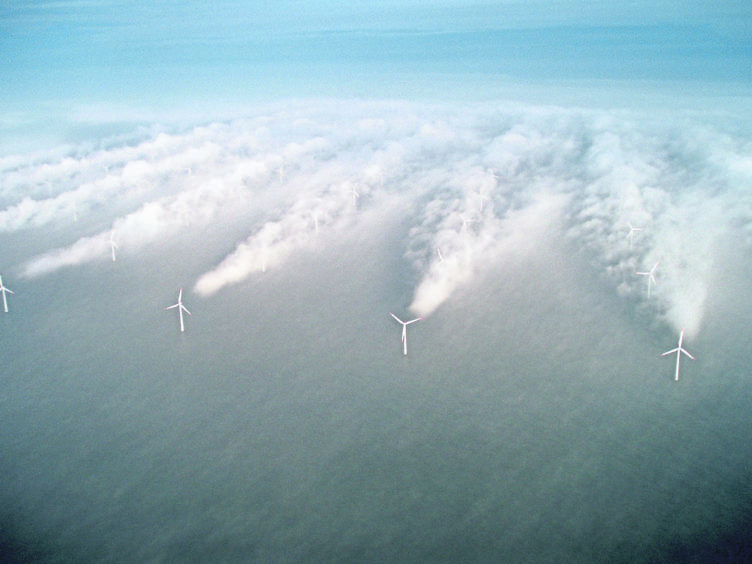
The push to find low-carbon energy solutions is gaining momentum in the academic world and eclipses the effort being directed towards oil and gas and coal-related research by universities.
I sit on an advisory group guiding an EU-funded PhD incubator with 34 research projects across two Irish universities and one Scottish institution, where
the focus is on marine and bio-energy.
Even in oil-dominated Aberdeen, serious questions are being asked about what the future course and research and development mix should be, in part because they risk being ostracised, indeed boycotted by Millennials who want nothing more to do with what they regard as dirty energy.
Take a look at the flow of energy-related news from universities worldwide. The overwhelming bulk of it relates to low-carbon energy and young people are pioneering it with zeal.
What follows is a surf through the highlights in mostly low-carbon energy R&D worldwide, starting with Lancaster University, where Professor David Antonelli is leading an international team of researchers who have discovered a new material that it is thought holds the key to cheaply unlocking the potential of hydrogen-powered vehicles.
ROAD HYDROGEN
In this field, a major obstacle has been the size, complexity and expense of the storage systems required, until now perhaps.
The new material identified by the Antonelli team could be used to make molecular sieves within fuel tanks that store the hydrogen and work alongside fuel cells in a hydrogen powered system.
The material, called Kubas Manganese Hydride-1 (KMH-1), would enable the design of tanks that are far smaller, cheaper, more convenient and energy dense than existing hydrogen fuel technologies. They would significantly out-perform battery-powered vehicles.
Prof Antonelli, who is chair in physical chemistry at Lancaster and has been researching this area for more than 15 years, said: “The cost of manufacturing our material is so low and the energy density it can store is so much higher than a lithium ion battery, that we could see hydrogen fuel cell systems that cost five times less than lithium ion batteries as well as providing a much longer range – potentially enabling journeys up to around four or five times longer between fill-ups.”
The material takes advantage of a chemical process called “Kubas binding”.
This process enables the storage of hydrogen by distancing the hydrogen atoms within an H2 molecule and works at room temperature.
This eliminates the need to split and bind the bonds between atoms, processes that require high energy, extreme temperatures and complex equipment.
The KMH-1 material also absorbs and stores any excess energy so external heat and cooling is not needed, which means less equipment needs to be used in vehicles, resulting in more efficient systems.
The material could enable the storage of four times as much hydrogen as existing hydrogen fuel technologies.
This should give car makers the flexibility to design vehicles with increased range or smaller tanks.
However, researchers believe there are many other applications for KMH-1.
“This material can also be used in portable devices such as drones or within mobile chargers so people could go on week-long camping trips without having to recharge their devices,” Prof Antonelli said.
“The real advantage this brings is in situations where you anticipate being off-grid for long periods of time. It could also be used to run a house.”
HARNESSING BUGS FOR ELECTRICITY STORAGE
At present, no existing technology provides large-scale storage for wind, solar and wave energy at a low financial and environmental cost.
However, according to American researchers at Cornell University, “engineered electro-active” microbes could be part of the solution. These are capable of borrowing an electron from solar or wind electricity and using the energy to break apart carbon dioxide (CO2) molecules from the air.
The microbes can then take the carbon atoms to make biofuels. They could be burned in a generator or added to petrol.
Buz Barstow, assistant professor of biological and environmental engineering at Cornell, said biology can play a significant role in creating a sustainable energy infrastructure.
He is the senior author of the academic paper Electrical Energy Storage With Engineered Biological Systems, published in the Journal of Biological Engineering.
Adding electrically engineered elements could make the approach even more productive and efficient than microbes alone.
Farshid Salimijazi, a graduate student in Prof Barstow’s lab, said: “We are suggesting a new approach where we stitch together biological and non-biological electrochemical engineering to create a new method to store energy.”
Natural photosynthesis already offers an example for storing solar energy at a huge scale.
But photosynthesis is regarded as being really inefficient at harvesting sunlight, absorbing less than 1% of energy that hits the cells.
This is where electroactive microbes come into play. They make it possible to replace biological light harvesting with photovoltaics.
The microbes can absorb electricity into their metabolism and use this energy to convert CO2 to biofuels.
The approach shows a lot of promise for making biofuels at higher efficiencies.
It is recognised that non-biological methods for using electricity for carbon fixation (assimilating carbon from CO2 into organic compounds, such as biofuels) are starting to match and even exceed microbes’ abilities.
However, electrochemical technologies are not good at creating the kinds of complex molecules necessary for biofuels and polymers. Engineered electroactive microbes could be designed to convert these simple molecules into much more complicated ones.
Combinations of engineered microbes and electrochemical systems could greatly exceed the efficiency of photosynthesis. For these reasons, a design that marries the two systems offers the most promising solution for energy storage.
The researchers plan to test out all possible combinations of electrochemical and biological components and find the best combinations.
PLASTICS TO FUELS
The growing war on plastics is now commanding headlines worldwide as the staggering scale of the challenge gradually dawns.
Worldwide, out of the 8.3 billion tonnes of plastic ever produced, more than 6bn is now plastic waste.
Any way of reducing this staggering legacy must be welcomed, including turning it into fuels of various kinds.
In a paper published in the Applied Energy journal, Washington State University’s Hanwu Lei and colleagues said they melted plastic waste at high temperature with activated carbon, a processed carbon with increased surface area, to produce jet fuel.
“Waste plastic is a huge problem worldwide,” said Mr Lei, an associate professor in WSU’s Department of Biological System Engineering. “This is a very good and relatively simple, way to recycle these plastics.”
Prof Lei tested low-density polyethylene and mixed a variety of waste plastic products, like water bottles, milk bottles and plastic bags and ground them down to about the size of a grain of rice.
The plastic granules were then placed on top of activated carbon in a tube reactor at a high temperature, ranging 430 to 571 degrees Celsius.
The carbon is a catalyst.
“Plastic is hard to break down,” Prof Lei warned. “You have to add a catalyst to help break the chemical bonds. There is a lot of hydrogen in plastics, which is a key component in fuel.”
Once the carbon catalyst has done its work, it can be separated out and reused on the next batch of waste plastic conversion. The catalyst can also be regenerated after losing its activity.
After testing several different catalysts at different temperatures, the best result they had produced was a mixture of 85% jet fuel and 15% diesel.
“We can recover almost 100% of the energy from the plastic
we tested,” Prof Lei said. “The fuel is very good quality and the by-product gases produced are high quality and useful as well.”
He also reckons the method for this process is easily scalable. It could work at a large facility or even on farms, where farmers could turn plastic waste into diesel.
LIQUID FUELS FROM THIN AIR
Hydrocarbons can still pull a few surprises, despite becoming increasingly regarded as energy pariahs and losing out to low carbon in the race for R&D funding.
Researchers from ETH Zurich have developed technology that produces liquid hydrocarbon fuels from sunlight and air.
For the first time anywhere they can demonstrate the entire thermochemical process chain under real field conditions. The new solar mini-refinery is located on the roof of ETH’s Machine Laboratory building.
Carbon-neutral fuels are crucial for making aviation and maritime transport sustainable. Help may be at hand as ETH researchers have developed a solar plant to produce synthetic liquid fuels that release as much CO2 during their combustion as previously extracted from the air for their production.
CO2 and water are extracted directly from ambient air and split using solar energy.
This process yields syngas, a mixture of hydrogen and carbon monoxide, which is subsequently processed into kerosene, methanol or other hydrocarbons. These drop-in fuels are ready for use in the existing global transport infrastructure.
Aldo Steinfeld, professor of renewable energy carriers at ETH Zurich, said: “This plant proves that carbon-neutral hydrocarbon fuels can be made from sunlight and air under real field conditions.
“The thermochemical process utilises the entire solar spectrum and proceeds at high temperatures, enabling fast reactions and high efficiency.”
The mini-refinery produces around one decilitre of fuel per day. However, Prof Steinfeld and his team are already working on a large-scale test of their solar reactor near Madrid.
The next project goal is to scale the technology for industrial implementation and make it economically competitive.
“A solar plant spanning an area of one square kilometre could produce 20,000 litres of kerosene a day,” said Philipp Furler, a former doctoral student in Prof Steinfeld’s group.
“A plant the size of Switzerland could cover the kerosene needs of the entire aviation industry. Our goal for the future is to efficiently produce sustainable fuels with our technology and thereby mitigate global CO2 emissions.”
ALGORITHM BOOSTS TURBINE POWER
Thanks to an algorithm developed at Stanford University in the US, the wind industry will be able to get more power out of its turbines.
A solitary turbine produces most power when pointing directly into the wind.
However, when tightly packed lines of turbines face the wind, wakes from upwind generators can interfere massively with those downwind, reducing the amount of electricity generated.
But by pointing turbines slightly away from oncoming wind – called wake-steering – it is possible to reduce that interference and raise production.
“To meet global targets for renewable energy generation, we need to find ways to generate a lot more energy from existing wind farms,” said John Dabiri, professor of civil and environmental engineering and mechanical engineering at Stanford.
“The traditional focus has been on the performance of individual turbines in a wind farm, but we need to instead start thinking about the farm as a whole and not just as the sum of its parts.”
Attempts to show the benefits of misaligning turbines at a real wind farm have been hindered by challenges in finding a company willing to halt normal operations for an experiment and in calculating best angles for the turbine. Until now, that is.
First, the Stanford group developed a faster way to calculate the optimal misalignment angles for turbines.
Then they tested their calculations on a wind farm in Alberta, Canada, in collaboration with operator TransAlta Renewables.
The overall power output of the farm increased by up to 47% in low wind speeds – depending on the angle of the turbines – and by 7-13% in average wind speeds.
Wake steering also reduced the ebbs and flows of power that are normally a challenge with wind power.
Through wake steering, the front turbine produced less power, as expected. But it was found that, because of decreased wake effects, the downstream turbines generated significantly more power.
Although the researchers were unable to measure a change in annual power production because of the limited 10-day duration of this field test, the next step, said Prof Dabiri, is to run field tests for an entire year.
Variable output by wind farms makes managing the grid more difficult in two important ways.
In the Stanford study, the power improvement at low wind speeds was particularly high because turbines typically stop spinning below a minimum speed, cutting production entirely and forcing grid managers to rely on backup power.
In slow winds, wake-steering reduced the amount of time that speeds dropped below this minimum, the researchers found. Notably, the biggest gains were at night, when wind energy is typically most valuable as a complement to solar power.
The other is the need to match exactly the amount of electricity supplied and used in a region every moment to keep the grid reliable.
Air turbulence from wakes can make wind farm production erratic minute by minute – a time period too short to fire up a gas generator.
This in turn makes matching supply and demand more challenging for system operators in the very short term. They have tools to do so, but the tools can be expensive.
In the study, wake steering reduced the short-term variability of power production by up to 72%.
Additionally, reducing variability can help wind farm owners lower their operating costs. Turbulence in wakes can strain turbine blades and raise repair costs. Wake steering could reduce turbine fatigue.