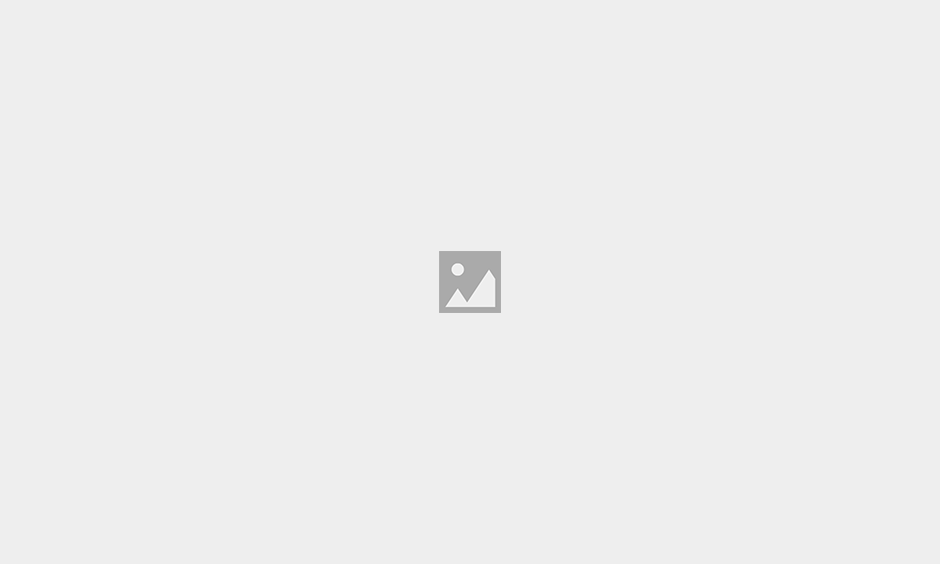
One suspects that Ian Whewell, who stands down at the end of this month as the head of the HSE’s Offshore Safety Division, has not always seen eye to eye with North Sea bosses.
He was tough at the 2007 Offshore Europe conference, oversaw the KP3 report, and the just published review of progress thus far is his last contribution.
Whewell told Energy that, while there were variations across the industry, by and large he was pleased with the way it had risen to the KP3 challenge. But he warned that there could be no let-up in the battle to stay safe offshore.
He said keeping offshore installations in good shape was a never-ending task and that companies must not forget this.
“It’s vital that you don’t ever decide that you’ve cracked it because, as soon as you do that, you’re doomed to failure because things get older and maintenance never stops. If anything, the volume of maintenance will increase,” said Whewell.
Whewell agreed that the drive to cut costs, especially in the 1990s and early-2000s had cost the industry dear.
It was a false economy; moreover, Shell had admitted this at a conference in Houston.
“If a major like Shell accepts that continuous maintenance is the answer, then I think the industry should listen.”
Turning to people and management’s attitudes, Whewell reckoned there had been a genuine turn for the better – witness the admission that NRB (not required back) was real and not a figment of trade-unionist imaginations.
“The NRB issue … I think that was a watershed moment for the industry.
“‘I’ve always viewed it as a bit like the alcoholic accepting that they were an alcoholic and then saying something like, ‘I’m going to sort myself out’.
“For many years, the industry was very reluctant to accept that there were situations when people were NRB.”
In his role as the North Sea’s best known trade unionist, Jake Molloy has, for sure, crossed swords with oil company and main contractor bosses, but he is a little mellower today and recently accepted an invitation to get directly involved with the Step Change Safety Initiative, which he has, in the past, hammered because of failures to reach targets set.
He told Energy that his being invited on to Step Change was, in itself, a watershed.
“Was it a genuine invitation? I don’t know, but I made it clear before accepting that if they thought getting me on board would be seen as my accepting Step Change policy then they were wrong,” Molloy said.
“I got involved to make a difference, so my tenure of involvement with the group may yet be curtailed.”
Molloy remains cautious about how effective workforce engagement in fact is. Fine words, but can the evidence garnered by the study be trusted?
“The industry argues the workforce is involved and will no doubt point to the workforce survey that formed part of the Workforce Involvement Group (WIG) report, where something like 85% of those questioned felt they were ‘involved’.
“However, when you consider that less than 30% had any kind of involvement with the safety case, you have to question the level and quality of that involvement.
“In short, workers are involved, but only to a degree which is determined by the industry.
“Industry leaders continue to balk at the idea of properly trained, properly resourced, empowered workers.”