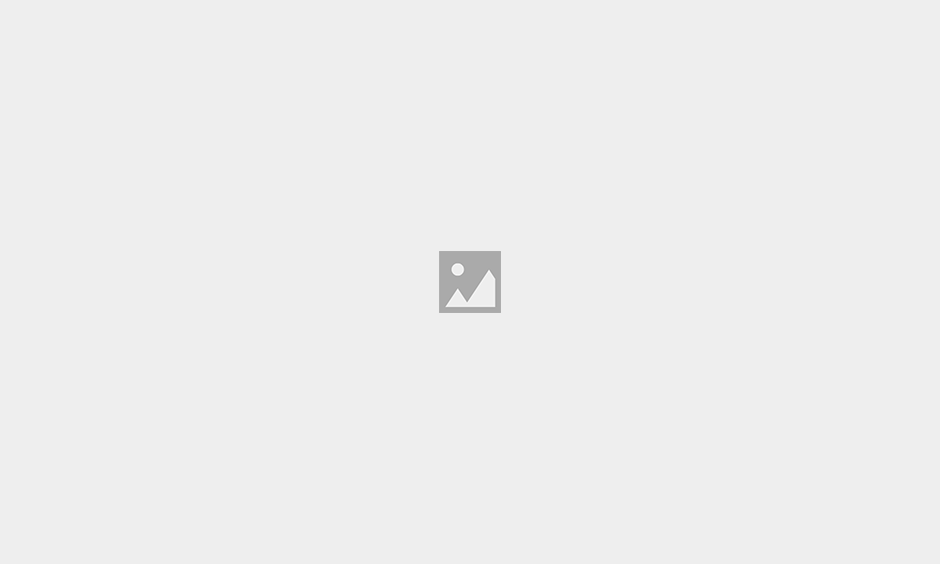
ON OCTOBER 13, BP formally sanctioned the £4.5billion Clair Ridge development West of Shetland, positive news that Prime Minister David Cameron sought to capitalise on by travelling to Aberdeen for the occasion.
But behind the announcement had already been years of preparation . . . much of it low key, systematic work and a logical follow-on to Clair Phase I, which was brought onstream in 2005. Witness the handover of the project batten from Ron Kelly to Chris Rees last year.
Kelly had taken Clair Ridge through the appraisal and selection phases; while Rees would navigate the project through the definition and construction execution stages, with the objective of achieving first oil in 2016.
Clair was discovered in 1977. But, such is the complexity of the field that £650million Phase 1 was not sanctioned until 2001, coming onstream four years later. There was talk of further development but this would hinge on first phase success.
And then how would it be done? A clone of the Phase I platform was discussed; even two clones.
“It was thought that we needed two copies because of the capacity that would be required,” Rees told Energy. “Phase I was only 80,000bpd name-plate. The right answer for the Ridge is 110,000 barrels nameplate but capable of up to about 120,000 per day.
“But the economics of building two clones, while viable, were such that the better solution was one very big complex with a large water injection capability because water is key to driving the reservoir.”
Rees described the uncertainties that have always bedevilled Clair, especially the complexity of this vast, heavily fractured medium-heavy (25 deg API mean) asset. It wasn’t until 1995 that BP managed to crack the field’s geological code and then it took another 11 years to commercial oil.
“There was uncertainty as to whether Clair would ever go much beyond Phase I and whether the (reservoir) compartments were ever going to flow and, by the way, were they connected?” said Rees.
BP turned to the US Gulf of Mexico for inspiration, especially with regard to Phase I platform design and build.
“It was done in a certain way, certain things were deliberately slimmed down because of the potential for (commercial) failure. We could have built a much larger platform even in those days. What I sense is that deliberate decisions were taken not to build the Rolls Royce or BMW of platforms then.
“With Ridge we’re a lot more comfortable in the ability to produce. We have Phase I data, plus the appraisal work on Clair Ridge, and recently announced work on Southwest Clair.
“This gives us confidence that we can build a very large central complex with the capability to handle subsea feeds in the future.”
That confidence also means BP is to apply its LoSal (low salinity) extended oil recovery technology, which is low salinity water.
Rees: “We’ve developed this onshore in various places including in Alaska. The advantage is that it helps improve recovery from the reservoir. It has an added benefit in that it reduces the amount of sulphates and the like that we put into the ground. A secondary benefit is that we see a reduction in the potential for souring of the reservoir, which is a big issue today for Phase I.
“We’re investing not just in oil production capability but also in the first application offshore of LoSal. This is the same technology as is used in the Middle East for freshwater production from salt water.”
It’s basically a semi-desalination plant. The kit will be huge. Each membrane pack will measure 4m by 8m by 8m. Multiples of these will be installed at Clair Ridge. They are bulky, heavy and are a key reason why the Ridge platform (actually two bridge-linked steel jacket structures) will be so large.
The other difference compared with Phase I is recognising that field life will be up to 40 years, so BP could be producing in 2056.
This is another reason why the complex will be generously proportioned. Equipment wears and it will be necessary to change it out and upgrade with the minimum of hassle.
“We have people from the Clair Phase I project and operations teams involved with Ridge,” said Rees. “So a lot of the learnings that we’ve picked up from that platform’s drilling rig and facilities design and how everything is currently working has been fed into the way that Ridge is being designed.
“Specific learnings have also been introduced from the Macondo incident, including physical changes. Those are being introduced into the rig design. We have various targets – safety, quality and operability – targets that must be met.
“It is important that we deliver an inherently safe design. This is one reason why Clair Ridge will have a pair of bridge-linked platforms, where accommodation, utilities and power are on one side, while processing is on the other. Given the scale of this there is no way everything can be fitted onto a single integrated deck anyway.”
The nominal topsides weight for Clair Ridge main platform is more than 42,000 tonnes; its jacket will be 23,000 tonnes. The smaller sister structure will have a jacket weight of 23,000 tonnes. Sophisticated thermal (hot) aluminium spray coatings will be used.
Recommended for you
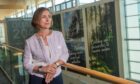