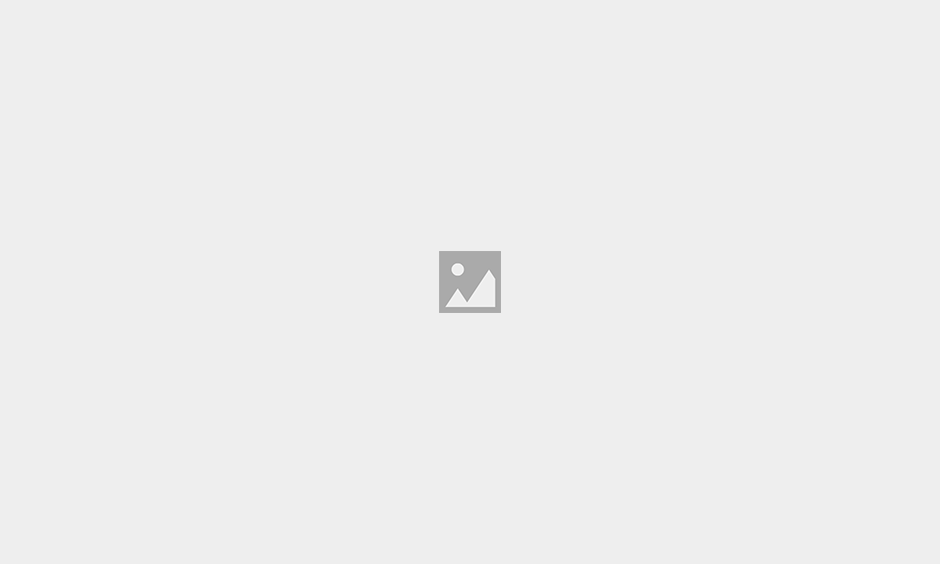
MUEHLHAN Surface Protection is poised to set new standards for grit-blasting on North Sea installations, with the introduction of technology that simultaneously blasts and immediately recovers the abrasives used.
Pinovo technology is well proven for onshore industrial applications, including at downstream petroleum industry processing/refining plants such as a Mossmorran in Fife.
Bringing Pinovo into the North Sea is just one of a number of fresh developments at the Aberdeen-based company, a satellite of the German group Muehlhan AG, which specialises in maritime and industrial surface protection.
Managing director, Jim West, said Muehlhan Surface Protection had also invented a simple way of ensuring that the frangible bulbs of deluge systems fitted aboard oil and gas installations are not left masked following periods of heavy plant maintenance, such as grit-blasting and repainting.
His team are further reinforcing the company’s offering with a fabric maintenance management tool and preparations are being made to introduce an OPITO-approved course in insulation.
“Muehlhan’s a very progressive company and we’re working actively on introducing new methods of working and standards to our clients,” said Mr West.
“Being a subsidiary of Muehlhan AG, headquartered in Hamburg, we have access to a development department that looks at innovation and different ways of working. There are also other things coming on to the market that people outwith the North Sea are introducing, and one of the main ones that we’ve been able to recently introduce to Shell, an important client of ours, is the Pinovo system.
“Pinovo is a Scandinavian company that has designed and developed an efficient way of carrying out grit blasting. Advantages are that it is cleaner, safer and there is less localised contamination, as coatings and corrosion which are removed are immediately sucked up and recovered directly to a chamber for cleaning, prior to shipping onshore for disposal.
“The user is not exposed to as much risk as with traditional blasting systems, and their personal protective equipment requirement is less, which in turn means that they have greater mobility. The great attraction for clients is that it means hazardous work and materials are far better contained than was previously the case.
“When you’re carrying out shot-blasting offshore there is always the risk of expended grit getting into machinery. That can in turn lead to shut-downs.”
Basically, the Pinovo machine is a combined shot blast gun and vacuum cleaner. The innovation lies in the head, which ensures that no grit escapes.
Muehlhan has recently introduced it on Shell’s Shearwater platform and will shortly be using it on the super-major’s Nelson installation, followed by other North Sea assets. The plan is to broaden its use to other North Sea clients.
Turning to the protection of frangible deluge bulbs, Muehlhan has developed a simple, fluorescent protective bag with a drawcord that is designed to cover this critical part of an installation’s fire-fighting system and be easily identified and removed.
The current method is to tape over the heads, otherwise there is a significant risk of damage from expended abrasives during traditional open grit-blasting operations.
But when the blasting is completed, in the darker areas of platforms, it is easy to overlook a deluge head where the bulb has been masked.
“This could compromise the effectiveness of a platforms deluge system just when it’s needed,” said Mr West.
“With our bag, all you do is fit it over the frangible bulb, pull the drawstring and it’s protected. Once blasting operations are completed, it is easy to spot the drawstrings and remove the bags.
“And, by making a change to the design of the original bag, if a deluge is triggered, the bags will be blown off by the water pressure. Small things like this can make a big difference.”
Yet another innovation being developed in Aberdeen is fabric maintenance management software geared to the kind of work that Muehlhan does offshore.
In essence, a platform’s structure and piping is surveyed to assess the condition of coatings, the data is inputted into the software and, by using information taken from existing standards and a system of complex algorithms developed for the purpose, it is possible to determine what has to be painted on an annual basis for the life of the platform.
“Our fabric maintenance management tool would be added to the package that we offer, which covers painting, fireproofing, insulation, scaffolding and rope access,” said Mr West.
Turning to training, which Muehlhan invests in heavily, the latest step is to bring the firm’s near 100-strong North Sea squad up to speed in insulation.
“I’m only aware of one other UK company that does it,” Mr West said. “What we want to do is introduce what is an OPITO-approved course and gain accreditation to start that training at our Aberdeen facility.
“The aim is to train all of our people to be able to apply insulation. That would make them even more multi-disciplined than they already are.
“Everyone is rope-access approved, all are shot-blaster painters and most of them are fire-proofers; what I want is for all of them to be insulators too.”
And it doesn’t stop there; the company is finalising arrangements to add scaffolding to its services.
A further innovation is the introduction of an asbestos removal capability, both offshore and onshore, including for industrial and public buildings.