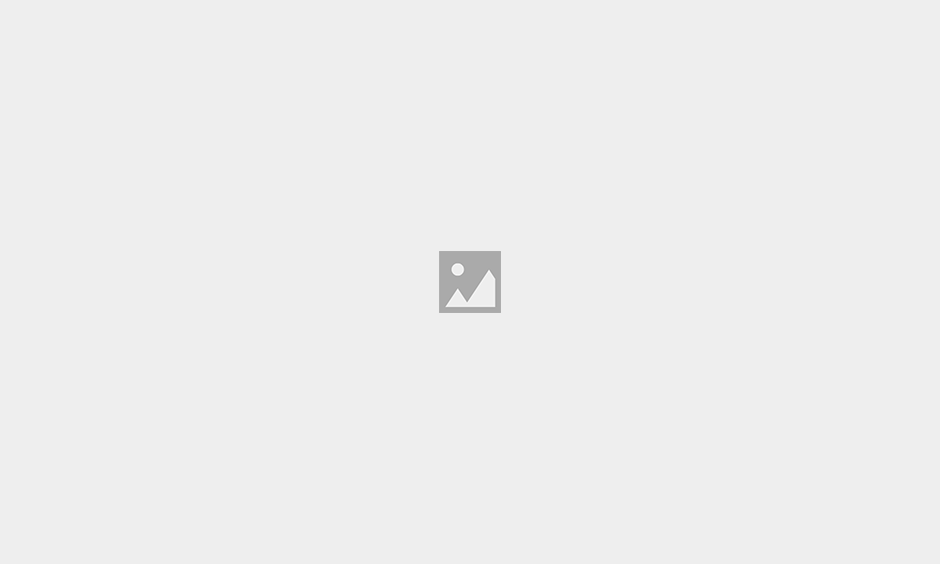
A bespoke filtration solution jointly developed by oil-industry chemicals supplier Champion Technologies and 3M’s Oil & Gas business has apparently significantly reduced the potential risk of blockage in a subsea chemical umbilical system recently installed in the North Sea.
While we cannot name the operator, the project is a very recent subsea satellite linked to existing infrastructure via a 28km subsea tieback.
The need to deliver chemicals over such a long umbilical system, many times typical umbilical length, led to a requirement for production chemicals to be filtered to an exact cleanliness level to minimise the risk of umbilical blockage.
“The longer the tieback, the more difficult and costly it is to pinpoint and remove any source of obstruction,” says Champion Technologies (UK) area manager, John Reid.
“Although there is nothing new about the use of subsea tiebacks, with an increasing percentage of the world’s reserves being in deep water, longer and deeper tiebacks are inevitable, and with them comes an increasing risk of umbilical blockage.”
Resolving blockages can be an expensive and time-consuming process. Most blockages require intervention by divers working from a support vessel, so the costs can, at best, be hundreds of thousands of pounds and, at worst, depending on deferred production, literally millions of pounds.
Proactive measures designed to prevent blockages from occurring are the key to maintaining effective chemical dosing regimes, addressing customer flow assurance issues and supporting the customer’s production objectives.
To achieve this, production chemicals utilised to treat the system require filtration to an appropriate specification.
The filtration process implemented for this particular operation was developed by 3M, working in close co-operation with Champion Technologies and the subsea development’s operator – a European mid-ranker.
An extensive laboratory testing programme identified 3M BetaKlean filters as the most appropriate for the filtration process, providing optimum product filtration.
3M’s Cuno Scientific Application Support Services (SASS) provided the laboratory testing services to support the development of a solution that was fit for purpose and agreeable to all parties.
3M also worked closely with Champion to modify existing filtration processes to provide a bespoke solution that was fully compatible with the various types of chemicals its filtration equipment would come into contact with.
The filtration system has now been installed and successfully commissioned, “despite the significant time pressures” that can apparently often be involved in a first-fill chemical process.