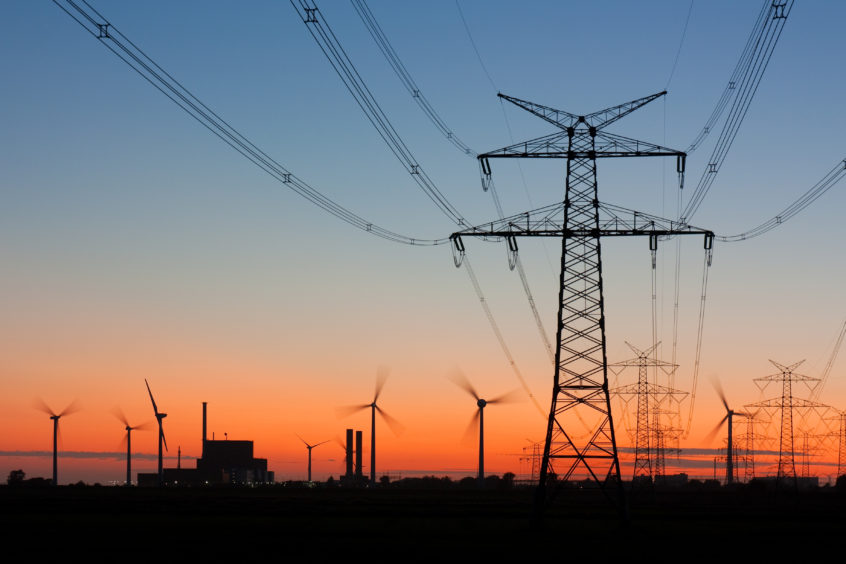
With the human population fast approaching the 8 billion mark and as the great energy transition gains momentum, so the pressure to find wholly sustainable, high efficiency low-carbon replacements for fossil fuels and to stem rising greenhouse gas levels mounts.
One of the outcomes of this hunt is that there are probably more universities around the globe than ever before engaged in energy research than at any time in the past as they seek the low carbon solutions that will transform all our lives.
Three examples of such work are described below.
There have been several false dawns over the past 100 years or so, especially the promise of endless, cheap, clean electricity generated using nuclear technologies. And, until very recently, Big Oil has sadly often sought to derail the development of low-cost, low carbon technologies development wherever possible.
But as the pendulum swings, so the pressure on research and development teams in academia and industry to catalyse the next giant leap forward grows.
But it is hugely challenging.
The classic surely has to be water electrolysis to produce endless, cheaply produced hydrogen. The splitting of water into hydrogen and oxygen was first successfully achieved in 1800.
A method of industrial synthesis of hydrogen and oxygen through electrolysis was developed in 1888 and yet today, it is still cheaper to produce hydrogen by processing hydrocarbons than attempting to split water into hydrogen and oxygen.
Cracking the water nut
One of the latest attempts to crack this nut is currently going on in the US where a team of scientists drawn from the Los Alamos National Laboratory and Washington State University claims to have made an important step forward.
The team has developed a less expensive water electrolysis system that works under alkaline conditions but still produces hydrogen at comparable rates to the currently used system that works under acidic conditions and requires precious metals as catalysts.
This advance is claimed to reduce the cost of water splitting technology, offering a more viable way to store energy from solar and wind power in the form of hydrogen fuel.
Currently the most popular system used for water splitting relies on precious metals like platinum and iridium as catalysts plus plates made from titanium, but the Los Alamos-Washington team has developed a system that uses less expensive and more abundant materials.
“The current water electrolysis system uses a very expensive catalyst; in our system, we use a nickel-iron based catalyst, which is much cheaper, but the performance is comparable,” says Yu Seung Kim, a Los Alamos team member.
It was the team at Washington led by Professor Yuehe Lin that came up with the nickel and iron catalyst idea.
Lin’s team shared their development with Kim at Los Alamos, whose team in turn developed the electrode binder to use with the catalyst.
The electrode binder is a hydroxide conducting polymer that binds catalysts and provides a high pH and, therefore, alkaline environment for fast electrochemical reactions.
The combination of the Los Alamos-developed electrode binder and WSU’s catalyst boosted hydrogen production to nearly 10 times the rate of previous anion exchange membrane electrolysers, making it comparable with the more expensive proton exchange membrane electrolyser.
“Water splitting is a clean technology, but you need electricity to do it,” said Lin. “Now we have a lot of renewable energy, wind and solar power, but it is intermittent.
“For example, at night we can’t use solar, but if during the day, we can use extra energy to convert it into something else, like hydrogen, that’s very promising.”
The global hydrogen generation market is huge and is expected to reach £160 billion in value just two years from now. Potential markets for hydrogen energy include everything from mass energy conversion and power grid management to fuel cells for cars.
Lin estimates that there are hundreds of wind farms in the US, let alone anywhere else, ready for direct connections to water electrolysis systems.
But they have to be right for the job and, while promising, the Los Alamos-Washington system has yet to be commercialised.
Smart management of turbines
Switching to managing the output of wind farms to make them more efficient, there is a team of researchers at Birmingham University Enterprise so successful that they have filed for a patent to protect their intellectual property.
Their system developed to control the storage and release of energy from wind turbines will apparently reduce the risk of power cuts and support the increase of wind energy use worldwide.
The digital system uses the variable speed of the rotors in wind turbine systems to more closely regulate the supply of power to the grid.
This means that when electricity demand is high, stored kinetic energy in the turbines can be used intelligently to keep the grid stable.
The team has already validated their approach in an industry-standard power grid simulator and is seeking industrial partners to explore commercial opportunities for the technology.
Regulating the supply of electricity to keep pace with demand is a continual challenge.
Sudden outages of power generation, such as when a generator gets damaged, can cause a frequency dip, which can lead to power cuts.
In the UK, large power stations currently manage these dips by pushing out more electricity.
However, as more wind turbines are integrated into the system, it becomes more difficult to balance supply and demand and keep the system stable, as frequency dips in the national power grid occur more quickly and more severely than before when wind generation became such a significant element of electricity generation.
Lead project researcher and smart grid director, Professor Xiao-Ping Zhang, is keenly aware that the clock is ticking.
“By 2030 wind is expected to provide half the UK’s power, so it’s important that we can use the wind farms to provide a vital safety mechanism of controlling frequency dips of the UK’s national power grid,” Zhang said.
“Our proposed frequency control system for wind turbines could revolutionise the UK power grid’s frequency control and, importantly, uses our existing infrastructure of wind turbines and it will not need additional devices and investments.
“Current methods of using wind turbines to regulate electricity struggle to provide consistent support because of variable wind speeds and other system conditions.”
The most recent severe UK power cut, in August 2019, was triggered by two almost simultaneous unexpected power losses at Hornsea and Little Barford due to lightning strikes.
Converting CO2 to syngas
Turning to the carbon reduction front, chemical engineers from the University of New South Wales (UNSW), Sydney, have developed new technology that helps convert carbon dioxide emissions into chemical building blocks to make useful industrial products like fuel and plastics.
If validated in an industrial setting and adopted on a large scale, it is claimed the process could give the world breathing space as it transitions towards a green economy.
The researchers, who carried out their work in the Particles and Catalysis Research Laboratory at UNSW, led by Professor Rose Amal, show that by making zinc oxide at very high temperatures using a technique called flame spray pyrolysis (FSP), they can create nanoparticles which act as the catalyst for turning CO2 into syngas — a mix of hydrogen and carbon monoxide used in the manufacture of industrial products.
The researchers say this method is cheaper and more scalable to the requirements of heavy industry than currently available processes.
They used an open flame, which burns at 2,000 degrees Celsius, to create nanoparticles of zinc oxide that can then be used to convert CO2, using electricity, into syngas.
“Syngas is often considered the chemical equivalent of Lego because the two building blocks — hydrogen and carbon monoxide — can be used in different ratios to make things like synthetic diesel, methanol, alcohol or plastics, which are very important industrial precursors,” says team member Emma Lovell.
“So essentially what we’re doing is converting CO2 into these precursors that can be used to make all these vital industrial chemicals.”
In an industrial setting, an electrolyser containing the FSP-produced zinc oxide particles could be used to convert the waste CO2 into useful permutations of syngas, said Rahman Daiyan, researcher at UNSW.
Waste CO2 from say, a power plant or cement factory, can be passed through this electrolyser with its zinc electrode where it is converted to a mix of CO and H2.
The researchers say that, in effect, they are closing the carbon loop in industrial processes that create harmful greenhouse gases.
And by making small adjustments to the way the nanoparticles are burned by the FSP technique, they can determine the eventual mix of the syngas building blocks produced by the CO2 conversion.
Recommended for you
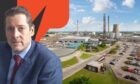