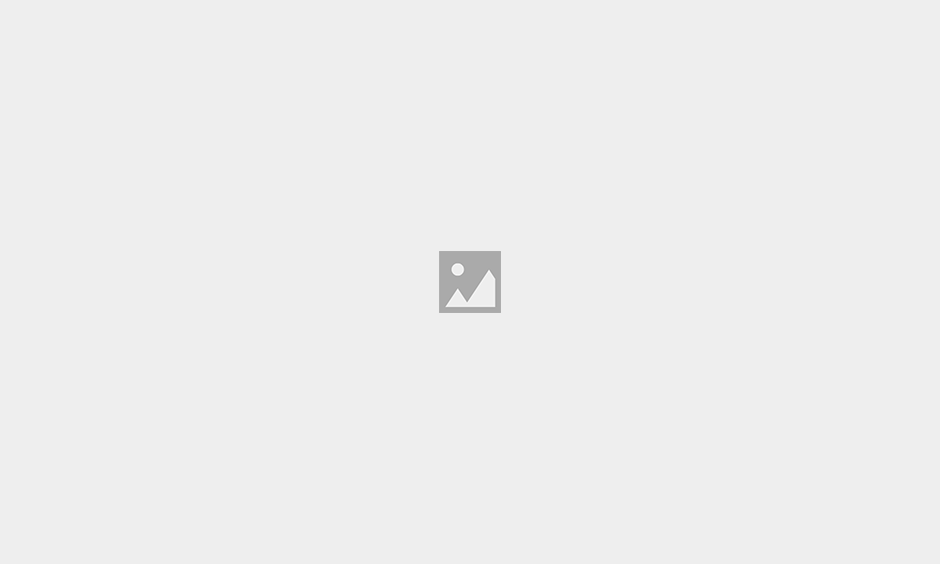
The UK’s Energy Technologies Institute (ETI) is seeking partners for a new £13million project to help design and build a next generation energy from waste demonstrator plant to convert typical wastes into electricity and heat.
It is yet another indication of just how active the ETI appears to be as it also has a call out for interest from companies and other organisations interested in coming up with a viable means of monitoring carbon dioxide storage in subsea geologies.
The energy from waste demonstrator sits within the ETI’s Bio-energy programme.
The objective is to commercially demonstrate how such a plant can create energy from waste, and produce energy at efficiencies higher than previously achieved.
It is hoped the plant could be designed by 2014 and operational by 2016.
The ETI has issued a request for proposals for interested parties and the deadline set for notification of intention to submit a proposal is June 7, with July 2 set as closing date for submissions.
Commenting on the project, Dr David Clarke, CEO of the ETI said: “Bio-energy should be a key component of any future energy systems mix to meet the demands of providing affordable, clean and secure energy. We have already completed an extensive analysis of the existing energy from waste technologies, as well as the breakdown of typical UK municipal, commercial and industrial waste.
“From this research we believe that improved technology for the integrated gasification of waste together with gas clean-up and subsequent combustion of this cleaned gas in either a gas reciprocating engine or turbine would provide an effective and efficient solution.
“Our modelling indicates that such a plant design could operate at a net efficiency of 25%, which significantly exceeds the performance of current plants in operation.
“Successful design of such a plant also provides an opportunity to move away from the inefficiency and reducing availability of landfill sites. This waste could contribute up to 4% of UK energy by 2050.”
The UK produces around 33million tonnes of municipal solid waste (MSW) and 72million tonnes of commercial and industrial waste (C&I) annually.
It is estimated that this waste could contribute up to 2-4% of UK energy by 2050, assuming this is applied to combined heat and power (CHP) schemes, with appropriate technology advancement.
The current practice of waste to landfill can lead to significant emissions of methane and CO2 from landfill, which is estimated at 15-20million tonnes of CO2 equivalent per year for the MSW and C&I components.
However, this is currently being addressed by EU legislation with a view to curtailing the production of greenhouse gases from landfill.
By 2016, EC member countries must reduce the amount of biodegradable waste to landfill by 35%.
And, by 2025, the EC Landfill Directive will compel appropriate treatment with no biodegradable waste to landfill allowed.
It is estimated that it will cost £10-20billion in the UK alone to meet the 2025 proposed EC Landfill Directive.
Europe-wide and the capital cost may be in the range £100-200billion.
Currently for dry wastes, incineration with CHP, and or derivative incineration technologies are the predominant technologies deployed for energy from waste (EFW) schemes. Approximately 10% of the current UK waste is incinerated.
It is believed that advanced thermal conversion (ATC) schemes could operate at significantly higher efficiency than incineration-based systems, with the production of gas that could be used in gas engines/turbines to produce electricity and heat, or injected into the grid.
There is also the opportunity to develop more technically-stretching plants with the potential for this gas to be used to create transport fuels and chemicals.
The ETI has over the past two years completed extensive analyses of both energy from waste technologies, and the composition of typical UK waste (both MSW and C&I).
It believes that integrated gasification of waste with gas clean-up and the subsequent combustion of the cleaned gas in a gas reciprocating engine or gas turbine offer the best way forward, in terms of improved flexibility and higher recovery efficiencies.
The vision is to design and built a first of a kind test demonstrator by end-2015, enabling such a plant to be operational by 2016.
Recommended for you
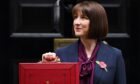