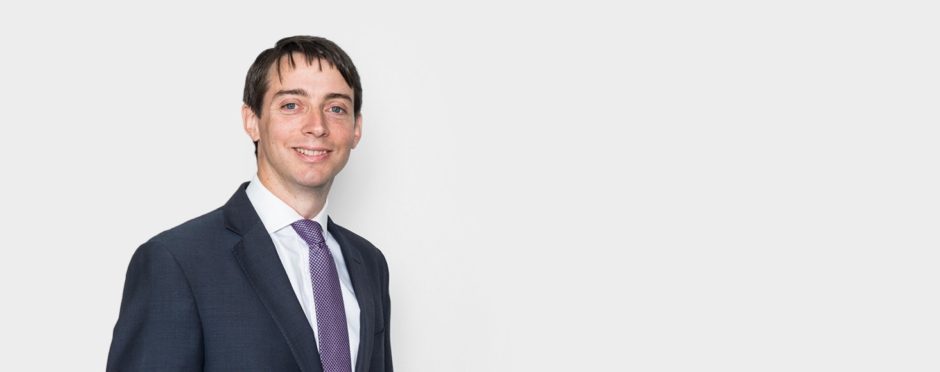
The global EPC market was estimated to be worth over US$7.5 trillion in 2019.
It is reported that only around one in four EPC projects complete within 10% of the deadline for completion and budgeted cost, and that 98% of the largest EPC projects come in over budget or are delayed for some reason, with 75% of these mega projects being at least 40% behind schedule.
Evidently, therefore, whilst being a well-established method of contracting and delivering complex projects, EPC contracts continue to foster significant claims for delay and disruption and a wider range of claims with costs attached to them.
HKA’s CRUX Insight 2020
Overview
HKA’s CRUX Insight 2020 is the product of investigations into more than 1,100 projects across 88 countries that generated claims or disputes. The average cost claimed, related to delay, disruption and other quantum claims, across the EPC projects investigated was over US$140 million, or 47% of the original contract value, with the average extension of time claimed being 60% of the original contractual period.
Comparing EPC with non-EPC projects there is a clear reduction in both EoT and costs claimed under EPC contracts. However, there still remains notable durations and amounts claimed, with nearly 50% of original contract amounts being claimed. This appears to be disproportionate to the principle of risk allocation underlying an EPC arrangement.
EPC Causation
The data includes a level of granularity of causation that can be useful in pin-pointing specific areas of concern. These levels can be combined in groups to show general areas of concern. For example, the three “design” related causations combined identify primary causation of claims and disputes on 18% of EPC projects:
Following Design issues, Worldwide, across all sectors, the standout cause of disputes is “Changes in scope” closely followed by “Contract interpretation issues”. These two issues alone were found to be the primary or secondary cause of 17% and 14% of disputes on EPC projects respectively.
Design Issues
The most frequent primary causations were Design related issues. This goes to exemplify the importance of clients sufficiently planning their deliverables, usually made via an engineering company that frequently both manages aspects of the design and the administration of the contract.
When entering into an EPC contract it is evidently important to ensure that the programme of works includes or in some way addresses the need for elements of design input at certain stages. It is of equal importance that the client and its engineer, understand prior to entering into such a contract what will be needed and when, and key deliverables be set out within the agreement between the client and engineer, to ensure any such transfer into the EPC contract be met and upheld as required. The implementation of sufficient and appropriate controls will reduce the claims and disputes between the parties.
Changes in Scope
All but one of the sectors have changes in scope as the leading primary cause of claims and disputes. “Industrial”, however, included change of scope as the eighth-ranked primary causation, at only 5%.
The Industrial EPC projects in the CRUX data also show a significant reduction in both claimed EoT and cost, both as percentages of the original period/contract amount compared to the EPC average for all project types.
It appears, therefore, that Changes to Scope are significant both in prevalence of occurrence but also level of impact for non-Industrial EPC contracts (which rely heavily on functional performance specifications). Investment taken pre-contract to fix the requirements, will reap benefits in reducing exposure to additional cost and time claims once the project is underway.
Clients should endeavour to ensure that sufficient time and effort is expended in the specification and FEED phases of the project. This will ensure that the specifications that form the basis of a contract are sufficiently detailed, contain sufficient certainty and when implemented, will reduce the need for changes in scope. Clients may elect to utilise a two-stage tender process that will allow more client input in the detailed design phase, allowing the client to continue expanding its requirements without a commitment being made by the contractor as to time and cost of delivery meaning disputes are less likely to arise.
Contract Interpetation
With reference to the high level of contract interpretation causation, the majority of EPC contracts are entirely bespoke. As such, it is likely that issues around contractual interpretation are predominantly due to a lack of clarity and certainty in the conditions and specifications. This inevitably leads to the parties adopting polarising views on matters, frequently leading to a dispute.
In the wider construction industry, it is generally accepted that the most effective way to reduce the overall risk to projects is to use standard forms of contracts with amendments to suit the project’s circumstances. This is likely to reduce ambiguities, fairly allocate risk and use clauses which have largely been tested in the courts and therefore have legal precedence. Clients should consider adopting a standard form such as FIDIC Silver Book or, alternatively, ensure that bespoke contracts are drafted clearly and without any ambiguity. This will, in turn, leave very little room for interpretation by either party and thus reduce the occurrence of disputes.
As such it is of crucial importance that EPC contracts are both thoroughly reviewed and, in addition, “stress tested”, with varying example theoretical issues worked through so the contractual mechanisms can be checked for their sufficiency.
Summary
It is clear that establishing and monitoring robust design development controls and practices, investment in the early stages of the project to properly and clearly define the requirements, along with ensuring the contract is well-drafted, have value in mitigating the risk of claims and supports the potential to minimise cost and time overruns.
Charles Wilsoncroft is a Partner at HKA with over 20 years’ experience in the construction industry. He is a Chartered Civil Engineer who has gained broad experience working for a main contractor, a public-sector client organisation and now an international consultancy. During his career he has been involved in all manner of procurement, contract training, project management, contract management and contract administration including dispute resolution, expert witness provision and final account settlement. He has experience across a range of EPC projects and regularly advises clients in respect of such.