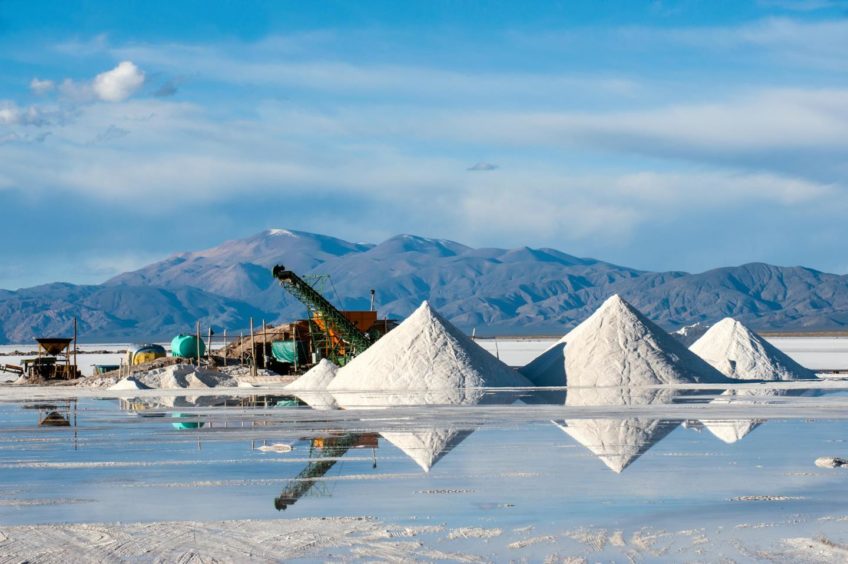
As the curtain falls on the Age of Hydrocarbon Man and the transition towards a more sustainable low carbon future gathers momentum, it is important to recognise the sheer scale of the effort required.
There have been various energy transitions in human history, the most profound being the switch from burning biomass to extracting and burning fossil fuels.
The one we are embarking upon today is fundamentally different to all prior changes along the energy consumption road. It is born out of crisis rather than wealth creation.
And the scale of the challenge is barely imaginable.
Seeking to exchange our high-carbon habit for a more sustainable low-carbon approach is already exposing deeply uncomfortable challenges.
Among the most obvious is the wholesale closure of fossil-fuelled and nuclear generation plant in favour of harnessing wind, oceans and solar, especially.
This will require wholesale changes to transportation, large-scale replacements for the feedstocks required in the manufacturing of thousands of goods.
And we need major upheavals in sourcing minerals such as lithium, currently favoured for the high performance, long endurance batteries for electric vehicles (EVs).
As we change our ways, there is a serious need to get to grips with exactly what that means.
Which is precisely what the International Energy Agency and, separately, a German research institute have been trying to do. Both recently published their initial findings, which are eye-opening.
The IEA’s report is titled, The Role of Critical Minerals in Clean Energy Transitions, while the Nova Institute has just published Turning off the Tap for Fossil Carbon.
They are very different in their approach and point to massive decarbonisation of the human way of life that may prove hugely disruptive.
The IEA’s minerals report, which received less attention than its net-zero by 2050 roadmap of May 18, identified risks that could make progress towards a clean energy future slower and/or more costly.
It warned that installing solar photovoltaic (PV) arrays and wind farms and manufacturing electric vehicles required more minerals than their fossil fuel-based counterparts.
A typical EV requires six times the mineral input of a conventional car.
And an onshore wind plant requires nine times more mineral resources than a gas-fired power plant.
The IEA says that, since 2010, the average quantity of minerals needed for a new unit of power generation capacity has increased by 50% as the share of renewables has risen.
Which mineral resources are utilised varies according to technology.
For example:
• Lithium, nickel, cobalt, manganese and graphite are crucial to battery performance, longevity and energy density;
• Rare earth elements are essential for permanent magnets that are vital for wind turbines and vehicle motors;
• Electricity networks need a huge amount of copper and aluminium, with copper being a cornerstone for all electricity-related technologies.
The shift to a clean energy system is set to drive a huge increase in the requirement for these minerals.
Until the mid-2010s, the energy sector represented a small part of total demand for most minerals. However, as energy transitions gather pace, clean energy technologies are becoming the fastest-growing segment of demand.
The IEA warns: “In a scenario that meets the Paris Agreement goals, clean energy technologies’ share of total demand rises significantly over the next two decades to over 40% for copper and rare earth elements, 60-70% for nickel and cobalt, and almost 90% for lithium.
“EVs and battery storage have already displaced consumer electronics to become the largest consumer of lithium and are set to take over from stainless steel as the largest end user of nickel by 2040. But lithium sees the fastest growth.”
Raw material costs are on the rise, accounting for some 50-70% of total battery costs, up from 40-50% five years ago.
The IEA calculates that higher mineral prices could have a significant effect: a doubling of lithium or nickel prices would induce a 6% increase in battery costs.
If lithium and nickel prices were to double at the same time, this would offset all the anticipated unit cost reductions associated with a doubling of battery production capacity.
In the case of electricity networks, copper and aluminium currently represent around 20% of total grid investment costs.
Higher prices as a result of tight supply could have a major impact on the level of grid investment.
The IEA says: “Expected supply from existing mines and projects under construction is estimated to meet only half of projected lithium and cobalt requirements and 80% of copper needs by 2030.”
Metals recycling has the potential to be a significant source of secondary supply, although it comes with its own set of challenges.
For some metals, such as aluminium and copper, global stock and recycling pathways are relatively well established.
That said, recycled input rates for metals such as these have not changed much in recent years, meaning that improved recycling activities have only managed to keep up with demand growth
However, for many metals, global stock assessments are scant or only examine discrete sub-sectoral applications, making recycling potential difficult to assess.
As for lithium-ion batteries, there is considerable scope for growth as only 5% are presently recycled, though the IEA report appears to overlook this.
It warns that the Li-ion recycling industry still needs to address several challenges to reach scale and profitability. Some of these are technical constraints, and others involve economics, logistics and a lack of streamlined policies
Economies of scale play a major role in improving the economic viability of all types of recycling, and increasing collection and sorting rates is a crucial starting point. In this context, the IEA points out that government policies can play a major role in facilitating waste collection.
NOVA SLANT
Nova focuses on carbon contained in organic chemicals and derived materials that conventionally use high shares of virgin fossil resources.
These include:
• Plastics, mainly thermoplastics, but also thermosets and elastomers or rubber;
• Man-made fibres such as polyester;
• Organic chemical substances such as adhesives, solvents, detergents, paints, etc.
The chemicals industry is the backbone of the modern world. Almost all everyday products are largely derived from chemistry.
The sector today relies on virgin fossil carbon as a building block. As such, its challenge is to convert its feedstocks to renewable carbon.
The use of renewable carbon in the chemicals and derived materials industry is key to climate change mitigation.
“But how can we ensure this change happens?” asks Nova. “Are the technologies that can enable this change already developed and mature? Is there enough arable land for biomass? Can we really harvest CO2 from the air? Can recycling turn old plastics into food packaging and detergents?”
The chemicals industry is a highly interconnected, integrated industry and has been optimised in many ways over decades.
Therefore, if the current system is to be fundamentally changed, well-considered strategies will be needed.
Nova points out that comprehensive carbon management needs to take full account of the structure of today’s chemicals industry, preserve or repurpose industrial assets where possible, and replace those that have no future.
Significant quantities of chemicals – 10-15% depending on world region – are produced from biomass feedstock.
Today, the worldwide annual supply of biomass is 12.3 billion tonnes. Nova claims this could reach 25 billion tonnes by 2050.
However, any expansion must pay strict attention to food security and biodiversity loss. Experts see potential for sustainable expansion and, above all, prospective yield, efficiency and storage improvements.
Despite sometimes unfavourable public perception, Nova claims food crops are often a good choice for industrial utilisation, as they produce high yields per hectare, and often provide protein-rich by-products.
Another option is to use the land and facilities that are currently used for biofuel production, as the demand for liquid fuels is set to dwindle over the next few decades due to the rise of electric cars.
They say too that advanced biodiesel is almost identical to naphtha and ethanol, and can easily be used to produce ethylene, a building block for PE and PET plastics.
There are also some promising approaches for the use of marine biomass, such as micro and macro algae, according to Nova.
While they have not yet penetrated mass markets, however, they are used for products such as cosmetics and food supplements. The institute doesn’t mention that the alginates industry has been around for more than a century, but that marine biomass lags far behind agricultural and forestry systems.
CO2 PROMISED LAND
Energy Voice has occasionally touched on direct utilisation of CO2 but technologies being developed to achieve this are early stage.
There are almost endless source of renewable carbon in the carbon dioxide and monoxide of exhaust gases, waste air and the atmosphere.
Nova says each of these may be used as a raw material for the chemicals industry through a number of different technologies.
Turning to carbon capture and utilisation (CCU), Nova points out that the chemicals industry offers a wide range of opportunities where CO2 can be used as feedstock for chemicals, polymers, fuels, minerals and even proteins.
Unfortunately, to make the carbon contained in CO2 re-usable, it must be chemically reduced, which requires large amounts of energy, mostly in the form of hydrogen.
Nova said: “From an ecological standpoint, this means that only renewable energies or existing process energy can be used.
“For this reason, looking ahead, there must be massive, worldwide growth in renewables.
“Based on current trends it is possible to say that this transition is achievable, as many energy systems around the world are already shifting towards renewable options.
“The big advantage of CCU technologies over biomass is their high land efficiency and ability to use inarable land types like deserts.”
But Nova admits downsides to CCU, namely, high costs, energy requirements, and the need for construction of new infrastructure.
Nova continues: “Since the beginning of the industrial revolution, humanity has almost exclusively relied on cheap virgin fossil carbon sources such as coal and crude oil for its development.
“Today, for the first time, we can now decouple the production of chemicals and derived materials from the use of virgin fossil carbon.
“All of today‘s chemicals and derived products can be made with renewable carbon from biomass, captured CO2 or recycling.
“Technologies and investment capital are available for the transformation from fossil to renewable carbon for the entire industry.
“The renewable carbon family is the only pathway to a truly sustainable future for the chemicals industry,” adds Nova.