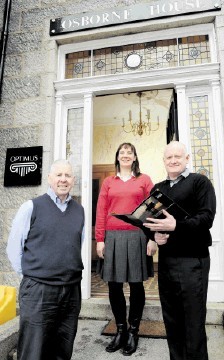
Optimus, the Aberdeen-based oil and gas engineering consultancy business, is saving energy industry operators’ and contractors’ time and money thanks to its growing business improvement capability.
This specialist division has experienced rising demand for its expertise in providing insight and helping solve problems and that demand comes from a broad spectrum of companies . . . large, medium and small and with different corporate styles and cultures.
Peter Stock, leader of the business improvement team, said: “We particularly enjoy tackling ‘hairy’ problems – something where the standard approaches don’t work. Our team’s skills lie in facilitation, numerical modelling and innovation to help people appreciate the subtleties of their problems. It’s about helping people come to decisions in an environment of uncertainty.
“We inhabit that space between the technical and managerial worlds. A lot of our skills lie in interpreting technical issues for management consumption; making the technical case to sometimes non-technical people. That tends to be where we are most effective.”
The team is drawn from a diverse range of disciplines and deliberately so as this creates the valuable range of tools and experience that imparts the art of business improvement and which takes account of the need for that desirable technical stewardship.
It is about gaining the attention of management subtly and effectively and being able to achieve this, regardless of the corporate overlays already referred to and the pressures that make it increasingly difficult for decision-makers to have the time to reflect on strategic decisions that they would prefer. Optimus’ business improvement group facilitates decision-making and risk identification through workshop sessions and a range of qualitative and quantitative techniques. Qualitative techniques include risk and opportunity identification, constructability reviews, decision analysis, due diligence auditing, “regulation 5” auditing and operational readiness auditing. Quantitative analysis extends these skills using numerical modelling to typically cost and schedule risk predictions.
At its most advanced, numerical modelling is used to make probabilistic platform availability and production efficiency predictions for use in field economics, platform configuration decisions, develop obsolescence strategies and capital spares holdings decisions.
Stock said: “We have streamlined our workshop processes to minimise the demand on people’s time and reach decisions quickly and efficiently. We particularly pride ourselves in running efficient workshops that concentrate on data capture, not processing, and in getting people back to their desks as quickly as possible. Most workshop sessions last just half a day.
“The business improvement area of the industry can be more of an art than a science; it’s more organic and very personality-based. It relies on a blend of experience, analysis tools and innovative thinking to bring about results.”
That said, how does he know that the approaches used by the Optimus team actually strike the right balance and are effective?
“All of our work tends to come from repeat business . . . recommendations. So I’m guessing that what we offer does work. Another of our ‘calling cards’ is that we try to have an operations engineer’s approach to a lot of our work; by that I mean someone who is working in an oil company and who needs an approximate answer quickly as opposed to a perfect answer eventually to enable to get on with their job . . . task in hand.”
The Business Improvement group has worked with most major oil and gas companies and integrated service contractors in the North Sea and overseas, including Holland, Norway and St John’s Newfoundland.
One recent example is that of qualitative decision-making applied to a project in the Caribbean. During a half-day workshop, decisions on many aspects of the project were made from technology selection to onshore terminal location. This allowed poor options to be eliminated early on so as to concentrate on the likely winners.
The team’s numerical modelling skills have been recently applied in the North Sea to tanker offloading uncertainties and the impact on platform availability, including the “what-if” impact of alternate-sized tankers with different connection and loading envelopes.
A fresh innovation is that, from this month, Stock and his team are to offer half and one-day risk awareness training so that clients become more proactive about realising the need for risk management.
The emphasis is on brevity; not least because upstream oil and gas is populated by intelligent people whose diaries are packed and therefore where time is at a premium.
Optimus was established in 1999 by director Ian Bell. The company provides a wide range of engineering consultancy, including process, facilities and safety engineering, and project execution. Over the last five years, Optimus has completed $130million of capital projects in Europe and Africa and, besides the UK, the company has bases in Bangkok, Thailand, Perth, Australia, and Varna, Bulgaria.
The Optimus business improvement team comprises:
o Peter Stock, who is structural engineer by trade, ex-Conoco, DNV and Aker Kvaerner and set up business improvement at Optimus in 2006;
o Catriona Wilson has a degree in risk management, is ex-KPMG and joined in 2008;
o Sarah Stalker is also ex-Conoco, is a mechanical engineer by discipline, joined in 2010 and is currently based in Perth, Australia;
o New recruit Sean Gallagher is ex-PSN, brings maintenance experience and joined in February 2013.