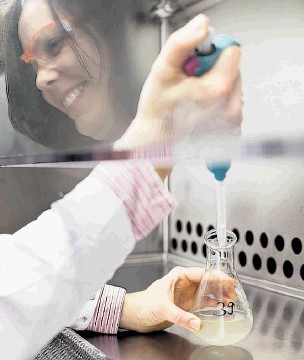
Germany’s largest oil and gas company Wintershall has started testing a new recovery enhancement technology with its parent BASF.
The new bio-polymer, which is being produced in the labs of chemical giant BASF, is being pumped down two wells at the Bockstedt oil field in northern Germany to see if it can extract more than existing synthetic polymers under high saline conditions.
Wintershall scientists are confident that the new bio-product, which is produced by a common mushroom, will indeed not only outperform traditional polymers in its ability to function in salty water, but also at temperatures up to 135degC.
With profitability of mature wells heavily dependent on every extra percent of oil that can be squeezed out, the German firm is excited about the possibility for this new product to be utilised in deeper, hotter offshore wells where it has not previously been possible to apply chemical flooding effectively.
Wintershall’s recent expansion in the North Sea helped to lift its sales last year by 39% to £14.4billion, with net profits after tax up 13% at £1billion.
The company expects production to increase to at least 160million boe per year by 2015.
Martin Bachmann, director of exploration and production, told Energy that Wintershall’s strategy had three strands, including organic growth and “balancing our portfolio through acquisitions like we did last year with Statoil”.
The third strand would be through technological advances to boost oil recovery, he added.
Wintershall’s two-year biopolymer field test started last December and the company, which has set a target of 50% recovery across its production business, hopes that the recovery rate from reservoirs can be increased by around 10% with the help of the biopolymer, or schizophyllan as it scientifically known.
Bernd Leonhardt, project manager and head of research at Wintershall, said: “Schizophyllan offers us a fantastic opportunity.
“We can set ourselves apart from the competition as a specialist in a technology developed by us and position our company on the market as an attractive partner, especially for national oil companies.”
He said that the idea came out of research at the University of Braunschweig which identified the loss in viscosity of synthetic polymers in high saline conditions as the challenge to overcome.
After several years of development the BASF labs are now producing 30 tonnes of the new bio-product per year.
Leonhardt said that experiments so far had showed that the biopolymer has also increased resistance to “sheer” allowing greater pumping efficiency.
It has also been shown to continue working in much higher levels of salinity and heat that its synthetic counterparts currently use in the US and China.
To maximise the recovery of hydrocarbons from a reservoir, several methods can be used after the natural depletion stage is over.
Polymer flooding is a well-known method of chemical enhanced recovery and involves dissolving a polymer in water to increase its viscosity, which is then injected into the reservoir to help “push out” the oil.
An ideal polymer withstands mechanical shear during pumping and injection operations, does not degrade too fast, works in saline conditions and operates in a wide range of temperatures.
Leonhardt said: “The test has started well and is running as planned around the clock.”
The polymer is mixed with reservoir water and a preservative agent to limit bacterial growth and is then pumped into the injection well.
Just a fraction of a percent is required to thicken the water by a factor of 25. By the end of its journey flowing through the rock, this polymer fully biodegrades.
He added that the first results are expected at the end of this year as to how the polymer behaves in the reservoir and if more oil is being extracted with one of the wells.
Key to the success of the project is reducing production costs and avoiding contamination of the reservoir by bacteria.
There are around a hundred staff in both Wintershall and BASF working on the project with hard costs for the testing alone estimated at more than £35million.
Although, the schizophyllan polymer cannot be patented, the firm has five or six patents on the production process that involves mixing the fungus with sugar and oxygen for several days in a process that is similar to producing beer.
Different strains of the polymer-producing mushroom, which is commonly found all over the earth on dead wood, have been combined to optimise the production of the gel-like schizophyllan that it uses to build its cell walls.
The substance has been used by different cultures over the ages as a food supplement, medicine and even a chewing gum.
Wintershall is not planning to offer the product “off-the-shelf” but through working partnerships such as the agreement signed last year with Norway’s Statoil to investigate applications for the technology.