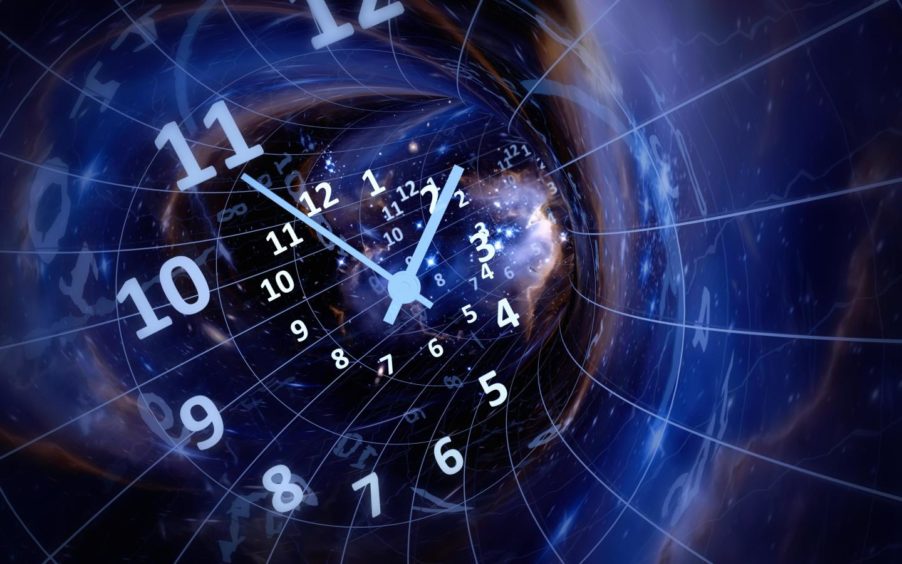
“Those who cannot remember the past are condemned to repeat it” – Spanish philosopher George Santayana.
That idea is causing more than a few sleepless nights in the oil and gas industry. Vital knowledge, captured in the experiences of long-standing employees, is leaving to enjoy its retirement. It’s a crucial element of the impending skills crisis, and one that seems hardest to remedy, leaving younger cohorts without the institutional memory and experience needed to make light work of recurring challenges.
But it’s not just about learning from the past. There are new challenges to overcome and new mistakes to avoid. The focus has to be on emerging issues: the demand for more efficient, greener operations, less hazardous working environments, and a considered look at total expenditure. Above all, the industry needs to direct effort to more sustainable and socially supportable modes of production.
The good news is that although engineers and project managers have certainly been essential repositories of problem-solving, risk-mitigating, cost-saving experience – they aren’t the only ones.
That information is also stored in every moving part, every maintenance record, every intervention decision of every well around the world – from reservoir to topside, and from first exploration to ongoing operation. The challenge has always been: how to access the data and how to make it usable.
Our industry has vats of data. Lakes of data. When it comes to subsea operations, we literally have oceans full of data. What we haven’t had, so far, is an open mindset to data collaboration alongside technology that is sufficiently advanced – or regarded as sufficiently reliable – to turn it into the mainstay of the decision-making process. Whatever insight it has given us has had to be checked against the experience of experts.
That is now changing. Fast. Even five years ago, true digital enablement was more powerful in its potential than in its reality. But today, we have sophisticated and advanced sensors to extract that data. We have the analytics and machine-learning capabilities that can transform it into predictive insight. And we have the visualisation techniques that make it accessible to everyone outside the data-science team.
That enables us to use data in new and powerful ways. Instead of collecting information
about fields and how they operate as an administrative exercise – as operators have for decades – we are now in a position to turn that data into operational and management tools resulting in safety, production and CO2 reduction benefits. Gathering data from equipment around the world that has collectively been operating for centuries, we can get a really accurate picture of how it will behave in certain conditions. Going beyond predicting failure modes based on statistical analysis, or assuming a fail after 20,000 hours of operation, we can now see whether additional stresses are likely to fall within or without the operational safety envelope. We can make informed assessments on how changes to operating conditions will impact the overall business. We can switch to more risk-based management.
In short, we can unlock the secrets of the past, and use that newly acquired wisdom to make the right choices today and inform the decisions of the future. We have built ourselves a time machine.
And just like any good time machine, it has arrived at just the moment it is needed most.
It’s not just that important members of the workforce are reaching the end of their careers. Many fields are reaching end of predicted life. At this point in the industry’s trajectory, the cost and risks of developing new fields is increasing exponentially – just when market conditions demand the opposite.
At the same time, the equipment designed and built specifically for these aging fields is coming to the end of its design life – again when those same external conditions demand smaller manufacturing footprints, reduced resource consumption, lighter weight logistics, just-in-time spares inventories, minimal tooling and all the rest.
What the time machine can do is look to the past to establish whether and how much productive life still exists in aging fields – and how much safe, operational life remains in the assets needed to make that happen. At Baker Hughes, we are able to look back over decades at the biggest installed base in the industry to predict field activity, work with operators to develop the right solutions for those specific circumstances, optimise installation and ultimately accelerate time to valuable, viable production; all fundamental benefits driving our Subsea Connect business model.
Our operators can pause, rewind and assess rather than galloping off into an unknown or uncertain future. They can consider the most accurate evidence they have ever had and make the right series of decisions whether for an entire field or a single asset.
The same is true at any stage of an asset’s life. Operators can use the time machine to see how equipment has actually performed in the field, and then fast forward to forecast and determine optimal asset management, controls, proactive maintenance and interventions from the very beginning of an asset’s life. In fact the prediction business can start before construction even starts.
This is the kind of future-first mentality that our industry needs. And we believe it can produce optimal results that reduce TOTEX to create much more sustainable developments – and minimise the interaction between humans and hazardous environments and equipment to improve safety.
We also know that data and digital expertise alone is not enough. The industry as a whole has to move into a more collaborative way of working. First of all, the data itself has to be agnostic. Aggregating and anonymising techniques are necessary to ensure that data can be pulled from equipment manufacturer or operator without impinging upon intellectual property rights; so too can a flexible approach to building solutions based on data and managing its ownership.
That comes back to the relationship between operator and service provider. Digital enablement of subsea equipment and services is inevitable. It is no longer the capability of the technology that is holding back progress, but questions of reliability and trust. As digital technologies become more embedded – and shake off any lingering sense that they are a hype-driven gimmick – that trust will increase.
But to get there, we also need transparent relationships and collaborative development projects; shared risk and commercial models that reflect that. The days of the noble Time Lord with his obedient earthly assistant are gone from our TV screens, and we need to stop replicating that model in subsea operations. We can remember our past – but we must do more than just remember. We must interpret all of its learnings to create a more informed, successful future.
Recommended for you
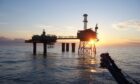