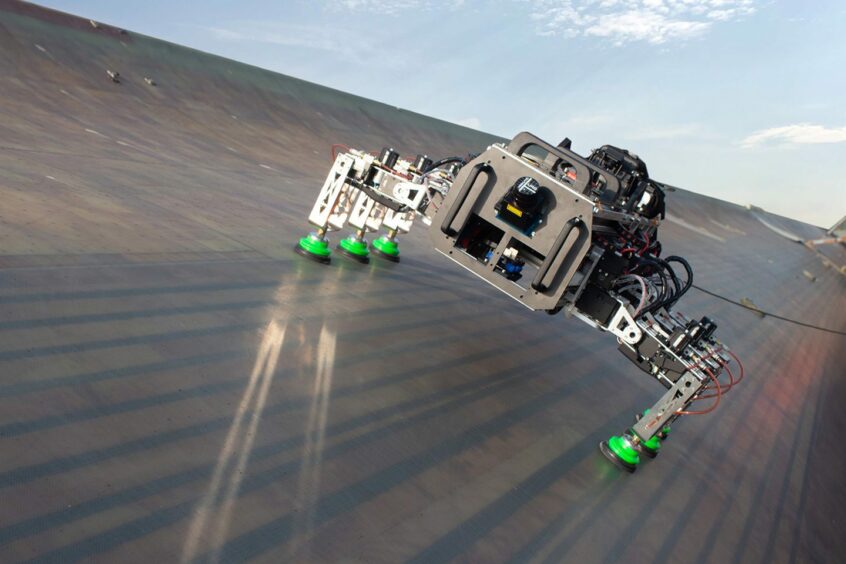
An ingenious robotic solution could halve the time it takes wind farm operators to inspect turbine blades.
In around 35 minutes, the BladeBUG advanced robot can be deployed to investigate areas of concern on a turbine blade.
In doing so it can majorly reduce downtime when carrying out essential maintenance tasks or inspecting damaged turbines.
Traditionally, rope access teams have had the job of carrying out inspections and repairs of blades.
But it takes over an hour for a team of qualified technicians to get kitted up, hoisted to the correct height and inspecting a blade.
They also come at a cost, and have to carefully manage safety risks as they work at great heights and sometimes in harsh weather conditions.
The BladeBUG removes those perils for workers, and can be deployed relatively easily on both onshore and offshore wind turbines.
Chris Cieslak, director and founder at BladeBug, said: “We designed the BladeBUG to reduce costly turbine shut downs for our wind energy clients. As the UK focuses its energy supply on renewable sources such as wind farms, it is imperative these projects operate as efficiently as possible.
“Once our team has arrived on site, unloaded the BladeBUG and carried out our safety checks, the robot will be attached to a blade and carrying out inspections in a little over half an hour. While vacuumed onto a turbine blade the BladeBUG is able to walk around to any areas of interest.
“Because the robot can be navigated to different locations on huge blades very quickly, this reduces turbine downtime. The BladeBUG also provides cost savings for wind farm operators as it removes
the need for employing rope access teams and allows preventative maintenance to be carried out at an earlier stage to increase turbine efficiency.”
The latest round of testing was successfully carried out at the Offshore Renewable Energy (ORE) Catapult’s National Renewable Energy Centre in Blyth.
Andrew Stormonth-Darling of ORE Catapult, said: “It has been a privilege to be a part of the BladeBUG journey and watch Chris and the team develop such a vital piece of technology for the industry. The BladeBUG continues to go from strength to strength, and this latest test in Blyth is another tick in the box for the future of innovative wind turbine inspections.”
Recommended for you
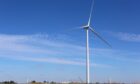