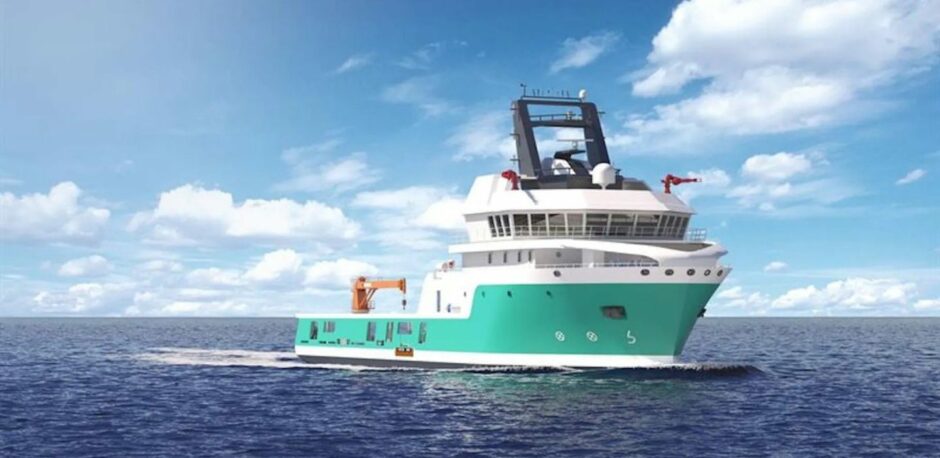
Oil-related supply boats have largely been pushed to the back of the new offshore support vessels orders book as global energy priorities change, driven by climate change.
It is some time since this column touched on new OSVs, so it’s rather refreshing to open with an offshore Malaysia development where the American Bureau of Shipping (ABS) is involved in the development and construction of a supply boat which will feature batteries as a key part of its propulsion system.
The new generation OSV will be designed to ABS Rules, and ABS New Technology Qualification (NTQ) procedures will evaluate the Blue G battery system (Gennel Engineering is the supplier) to be fitted. This power source can be charged by generator sets onboard as well as from onshore including via “cold ironing” (plug-in).
ABS says that, with this technology, the vessel will save fuel and reduce its carbon footprint, operational expenses and life cycle costs.
The (shipping) industry needs to implement green technologies to reduce greenhouse gas (GHG) emissions, and ABS is among various classification bodies at the forefront of this challenge.
Delivery of the project is via a partnership of companies and is being supported by ABS Engineering in Singapore, which is also home to one of ABS’s Sustainability Centers of Excellence, part of a global network of five similar centres suited to support this type of technology development.
The partnership comprises three shipbuilding and ship repair (SBSR) companies in Malaysia. They are Grade One Marine Shipyard (GOMS); Muhibbah Marine Engineering (MME); and Shin Yang Shipyard (SYS).
Design-work is to be led by Evolution Concepts together with partners like Gennal Engineering, MacGregor, Raytheon Anschuetz Singapore and Sindex Refrigeration.
Construction of the ship is expected to begin next year and take 18-24 months; which is a sedate pace by Far East shipyard standards.
De Beers flagship starts diamonds hunt
From time to time along the years, Energy Voice has touched on subsea mining, an industry that is quietly developing offshore Africa in particular – keeping its head down so to speak as it stirs controversy.
The UK contribution to this industry is surprisingly large, including the development and manufacture of sophisticated subsea dredging plant. A tank-like pioneering seafloor crawler unit was even designed and built in Aberdeen in the 1990s.
The latest development in this industry is the arrival and successful career start by the purpose designed 177m mining ship Benguela Gem, which was built by the Dutch shipbuilder Damen at its Mangalia facility on Romania’s Black Sea coast.
Designed by Norwegian naval architecture firm Marin Teknikk, Benguela Gem is owned and operated by Debmarine Namibia, a joint venture between the government of this West African state and UK-based diamond mining and jewelry company the De Beers Group.
Benguela Gem is the largest purpose-built diamond recovery vessel in the world built thus far and is a lot heftier than De Beers next largest vessel, the 174m Mafuta.
It is kitted out with modular mining equipment based on subsea crawlers developed in Cape Town, South Africa and which has an operating envelope of 90-150m water depth. Dredgings are delivered to the vessel for processing.
This processing equipment then discharges around 99% of any gravel collected during diamond recovery, leaving only diamonds in the sorting hoppers.
Debmarine Namibia expects Benguela Gem to operate for at least 30 years, adding around 500,000 carats of high-value diamonds to its annual production.
Rotor Sails for CO2 ships
Now for something trendy; Finnish wind propulsion specialist Norsepower has secured a contract for rotor sails to be fitted aboard two liquefied CO2 carriers commissioned by the Northern Lights JV in Norway.
The carriers will each be equipped with a single 28m tall by 4m diameter “rotor sail”, which Norsepower estimates will reduce fuel consumption and associated CO2 emissions by approximately 5%.
The vessels are being built by Dalian Shipbuilding Industry Company in China.
The “sails” will be delivered to the shipyard early next year, while both of the carriers are expected to be delivered in 2024.
Northern Lights is developing the transport and storage component of the Norwegian government’s Longship project, which includes the capture of CO2 from industrial sources in the Oslo region of Norway.
Once captured, the liquid CO2 will be shipped to an onshore receiving terminal on Norway’s west coast, then transported by pipeline to a subsea reservoir below the North Sea for permanent storage.
Norsepower’s rotors are a modernised version of the Flettner rotor patented in 1922 by Anton Flettner. Basically it comprises a spinning cylinder that uses the Magnus effect to harness wind power and generate thrust.
When wind meets the spinning rotor sail, the airflow accelerates on one side of the cylinder and decelerates on the opposite side. The change in the speed of airflow results in a pressure differential, creating a lift force that is perpendicular to the wind flow direction.
Depending on use, multiple rotors can be installed on a single vessel. Some are also designed to tilt, allowing vessels to navigate on height-restricted routes while using the technology.
The two first-of-their-kind 130m CO2 carriers have been designed by Northern Lights and will have a cargo capacity 7,500 cubic metres.
In addition to auxiliary sail power and LNG fuel, the sister vessels will also feature other energy efficiency technologies including air lubrication.
Once in operation, the vessels transport captured and liquefied CO2 and carry it to the Northern Lights receiving terminal in Norway’s Oygarden.
Since setting up in 2012, Norsepower has installed its rotor sail technology on at least six vessels – one tanker, two passengers vessels, a VLOC (very large ore carrier) and two roll-on/roll-off vessels.
The Northern Lights JV comprises partners Equinor, Shell and TotalEnergies.