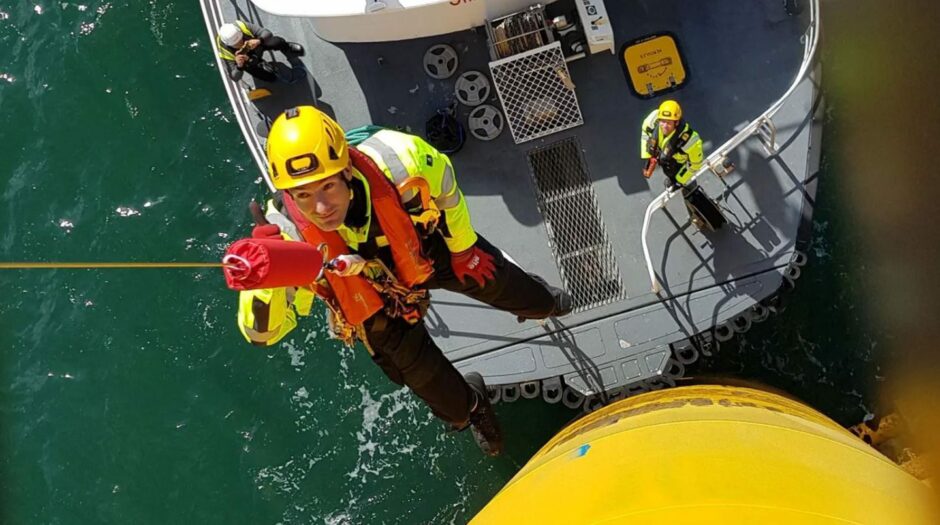
It’s all about timing.
While the offshore wind sector maintains a good safety record, there are always inherent risks of which workers are wary.
Not least of these is the moment technicians step from a bobbing vessel onto a small ladder at the base of the turbine. In all manner of weather, and dozens of miles offshore, it’s here that timing – and presumably a little nerve – are crucial.
As one of the riskiest points in a technicians’ offshore journey, this moment has been the sole focus of one Scottish technology firm. Pict Offshore’s Get Up Safe (GUS) system eschews the stepover entirely, in favour of a heave-compensated lifting solution which allows crew to move from crew transfer vessels to turbines safely and quickly.
Lasers track the motion of the vessel deck and automatically adjust the position of the line to ensure that transferring personnel are always kept safe – even if the crew transfer vessel (CTV) is moving in variable wave and weather conditions.
Its roots lie in Limpet Technology, an engineering firm based at the time Methil, and focused on providing systems for safe access and working at height.
Initially focused on the burgeoning onshore wind market, the team began to look at applications in offshore wind and whether its system could be adapted for use on even larger turbines at sea. While Limpet’s design ultimately failed to pass muster, prototypes still showed promise and ultimately attracted the attention of Danish wind developer Ørsted.
“They weren’t particularly interested in the Limpet products that we had developed, but they were interested in this new emerging transfer product for offshore wind,” recalls managing director Phil Taylor.
“We decided to spin out the R&D project into the new company, which is Pict Offshore and all of the know-how and assets that had been involved in taking the product up to that point were transferred.”
Pict was formally set up in April 2019 with Ørsted on board as a minority shareholder, bringing not only its offshore expertise but financial backing to commercialise the system.
A deal to outfit GUS at the group’s major Hornsea 2 development followed, and later its first export agreements which will see the system deployed at 1.8GW of capacity across a trio of the developer’s US pipeline, including South Fork, Revolution Wind and Sunrise Wind.
And last year fabricator Sif announced it would integrate the lifting system into its new Skybox monopiles.
To meet that demand the scale of Pict’s operation has grown too, from a workforce of just eight staff at the time of its incorporation, to a 40-strong team that now includes a growing services arm.
“As we’ve gone from manufacturing the systems into those systems being commissioned and serviced offshore, we decided to try and deliver most of that activity ourselves,” Mr Taylor explained.
This in-house technical service team now works at the Hornsea site maintaining GUS units, while the remainder of the staff work at the 14,000-square foot site in Inverkeithing, including 10 or so assembly technicians who build the GUS systems.
Get on up
As for the offshore workforce using the GUS system, Mr Taylor described a journey from “healthy scepticism towards acceptance” as its benefits became clearer.
“Although everybody knows there are risks associated with ladder transfer, you are to some extent master of your own destiny – you get to decide when you step back from the the ladder onto the boat,” he said.
“But as the system has been deployed and as it’s been used successfully over thousands of transfers, that scepticism has gone away, for the most part.
“From what I hear, the technicians now prefer using the GUS system which lifts them up to the platform without any effort on their part – compared to climbing slippery, slimy ladders and clipping in and out of all fall arrest systems.”
There are also reassuring levels of redundancy built into the GUS unit, from a backup sensor that measures the boats positioning, to an uninterrupted power supply that will kick in if power from the turbine ever fails. Failing that, power can be restored from the CTV via an umbilical cable.
The extent of that redundancy means developers like Ørsted are comfortable with using entirely ladder-less systems for crew transfer– a move that came as a surprise even to the system’s developers.
“When we started getting into it to begin with, we didn’t imagine that we would persuade operators to get rid of their boat landings and ladders,” he explained.
“That seemed like a huge stretch to us, and that was why we started off testing the system against ladders because we thought: maybe we can keep the ladders and we can increase the safety and accessibility.
“It was really Ørsted’s leap, they said: ‘If we remove the ladders and boat landing completely, there’s going to be additional capex upside.’
“It’s a nice additional business case benefit to have.”
Floating ambitions
Beyond the construction economics, he says the system can be of huge benefit to the operations and maintenance of wind farms too, not least in allowing technicians wider weather windows to access turbines in rougher seas.
“As wind farms go further and further offshore and into increasingly hostile sea environments, that becomes more and more important to operators,” he continued. “By opening up that weather window we can become very attractive on a commercial basis to the next generation of wind farms, particularly far offshore wind.”
Pict is confident that the system will be equally applicable to floating wind, fast becoming the next frontier of offshore development.
“We don’t see any reason why it can’t be,” he says.
“Obviously you’ve got two moving objects instead of just the one in our current application, but because of the way the deck tracking and active heave compensation function work, we don’t think that it that two moving objects present a challenge”
Pict is already in conversation with the backers of “quite a few” early-stage floating projects, and Mr Taylor’s hope is to qualify GUS on several demonstrator-scale projects to ensure it’s up to spec for the wave of larger projects expected to mobilise by the end of the decade, including gigawatts of capacity secured under the ScotWind round.
It’s a strategy that has the blessing of Ørsted too. Far from keeping the system proprietary, he suggests their hope would be for GUS to be adopted as the standard method of access for the industry.
“Despite Ørsted being the largest offshore wind developer in the world, they still don’t have a large enough pipeline for us to easily exist on that alone, so we really need to make this much broader than that,” he added.
Moreover, the firm needs reliable work to fuel throughput and growth in the short and medium term – much of which he hopes will come from exports.
“We can’t afford to wait for ScotWind to come around, so the intention is to be able to export the system to offshore wind markets wherever they may be in the world,” he continued.
In the meantime, Pict faces a challenge familiar to many SMEs in garnering investment to drive its growth ambitions – something Mr Taylor says is made trickier by a “very risk averse” landscape in Scotland.
“We don’t have the kind of Silicon Valley-style appetite for risk that is going to be needed to rally build the supply chain locally that can support the ambitions of ScotWind” he ventured.
“Either we will fail completely to build and supply things locally or the Scottish investor community needs to step up.”
Global expansion
With clear global ambitions, Pict is currently examining whether it should continue to assemble in its Scotland facility and export GUS systems or enter into agreements with local companies in other markets. At the same time, it’s also cognisant of the evolving nature of operator demands.
“The business case is evolving continually as foundation lines change,” said Mr Taylor. “All we can control is our product, and we are trying to make it as cost-effective as possible and look at ways in which we can improve the business case.
“The main way we see is by integrating the functions of a cargo lifting crane into the GUS system, so that instead of having two lifting systems on your platform as they have at Hornsea 2 and in the US, you can just have a single system that does everything.”
The next 12 months will see further development of this upgraded unit, with a view to having a product ready towards the end of 2024.
Provided a commercial product emerges from these efforts, it’s not hard to see the GUS system deployed across wind farms from the US east coast to Taiwan – nor, as in Sif’s case, adopted as standard by manufacturers who are already preparing the components of the future.
Much like the brave wind technicians, Pict too is hoping to benefit from excellent timing.
Recommended for you
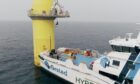