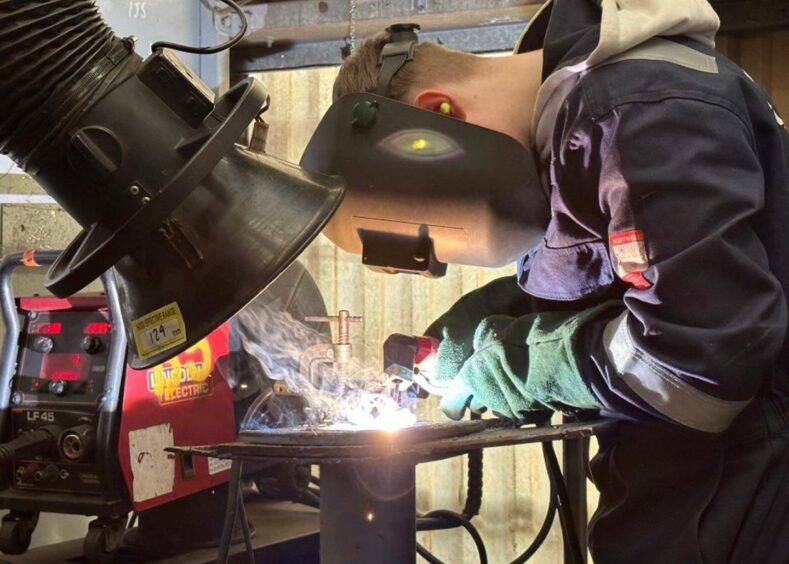
Welding is set to be one of the energy transition’s most prized skills, but the UK risks falling behind unless more projects and talent can be locked in over the next decade.
Offshore wind turbines. Platform jackets. Floating foundations. Hydrogen electrolysers. Carbon capture and storage facilities.
These will form the bedrock of the next 30-plus years of the UK’s energy transition – but someone has to build them.
Critical to that journey will be so-called ‘black trades’ like welding, pipe fitting, metal forming needed to manufacture and install equipment up and down the UK.
Demand for welding in particular is set to increase dramatically. The Engineering Construction Industry Training Board (ECITB) estimates the number of welders required by its sector could rise to 2,100 by the end of the decade – up 50% on the 1,400 employed in 2023.
ECITB statistics typically do not include supply chain and manufacturing firms, though ONS data suggests around 55,000 worked in the broader welding, metal forming and related trades in England and Wales in 2020.
That population is also growing older. Amongst the workforce mentioned above, estimates suggest around 40% are over the age of 50.
The organisation’s director of strategy and policy David Nash explained: “The 1,400 in our industry are very much qualified welders working in industrial settings, so will be doing the types of work that are going to be really vital. For example, retrofitting gas pipelines for hydrogen transmission or installing carbon capture on gas plants.
“Those are the welding trades that we’re going to need for the energy transition, and we’re going to need a lot more of them.”
When we talk about green skills we often overlook the trades, but without them, we’re not going to deliver net zero. It’s as simple as that.
Indeed, ECITB expects the percentage share of the workforce of welders will also grow, from 1.35% today to nearly 1.65% by the end of the decade, surpassing average growth estimates for the wider industry.
“Assuming projects that are in the pipeline go ahead to schedule – and this clearly a big if – but assuming that is the case, we could see a 50% increase in demand at least over the course of the rest of the decade,” added Mr Nash.
“It all reinforces the point that if we’re going to deliver major energy transition projects, trades like welding, pipe fitting, platers, mechanical fitters, industrial electricians – they’re all going to be vital to delivering this infrastructure.
“Whether it’s carbon capture, electrification, hydrogen production, offshore wind – they’re vital.
“When we talk about green skills we often overlook the trades, but without them, we’re not going to deliver net zero. It’s as simple as that.”
Bottlenecks
Demand for the trade is clear. But exactly how much – and when – remains a “big unknown”. Mr Nash says the shifting demographics raise questions over the volumes needed just to maintain current levels – let alone grow the workforce to meet demand.
Yet there appears not to be any issue with interest or awareness, he ventures.
“[Contractors] don’t lack for want of candidates applying for apprenticeships, particularly in occupations such as welding… There’s still a communication piece to be done around it, but in terms of remuneration, they’re very well paid jobs and you can progress very quickly.”
Indeed, it’s understood some skilled welders are earning upwards of £70,000 – and into six figures on the most complex of projects.
“What they find is there is a ceiling on the number of apprentices that they can take on at any given time, and that’s based on the requirements of their clients,” he added.
These limits are ultimately set by project developers through their budget and time constraints, which will dictate how many qualified and in-training staff can be on each project.
“Really in order to shift the dial we need contractors to be able to take a longer-term view having that certainty of the project pipeline and contracts coming down the track,” he says.
There are further complexities, but fundamentally Nash says both developers and contractors need certainty to greenlight projects, and to then commit more money to ensure more apprentices and trainees can be taken on.
Academy rewards
One solution is already in action at a revitalised Highland fabrication hub. Nigg Skills Academy is a not-for-profit training centre based at the port of the same name, with ties to DWP, Skills Development Scotland, and other industry and business leaders.
Set up more than a decade ago to address the skills shortages in oil and gas, it offers 16-week intensive courses in welding, fabrication and engineering with formal accreditation from the UHI North, West and Hebrides college.
“I’ve had many a chat with people in different industries and they think that green jobs are only green jobs if they’ve got green in the title,” says operations manager Ali Kennedy.
“Welding and fabricating could be one of the greenest jobs going because what you’re actually producing are structures to go out into the sea, be it offshore turbines or otherwise.”
January’s intake hosts 22 students spanning school leavers to mid-career workers and retirees looking to retrain. Partnering with UHI means students can also secure bursaries to help them during training. And while it’s not guaranteed, Mr Kennedy says it has had a high success rate placing Academy graduates in apprenticeships with local firms.
“We’re a good fit for this kind of person because they’re not committing to a year or two in college. They can do the first part of their training in 16 weeks and if they get taken on as an apprentice, that’s absolutely great.”
He is hopeful that demand for the course and these skillsets will continue to grow, particularly in light of the recent green freeport award.
“Demand is going to increase massively. They’re saying that the Green Freeport will create around 10,000 jobs and a high number of that is going to be the black trades, the hands-on trades as we call them,” he added.
That extends to the construction work on the factories, roads and infrastructure that will hopefully be unlocked by freeport plans.
“Really they’re indirect green jobs because they’re producing something that’s going to end up helping the renewable industry,” he added.
The hope is that in offering skills development – and a pathway into a long-lasting career – the previous decline in population and talent across the area might be arrested.
“We’re trying to set out that actually there is a future here… People in the area maybe don’t have to go down south to go to college or university – they can stay and get a good, highly paid job up here and progress their career while staying local.”
The country desperately needs tens, hundreds of thousands skilled workers. We’re 20,000 people short and it takes five to ten years to train them – that’s where the problem is.
No transition without it
One supply chain business attempting to navigate the demands of transition is fabricator Langfields. Part of the Macgregor group of companies, it builds process equipment for a range of industries spanning energy, waste, petrochemicals and nuclear and is already embedded in dozens of energy projects, producing equipment essential to new nuclear plants, CCUS facilities, sustainable aviation processes.
“Without us and companies like us, you don’t get an energy transition,” business development manager Ben Cohen told the Decarb Scotland event in February.
“The opportunities are vast, we’re seeing some unbelievable enquiries for reactors for blue hydrogen, electrolyser fit out for green hydrogen, storage vessels, nuclear vessel fabrication for SMRs,” he said.
The challenge Langfields faces is not just fierce competition from other sectors to hold onto its existing talent, but that it struggles to justify increasing its workforce without a firmer pipeline of work – something Mr Cohen said was a problem across the energy sector.
“You can train as many people as you want…but there’s got to be jobs at the end of it. We’re not hiring. We’re one of the biggest fabrication businesses in the country, and we don’t have jobs currently because our level of work is such that we have a workforce that currently can deliver that.”
He suggested it takes five to ten years to train a welder to achieve sufficient expertise for high-integrity schemes like nuclear, and a lack of new entrants means the UK is likely to remain far short of demand.
“The country desperately needs tens, hundreds of thousands skilled workers. We’re 20,000 people short and it takes five to ten years to train them – that’s where the problem is.”
And while new funding packages may help firms invest in equipment, facilities – and potentially training – unless projects are given the green light imminently, the supply chain can’t justify new job creation.
“These important projects desperately need companies like us and Glacier [Energy] and others to scale and grow our capacity but that needs to happen now to meet the upcoming demand.”
Mr Nash issued a similar warning.
“The key message is we need certainty from government at a project level so that developers can have the confidence to put in place programmes early so we can build that talent pipeline ahead of when they’re needed – because at the moment, essentially all the risk is placed on the contractors,” he said.
The good news is the UK workforce is more than capable of taking on the challenges. Both Mr Nash and Mr Cohen suggested the transferability of current skillsets and equipment is straightforward.
“We’re in a really good place in terms of the overall skill set of the welding workforce,” added Mr Nash. “We just need to find ways in which we can supplement the number of workers available.”
Meanwhile, those looking for a sustainable, well-paid and transition-aligned career should take note of the trade and its potential benefits.
“Welders are going have more of a choice in terms of what projects they want to work on. And so in a way that message itself is a good recruiting sergeant to the next generation,” he continued.
“But fundamentally there is a big risk here. Unless we get more in, these projects just won’t get delivered.”
Recommended for you
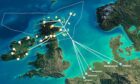