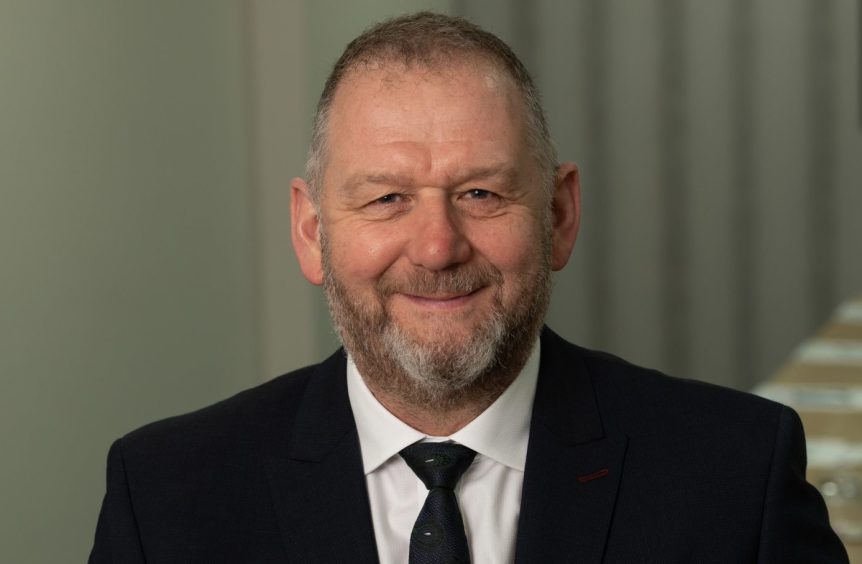
“I’ve been working on the tools for decades, why should I have my competence checked.”
It’s a good question. A time-served craftsman may not have worked in industry for some time or undertaken work scopes that cover all activities of their trade, so the need to verify ongoing technical competence is clear.
But what about a worker who has ‘kept his hand in’?
There are a number of studies that look into how repetition of a task can lead to a state of decreased external awareness and reduced sensitivity to hazards. This could result in corners being cut or not strictly following safety procedures (such as using a two-handed tool with one hand).
There are other reasons why people could become complacent. They could be pushed for time, anxious to meet performance goals or over-confident in their work.
When an individual, workforce or facility owner becomes excessively certain of their ability to safely operate a complex oil and gas facility, they can become pathologically complacent.
We don’t readily see warning signs if we aren’t expecting them, and psychologically it is very easy for us to explain away the warning signs and interpret them based on past experience – even when the situation is very different.
One of the biggest drivers behind the Connected Competence scheme is to help avoid workplace incidents and accidents.
Put simply, assuring a base level of ongoing technical competence for all workers creates a safer working environment for everyone.
It helps build confidence that everyone is supporting a duty of care to their coworkers around them.
Disasters that could have been avoided
Incidents such as Piper Alpha, Bacton Gas Terminal and Deepwater Horizon were avoidable. A lack of diligence around the recognition and assurance of competence standards was found to be a key factor that contributed to these disasters.
The Health & Safety Executive (HSE) defines competence as ‘the ability to perform activities to a recognised standard on a regular basis. It is a combination of skills, experience and knowledge’.
Connected Competence delivers this at an industry-wide level and not just an individual and organisational level.
Technical tests or site-based assessments allow workers to verify and confirm their skills to achieve the required standard.
Step Change in Safety chief executive Craig Wiggins said: “In our industry, we manage major accident risks every day, and each of us plays a role in ensuring that the barriers preventing these risks from escalating into serious incidents remain intact.
“It is vital that we have competent people in our operations who can install, operate and maintain the equipment that ensures safe operations.
“I see Connected Competence as a key tool in building a workforce that understands these risks and knows how they impact safety on our facilities. I encourage all personnel – both core crew and temporary staff – to take the opportunity to demonstrate their competency through Connected Competence.”
Reducing duplication of assessment
Connected Competence allows employers to share the same ongoing verification of workers’ technical competence. This means workers are verified against the same recognised and accepted standard for the applicable trade disciplines.
Historically, the workforce was verified against company-specific technical assurance schemes. Despite being similar, each time workers moved to another employer (through their own choice or via TUPE) they had to repeat the process.
Connected Competence is a proactive way of assuring base technical competence on a regular basis so that everyone is working to the same recognised base standard needed for today’s working environments – whether you are a full-time employed or temporary worker. Demonstrating base technical competence should not be determined by a worker’s employment status.
When competencies are not assured on a regular basis, one of two things may happen – people can become complacent and/or they may not maintain the level of competence required to operate safely.
The dictionary definition of complacency is: ‘A feeling of calm satisfaction with your own abilities or situation that prevents you from trying harder.’
But there is no room for complacency in major hazard industries such as oil and gas. We must continue to remain constantly vigilant while putting safety at the heart of everything we do.
Temporary workers who are working (or seeking work) with Connected Competence employers can access technical test vouchers to cover the cost of the tests.
Unite the Union regional officer John Boland said: “Unite the Union supports this initiative for the temporary (ad hoc) offshore workforce.
“It will ensure these workers are able to demonstrate their ongoing competence to work safely offshore, through Connected Competence, at no cost to themselves. It should make it easier for the workforce to move between connected competence employers, without the need to repeat this competence verification every time.”
The trade disciplines required to verify competence through technical tests before mobilisation include pipefitters, platers, electrical maintenance technicians, electrical installation technician, mechanical maintenance technicians, instrument & control technicians, industrial coatings technicians, riggers, appointed persons for rigging and thermal insulators.
Click here to find out more about the technical tests.