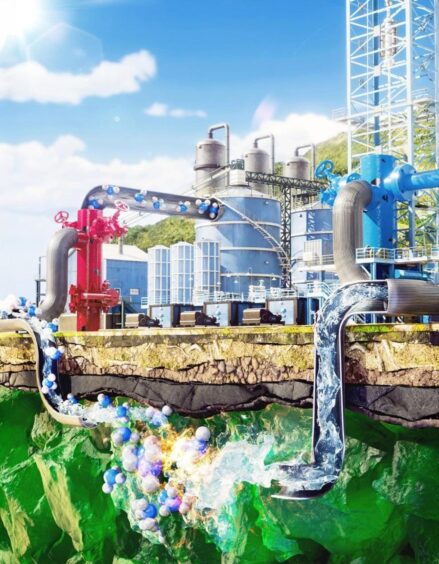
Delving into the world of energy science and technology has long been a fascination of mine. It is an interest that personally reaches right back to 1958 in New Zealand.
The family lived in Palmerston North at that time; Dad was reading for his PhD at Massey while I and the older of my two sisters were leading an idyllic, semi-feral existence where it was all our poor mother could do to get us to stick on our sandals before heading out to school.
1958 was our second-last year living in NZ and, that summer, we went on an extended holiday up to the Lake Taupo area and Rotorua: so big geothermal springs, boiling mud – that sort of stuff.
One day, we headed north up the main drag out of Taupo bound for sulphurous Rotorua.
As I recall, not far along that road we stopped to sightsee what, I was told, was a geothermal power station.
My memory of what we saw remains crystal to this day, though it was many years before I decided to learn more about what I had seen.
It turned out to be the Wairākei geothermal power station, which had only just started operating.
It marked the first time geothermal hot water had been used for power production on a commercial scale anywhere in the world.
Throughout my years as an energy journalist, geothermal energy has quietly simmered in the background – barely more than that.
The notion of harvesting heat from the Earth’s crust was a fascination, and I am very well aware of just how high the temperatures encountered in deep oil and gas reservoirs can be.
But it has taken from 1958 until now to get really fired up, and it is to do with a novel way to produce ammonia (NH3).
Ammonia is largely made using the Haber process, also called the Haber-Bosch process, invented by German Fritz Haber in 1918.
It converts atmospheric nitrogen (N2) to NH3 by a reaction with hydrogen (H2) using finely divided iron metal as a catalyst.
The process is carried out at 400-500°C and a pressure of 10-30 MPa (megapascals) over an iron catalyst.
It is energy intensive and yields low ammonia per pass, with a low conversion efficiency of 25%, which acts as a limitation.
But now researchers are looking underground at Earth’s natural heat and forces to cook up ammonia for fertiliser.
‘Aha’ moment
MIT scientists have generated ammonia by mixing nitrogen-laced water with iron-rich rocks – without any energy input or CO2 emission.
It is speculated that this novel approach may lead to a more sustainable alternative to current methods, theoretically churning out enough ammonia for 2.42 million years.
The idea stems from an unusual geological phenomenon observed in the 1980s in Mali, West Africa.
Locals discovered a well streaming with hydrogen gas, which scientists later traced to a water-rock chemical reaction beneath the Earth’s surface.
“It was an ‘aha’ moment,” according to Iwnetim Abate of the Massachusetts Institute of Technology.
“We may be able to use Earth as a factory, harnessing its heat and pressure to produce valuable chemicals like ammonia in a cleaner manner.”
Which is precisely what Wairākei is: an Earth factory.
Ammonia is a key ingredient in fertilisers and can also be used as an engine fuel, particularly marine engines.
But today’s industrial ammonia production is, as already explained, highly intensive.
It consumes about 2% of global energy and releases around 2.2 tonnes of CO2 for every tonne of ammonia produced, making it the chemical industry’s top CO2 emitter.
To test their “Earth factory” idea, Abate and his team built a rock-water reaction system that mimics Earth’s subsurface environment.
They exposed synthetic iron-rich minerals to nitrogen-laced water, triggering a chemical reaction that oxidised the rock and yielded ammonia, which the team dubbed “geological ammonia”.
The magic is that the process required no energy input, emitted no CO2, and even worked under ambient conditions.
The team then swapped the synthetic mineral with olivine, a natural iron-laden rock, to better mimic real-world scenarios.
They further optimised the process by adding a copper catalyst and cranking the heat up to 300°C (572°F).
Within 21 hours, they produced about 1.8 kilos of ammonia per tonne of olivine, demonstrating the method’s feasibility and sustainability.
According to Abate, such rocks are all over the world, so the method could be adapted very widely.
Of course, there has to be a catch – well, at least two: cost and pollution.
The guys at MIT have a whole other level of complexity to work through.
For starters, implementation will involve drilling into iron-rich rocks deep within the earth, injecting nitrogen-laced water and grappling with the intricacies of how rocks crack, expand and interact with gases and liquids.
Nitrogen sources are considered pollution in wastewater and removing them costs money and energy.
However, the team think they may be able to use the wastewater to produce ammonia. It’s a win-win strategy.
It should not be forgotten that NH3 is pretty important for life. Apart from via microbes, the only other natural way to produce ammonia on Earth is through lightning striking nitrogen gas.
And that is where geological production of ammonia becomes really fascinating; just think about where life came from.
Recommended for you
