
“Who believes that all incidents are preventable?” was the question Step Change in Safety boss Craig Wiggins asked the audience at an event on health and safety in Aberdeen.
The response from the delegates of the Offshore Energies UK (OEUK) HSE conference revealed “about 20%” of people think that all incidents are preventable.
Before taking the poll, the trade body chief executive highlighted a “plateau” in UK safety rates in recent years and that there has been worsening trend particularly oil and gas spills, often called “hydrocarbon release”.
Pointing to recent data from the Health and Safety Executive (HSE), he said: “There are signs that we’ve done some great work over the last 30 years, but the fundamental issue is we have plateaued and in ‘23 and ‘24, we’ve actually seen an increase, certainly from a hydrocarbon release perspective.”
The Step Change in Safety boss admitted that there were no “majors”, however, there was a 5% to 10% increase in hydrocarbon releases.
“And the fact is, we had less assets offshore because there’s been quite a lot of decommissioning,” he added.
In addition to the “weak signal” from process safety in the industry, personal safety rates also took a hit in the same time period.
He continued: “From a personal safety with regard to incidents associated with injuries, we have seen an uptick after the pandemic and we’re now back to where we were in 2018.”
Wiggins also pointed to “anecdotal evidence” that there were further issues in 2024.
‘I fundamentally believe that every incident is preventable’
He opposed the remaining 80% of attendees who believe some accidents are not preventable and warned that those who do may be harming the safety culture within their organisations.
“I fundamentally believe that every incident is preventable, and I’ve thought that for many years and the reason I have that belief is that I’ve investigated so many incidents in my career,” he said.
Over his 40-year career, he said he has never found an incident in which nothing could have been done from a “people process and plant” perspective to prevent what came to pass.
“I’m not saying that incidents don’t happen but it’s absolutely clear that we can always find something that you could have done differently,” Wiggin explained.
‘Causal reasoning’ and not pinning blame on individuals
This fed into a talk from Shell UK’s (LON: SHEL) senior production operations engineer Chris Cunningham who highlighted his firm’s use of “causal reasoning”.
“Many companies use incident data to inform safety improvements, that’s nothing new, but traditional efforts tend to focus on the outcome of the incident and the consequences, for example, the incident type or the location of injury” he told attendees.
“In Shell, we use an instant investigation methodology called causal learning to determine cause.”
Cunningham said that other approaches to safety reporting are “based on hindsight bias” and can often pin the blame on one person rather than the situation they found themself in.
“The theory is that by understanding the systematic and organisational level causes, we can direct blame away from an individual, or a group of individuals, and create a learning environment where everybody is involved in improving our safety performance,” he added.
‘Permit to work and risk assessment’ cause 33% of Shell incidents
The London-listed supermajor has been using this approach for five years and now Cunningham and his colleague have collated the data gathered to find the most common reasons for accidents across Shell’s UK business.
“A total of 51 causes were analysed from 17 high potential instance over the last five years,” Cunningham explained.
More than a quarter (26%) of incidents that resulted from risk management issues were down to “managing/ supporting people in critical steps in a task” with the next highest cause being “assessment of risk for infrequent/high-risk tasks” at 16%.
“In 26% of the causes that we analysed, a critical decision or action was required which relied on a person to carry out the steps in a certain way to prevent the incident,” Cunningham explained.
“The question for us is ‘how do we identify critical steps on a task when the step has been carried out by a human, but when an error could cause an unwanted outcome?’ and how do we safeguard against that outcome because as we know, humans make errors.”
Across “permit to work and risk assessment” cases, one-third of the incidents covered in the analysis were found, he added.
“Permit to work and risk assessment are obviously closely linked as task risk assessment is a key aspect of permit to work.”
From this analysis, Shell was surprised at some of the findings while others “reaffirmed what we already knew,” Cunningham said.
In response to this, Wiggins commented: “That mindset [every incident is preventable] was actually created by doing an awful lot of causal learning at Shell in my 26-year career there and leading those programmes.
“When you go through that programme you start to have different insights into what we can do from a system perspective, a process perspective and obviously, a people perspective.”
When asked why he said, “every incident” instead of “most incidents”, Wiggins responded: “We’re talking about people, leaders are leading people, so I believe that we can keep people safe and I understand that people make mistakes but it’s our industry’s absolute accountability to make sure that people can make mistakes and not hurt themselves or cause a major accident hazard.”
Recommended for you
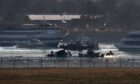