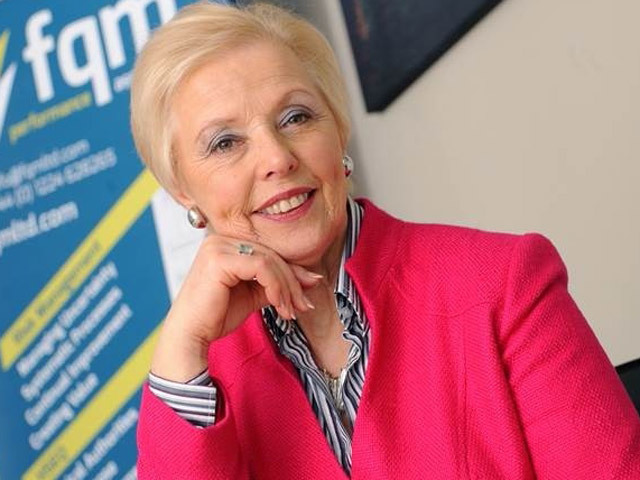
Rising costs of production and a sharp decline in drilling and exploration – these are the harsh realities of today’s oil and gas industry in the North Sea.
In the face of economic pressure, cuts are bound to come, and all too often these cuts are easiest made in budgets such as development and training.
In my experience this is a recurrent cycle that has been replaying for the past four decades.
The resulting skills shortage is recognised across much of the energy industry, however, do we stop to think that we are overlooking the importance of training within the competence formula?
Training is how we impart knowledge, and to some extent understanding, to our staff; competence is the measure of how this is then skilfully applied in the workplace. By making cuts in training when costs rise we are almost treating it as a “nice to have” option rather than an essential component needed to meet legal and contractual requirements.
The starting point is medium and long-term education and much is being done by organisations such as Opito and SCDI, alongside many individual companies, to convince young people that there is a lifetime of opportunity in the industry.
These initiatives, especially when introduced at primary school level, can do much to stimulate an early interest in science and engineering.
Science or engineering clubs in schools, partnerships between schools and local companies and, in some cases, the establishment of in-house training academies which take school-leavers, can all have a positive impact.
This, however, needs to be coupled with local government and politicians, in particular, promoting a more targeted conversation on the part that carbon-based energy sources can play in the overall energy mix of the country for the foreseeable future.
Next is the conversion potential among the 8,000 or so members of the armed forces due to leave the services in the next few years. There is a real opportunity to capitalise on these highly skilled workers who could, with the right training, convert to the energy sector.
They present a great potential to fill the gap left by an experienced but ageing oil and gas workforce, many of whom are close to retirement and who will take their knowledge and expertise with them. However, realisation of these opportunities will take considerable investment.
But what can be done immediately to recruit, retain and develop the already extant workforce?
Once again training plays a crucial role. In times of high profits and returns, training is often looked upon as an investment by companies wanting to motivate and develop their staff and provide them with a clear career path.
However, in times of rising production costs and lower profit margins, companies feel obliged to look for quick and effective ways to cut costs, invariably leading to staff development cutbacks, with courses limited to mandatory or refresher training in line with HSE requirements.
The result is a lack of consistency of staff development and progression, which feeds in to the skills shortage equation already touched upon. Workers begin to feel undervalued and unsupported, which in turn impacts upon retention.
As skilled staff become ever more elusive, no longer viewing long-term employment with one employer as the desired norm, there is an increase in “job hopping”.
Qualified and experienced employees are enticed away from one company to another through ever higher salary packages creating disproportionate expectations within the job market. As the turnover rate increases, companies try to offset recruitment costs, and view investment in training with caution.
As if the above difficulties were not enough, the continued use of ageing North Sea assets, originally intended to last 25 years, but still fully operational, has brought additional challenges to the industry in terms of risk and hazards. As an industry we can rise to the challenge.
Changes in production technology and asset degradation increases the range of technical competencies required by those working both onshore and offshore. The competent authorities and accreditation bodies are clearly indicating the need to be proficient in the management of Human Factors which play a vital role in ensuring an efficient, safe environment in which to operate.
Nowhere has the above scenario been more clearly observed than at FQM, where the work of the consultancy team in recent years has led to the establishment of an independent training arm.
The fact that training is delivered by specialists with hands-on, day-to-day experience of their particular subject, means they are fully aware of the latest changes, developments and legal requirements within their specialisation.
This is a much richer proposition than that offered by full-time trainers no longer working in the industry. The pressure is still on, but training definitely can remove some of the burden.
Anne Iravani is the newly-appointed training manager at FQM, a health, safety, environment and quality consultancy and training organisation
Recommended for you
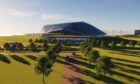