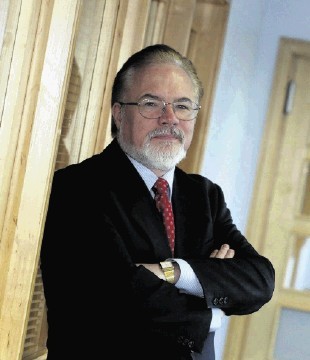
As the ITF Showcase kicks off in Aberdeen this week Dr Patrick O’Brien, chief executive of ITF, has taken up the role of Energy Voice’s guest editor. Follow along each day as he spells out the challenges and triumphs the industry faces.
The oil and gas sector is both willing and increasingly able to exploit innovation, recognising that it can help to deliver cost efficiencies, support production and most importantly, improve safety.
The increasing use of robotics and autonomous systems by oil and gas companies is part of this innovation picture and a key theme of the Technology Showcase.
One of the biggest headline uses of robotics is the widespread deployment of ROVs. This has had a huge impact on subsea activities, in terms of safety but also in reducing diver activities and enabling new exploration and production opportunities.
Whilst ROVs have become a familiar sight offshore and are no longer perceived as science fiction, some of the new tasks that these machines are undertaking are truly remarkable.
Their capabilities are increasingly challenged for example in the deep water ‘pre-salt’ regions of Brazil’s oil fields, depths of 3-4000m are common and the operational challenges to man and machine are significant.
Importantly for the industry, these systems and tools are increasingly reliable with ROV operations reporting decreasing breakdown time.
Tasks for ROVs encompass activities far greater than acting as a ‘pair of hands’. They are now capable of supporting drilling operations and complex well intervention activities. The ROV market is set to grow and grow.
Innovators are now taking the ROV into new areas and equipping them with more capable tools and developing new technologies which will eventually remove the cumbersome tethers and umbilicals that impose a restrictive element to their current operations.
There is the potential for increasing automation to occur in many areas of oil and gas operations. Further developments will be able to target the drill floor, allowing for safer and more efficient drilling operations.
Condition based maintenance and sensor arrays are providing operators with very specific and real time data.
This is increasingly important for the subsea environment where the need for asset related data is critical for safe and efficient operations.
Developers are responding to this with smart sensors which can be used for everything from fault detection and analysis to the monitoring of re-injected produced waters.
Machines and automation are now capable of undertaking many highly skilled tasks. This will pose further challenges for the industry, but as always there will be opportunities as well.
Autonomous underwater vehicle (AUVs) can now be preprogramed with specific roles for example, surveying subsea pipelines, water measurement, leak detection and significantly for mapping the seabed prior and during construction activities.
Future systems will see subsea ‘parking’ and charging bays for underwater vehicles.
The use of autonomous vehicles within the industry is now taking the natural route of deploying remotely operated aerial vehicles (ROAV) to support activities in difficult, hard to reach and dangerous areas.
Operators in the North Sea have successfully used these aircraft for numerous offshore inspection activities and have not only undertaken tasks more quickly and cost effectively and at significantly less risk, but the scope of work has also increased.
One example is a long term 3D mapping and analysis task underway in Alaska by unmanned aerial vehicles providing a low cost solution.
The future will now look towards the next suite of aerial vehicles.
These will be capable of operating beyond visual line of sight and by exploiting smart materials and enhanced sensors, they will be able to stay airborne for hours not minutes and operate in much harsher climatic conditions.
The opportunity now exists for developers, users and the relevant authorities to collaborate on taking these technologies to the next level.
Then their real potential will begin to be realised.
Recommended for you
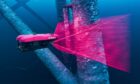