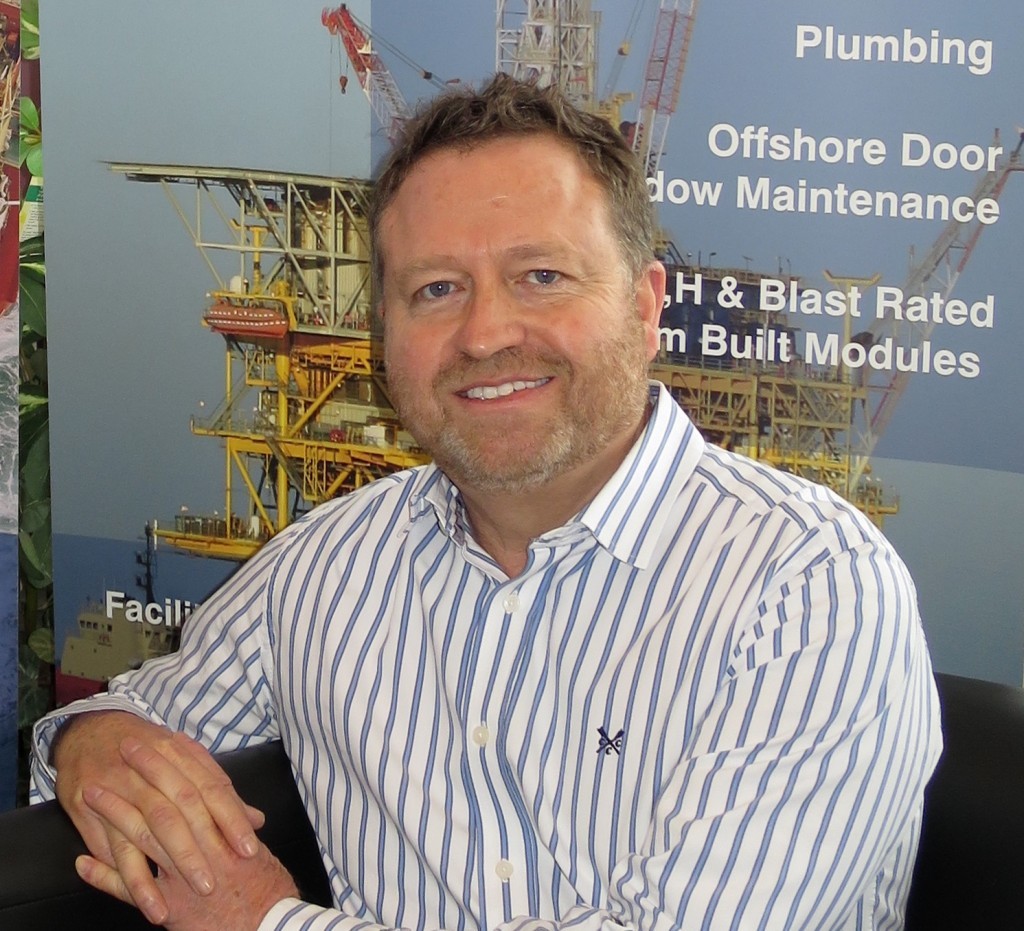
We may find ourselves in one of the most challenging eras our industry has encountered but, whilst there are challenges and consequences ahead for many, there is also the opportunity to look at what can be done to control the costs of oil and gas projects at planning and execution stage.
Reports from the sector’s leading monitoring bodies show us that the fundamental issue is that worldwide production of crude oil could drop by nearly 40 million B/D by 2020, whilst at the same time there will be a need for an additional 25 million B/D to keep pace with consumption. Understandably, the race is on to develop new technology to maximise recovery from fields old and new. Every bit as much of a challenge is that operators, contractors and service companies need to find ways to achieve this, while minimising project and operational costs, reducing environmental imprint and maintaining safety.
Some 15 years ago, the proportion of major oil and gas projects finishing 50% over budget was only 10% but by last year that number had almost tripled to 28%. According to a recent Schlumberger Business Consulting report, this trend is expected to worsen with the report predicting that: “the industry’s capacity to deliver these projects is not keeping pace, and as a result, significant overruns in budgets and schedules are rising in frequency.” Statistics like this should lead to companies thinking about how they can arrest, or reverse the trend.
One of the most effective ways to mitigate these risks is to increase the effectiveness of project controls, enabling the capture and immediate reporting of accurate data regarding cost, resourcing and schedule; allowing quicker and more efficient decision making to head off delays and overspends. Some companies have wrestled with the process of cost and schedule control for decades, relying on data which has been compiled by hand (often retrospectively), entered manually and inefficiently; much of the reporting from this data is inevitably inaccurate and too historical to support a proactive management process.
So how can companies improve the type of controls and data intelligence that they already possess?
It’s easy to see that technology investments for the industry typically focus on extending subsea capabilities and advancements in exploration, drilling and production, but investment in technology to improve business efficiency and economy of projects is neglected. Adopting the latest cost and schedule management software is a relatively small but beneficial investment compared to the money and time lost when a large project runs over schedule and over budget. It would appear to be one of the best kept secrets in the oil and gas industry that there are accomplished software solutions out there which integrate cost control with schedule management and can provide the key to long-term cost reduction, better project controls and hence greater ROI.
But these fantastic technological solutions will only be effective if combined with best practice in terms of contract, cost and schedule management. For the moment, however, let’s consider what the modern systems themselves can do to improve the unfavourable trend facing the industry.
With the typical project control methods adopted by even the largest companies involved in oil and gas projects, it’s just not possible to produce reports fast enough to provide timely insight into project performance. Systems and processes are not in place to provide early warning of the impact on cost that a change in scope or schedule will create and in these situations variations, disruption and delays become the silent monster which can financially cripple a project.
On a large project, it can be overwhelming to keep track of the interaction between many contracting parties (interfacing schedules, integrating resource allocation and performance) and typically data remains in separate silos with a lack of transparency between the various stakeholders.
Here, the solution begins with how we collect data. Traditionally, project cost and schedule management has relied on manual processes and outdated tools, which limit the speed and accuracy of data capture and reporting. The goal should be a single, accurate source of data maximising automated capture preferably at the workface and a single, combined pool of integrated data, capable of being accessed in real-time with informative dashboards cost reports on demand.
There are systems and solutions available, which allow progress, productivity and costs incurred to be reviewed on that same day in various global locations. Similarly, web-based dashboards showing as-built progress, burnt man-hours versus budget, etc. are all possible – but the technological solutions enabling this are only just beginning to be adopted by the leading players in the world’s oil and gas industry.
Companies which wouldn’t hesitate to invest millions in new subsea technology continue to overlook a smaller investment which can tighten control and make the difference between seeing a successful ROI, or a financial disaster.
An owner/operator engaging an EPC contractor for a large project often doesn’t have sufficient transparency into how the project is really progressing and discovery of cost or time issues is commonly realised too late to be influenced. He may feel the risk rests with the contractor, but does it really? What happens when the project is beginning to fall behind? The owner often has no way of knowing the true extent of the problem. The contractor may be close to delivering that new asset but if it isn’t producing by the deadline, then for the owner, the revenue isn’t flowing either. Recoverable penalties and liquidated damages from the contractor are unlikely to be an adequate compensation for lost project revenue. In this case, where does the risk actually sit and how do you assess and mitigate that risk before it’s too late?
The types of systems discussed here can offer multiple parties access to real-time project data, therefore giving owners the opportunity to track the project as it progresses, helping to uncover issues before they become insurmountable difficulties. Conversely, contractors can see problems as they begin to emerge and have opportunity to correct them before delays and overruns cut into margins.
When it comes to devising the optimum project controls system for the current project, the best indicator of the future is to examine the past. Studying the patterns of past project performance can establish benchmarks, trends which can be used to forecast expected outcome – and plot a better course.
Today’s technology can enable us to establish accurate benchmarking by using historical data to provide more realistic forecasts. Being able to track your project and predict potential outcomes ahead of time can mean the difference between finishing a project successfully and seeing a disaster unfold. By having the historical data as a guide and current data at your fingertips in real-time, you have the tools to make sure bad history isn’t repeated and to make better, more informed decisions as the project progresses.
Whilst it is generally viewed that the oil and gas industry will meet the challenges and flourish in spite of them, it must be considered that projects are becoming more complex and more costly to achieve. It will be important to the industry participants in this era, to embrace new technologies, and drive their projects towards success, paying attention to more effective cost and schedule controls. It is clear that the oil and gas industry can benefit from the technology available today coupled with established best practices so that these mega projects can be delivered efficiently, within time and closer to budget than in the past.
Richard is Managing Director of Aiken Burke, a Chartered Quantity Surveyor, with more than 30 years’ experience working on projects within Oil & Gas, Power and Process installations, Building and Infrastructure
Recommended for you
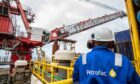