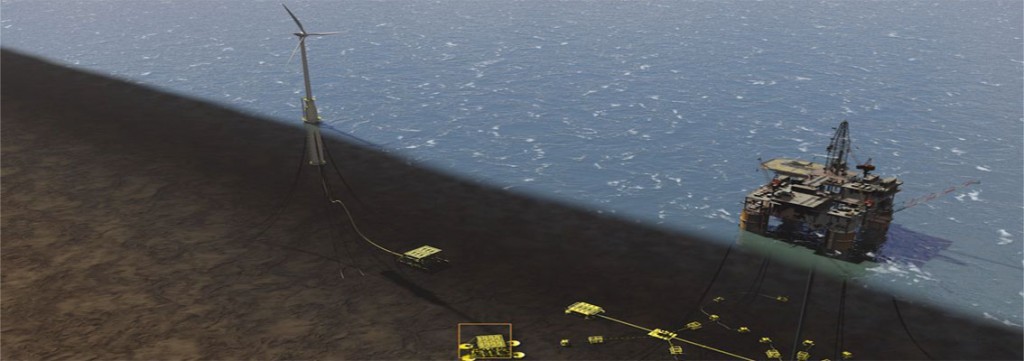
Floating wind turbine technology is well placed to help oil and gas operators reduce the cost of recovery from reservoirs using water injection, according to an industry expert.
A new joint industry project – Win Win – being led by DNV GL, has brought together oil majors including ExxonMobil, ENI, Statoil, Nexen and VNG to share knowledge and pursue water injection in subsea reservoirs delivered by wind-power rather than traditional gas turbines.
The technology is seen as being cost-efficient, able to reduce an oil platform’s carbon footprint and offers opportunities for one turbine to be used on multiple wells.
Integrating offshore wind power with offshore oil and gas operations could allow operators to significantly reduce costs for certain activities while also offering a new niche market for offshore wind technology, creating a momentum for both industries.
DNV GL’s Johan Sandberg, service line leader of offshore renewables, said that, under the right circumstances and conditions, costs could be cut significantly by powering the subsea pump via an offshore wind turbines that are placed in close vicinity (in the order of hundreds of meters) of the subsea manifold.
“Having major operators on board is incredibly valuable. It enables us to work with real cases and we can work with their staff to verify the work we have already done and apply that to real-life scenarios.
“I cannot speak for the oil companies themselves, but there are clear commercial benefits if we can get the system deployed.”
“In the conventional solution for a subsea injection manifold, the costs associated with connecting a subsea power cable to the host platform, where the electrical power for the subsea injection pump is generated, can be substantial.
“Under the right circumstances and conditions, it may be possible to reduce costs significantly using offshore wind turbines.”
The reduced costs are found thanks to the shorter subsea power cable required, the elimination of additional power generation on the host platform and, in the case of Norway, reduced taxes related to the incremental emissions of natural-gas turbine power generation for the subsea injection pump.
A successful demonstration of a stand-alone system could provide operators with a new and cost efficient mean to develop marginal reservoirs and enhance production in mature fields with long step-out distances.
Sandberg said: “We are very much looking at the next step. That could involve a working prototype. We are very keen to have industry keeping the momentum up.”
Producers have for many decades injected water into oil reservoirs to increase oil recovery. It is a technically complex, energy intensive and space consuming process.
A stand-alone, floating wind turbine requires no downtime on the host platform during installation. There is no costly platform conversion and corresponding downtime in order to install additional power generating system. There is also reduced fuel costs and emissions from running the gas turbines.
One concern is the intermittent nature of wind, however this is not a major dealbreaker as far as water injection is concerned.
Sandberg said: “Water injection is one of the processes that does not rely on continuous power source. Once the reservoir is up to the correct pressure it can remain there during down periods of power generation.”
Floating turbine technology is well established. Statoil’s Hywind was deployed in 2009. The Norwegian energy giant is expected to make an investment decision on the Hywind array project of the coast of Aberdeen in coming weeks.
Recommended for you
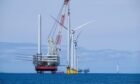