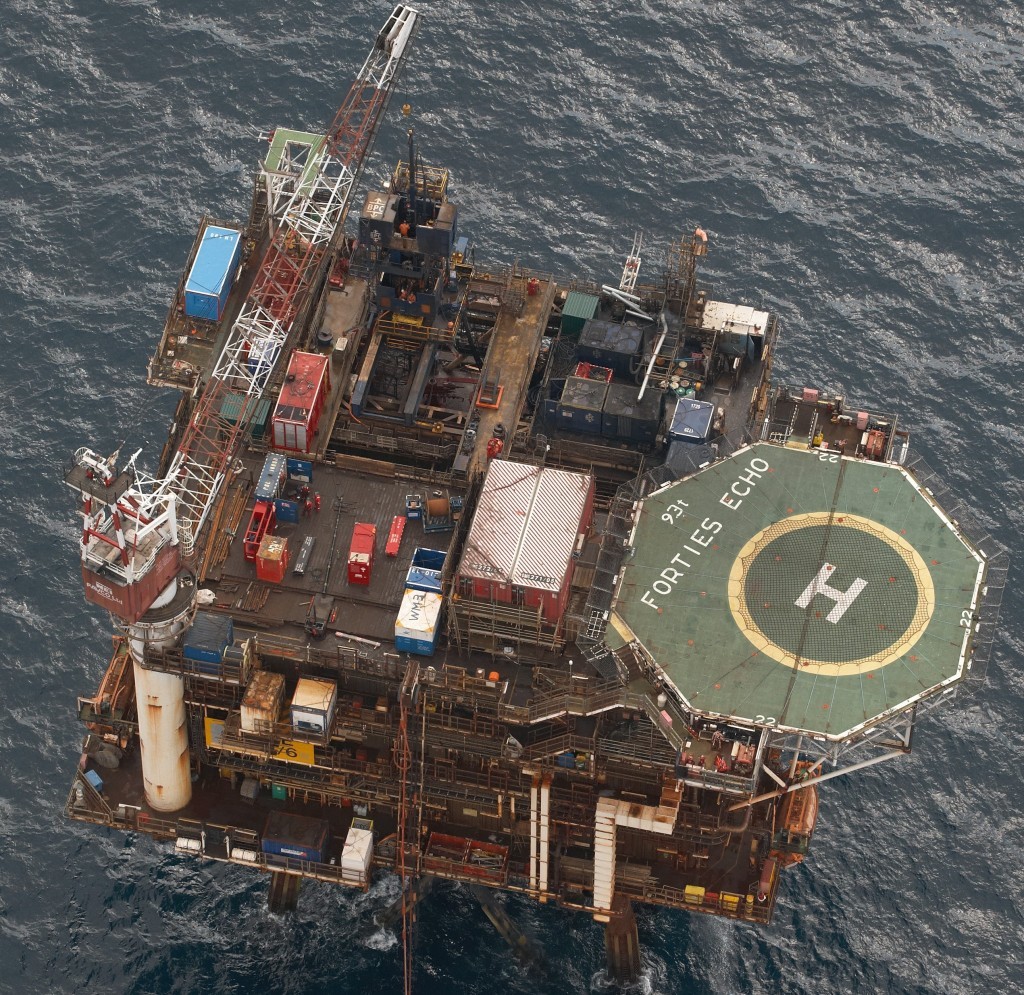
As an industry we are realising that the oil price may continue to drop to a level previously thought unthinkable, $20 to $40 per barrel. Regardless of whether or not these prices are seen in 2016, we do have to accept that a sustained low price is here to stay for a lot longer than we thought last summer. This is our ‘new normal’, where oil price determines the cash flow of the industry. Low oil price plus high cost equals a lot less cash, and a lot more pressure from the shareholders.
The current cash crunch is being felt by the global industry, but nowhere more acutely than on the UK Continental Shelf (UKCS). The previous long period of escalating oil price has made the drop particularly painful in a region with ageing assets, high costs of production, high taxation, and relatively high capital expenditure for new fields. We must not forget that the UKCS is competing for cash against all the other oil and gas basins in the world, and today many of them are more attractive.
As an industry we have taken the quick, dare I say, easy actions – cutting costs by postponing projects, cutting jobs and cutting rates. No doubt, future M&A activity will also enable more synergies to be extracted by larger merged operations. However, to be sustainable in the ‘new normal’ we must go further: reduce complexity, boost innovation, enhance collaboration, and extend standardisation.
Cost savings through reducing complexity
An example of complexity from the subsea sector shows how documentation has increased over the last ten years driving up cost. Digitalisation has made it easier for people to request more and more information, a lot of which they don’t really need. Historically, a contractor in the business – in a typical project – would deliver between 5,000 and 10,000 documents, but each one has an average of three revisions so we end up with at least 30,000 transactions between two parties with the need to produce more as the project develops.
Handling time has also increased, where it used to take on average 30 minutes handling time per revision now it takes an hour. A big project may require a contractor to have 25 people just on document control, but this exponential rise in documentation hasn’t provided tangible improved performance either on safety, environmental impact or on cost, so it does to a large extent only contribute to escalating costs, and prolonged schedule without providing much tangible benefit.
Cost savings through boosting innovation
DNV GL is developing a range of new innovative approaches in conjunction with the industry. This includes our electronic passport system to provide transparency to many stakeholders engaged in the late life and decommissioning phases; our e-verifi suite for major efficiency improvements on handling design and in-service verification can bring savings of up to 30%; and the development of improved risk based inspection techniques to justify residual life assessments on the older drilling fleet, also brings substantial benefits.
Cost savings though enhancing collaboration
Big data is changing how the industry understands projects and operations. Reducing costs and maintaining safety levels is a challenge. Safety barrier management is well established in the industry, employing audits and inspections to ensure the barriers are robust. Real-time or near-real-time information from many sources can also enable a step-change improvement to safety barrier management at a reduced cost. DNV GL has started a dialogue with the industry to develop Dynamic Barrier Management (DBM).
Cost savings though extending standardisation
At DNV GL, we continue to invest 5% of our revenue in research and development. Much of this is done through Joint Industry Projects (JIPs) which produce simpler codes, standards and recommended practices that can be used by the whole industry. More use of industry-wide standards rather than individual company specifications can lead to significant cost being taken out of the supply chain, through increased standardisation.
We have launched a number of JIPs in the area of standardisation in 2015. Two examples are: investigating affordable composite components for the subsea sector and qualification technology for more efficient linepipe production processes and a collaborative project with the US regulator and a number of oil majors to study and develop guidelines for quality, design, fabrication and installation of subsea bolts.
2016 will continue where 2015 left off, with an industry trying to find more costs savings. But, having done the easy actions, we will need to be more creative and look to smarter solutions through reducing complexity, boosting innovation, enhancing collaboration and extending standardisation.
However, our challenges do not stop here. The COP21 Paris agreement will put the focus back on decarbonising the global economy. The oil and gas industry will need to be proactive in the debate on carbon tax, increasing energy efficiency, integration with renewables and making carbon capture and storage a reality. We are also faced with an ageing workforce who will need significant renewal over the next decade. We will need to work exceptionally hard for the industry to be seen as an attractive employer given the industry slump, high profile job losses, and climate change agenda.
DNV GL, together with the industry, is ready to tackle the challenges of the ‘new normal’ to ensure 2016 is safer, smarter and greener.
Hari Vamadevan is the regional manager, UK and West Africa with DNV GL – Oil & Gas.
Recommended for you
