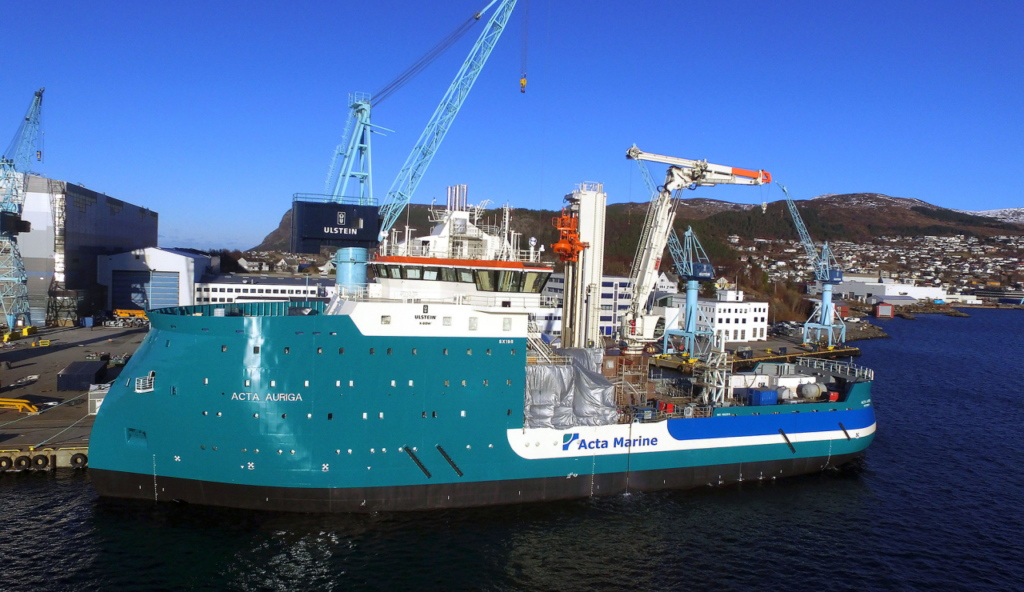
Dutch company Acta Marine, which has an offshore walk to work vessel currently completing at Ulstein Verft, has now ordered another one even before the Norwegian yard has delivered the first.
Acta is blazing a trail as the soon to be delivered Acta Auriga is the latest of a still new breed of offshore construction and service vessel pioneered by Ulstein and which is aimed at the offshore wind market.
Known as the X-stern, the SX195 class measures 93.4m in length overall by 18m in breadth. It is fitted with a large, centrally positioned walk to work motion compensated gangway and elevator tower for personnel and cargo transfers.
The unit was developed and manufactured by Dutch company SMST, which has also provided a 3D compensated SMST crane capable of 6-ton cargo lifts in wave heights to 3m.
On-board logistics includes large storage capacities, of which half is under roof in a controlled environment.
The vessel is equipped with a fuel-efficient propulsion and station-keeping system and is designed to work “stern-to” when operating infield.
The stern resembles a late 19th Century “dreadnought” cruiser stern but with a reversed upper rail to help throw seas. With all superstructure forward, the X-stern hull naturally weathervanes comfortably with its back end pointing into the wind and seas with minimal slamming.
A bonus of this Ulstein design is that, when working in-field, ship’s crew and wind turbine servicing personnel should enjoy relative peace and quiet when resting.
The vessel can accommodate up to 120 persons in 80 cabins. The facilities on board are described as modern, high quality and possessing a “home away from home” atmosphere.
Acta Auriga is scheduled for delivery this month and the latest order is slated for delivery in Q2 next year.
Meanwhile, Acta has recently been awarded a two-year contract that will see Acta Auriga go to work for Ocean Breeze Energy (OBE), owner and operator of the 400MW wind farm Bard Offshore 1, which is located 100m offshore in the German Bight sector of the North Sea.
Taking an Ad Hoc approach
Taking a different approach to offshore energy support, Ad Hoc Marine Designs has developed a large new variant of its successful 26m and 33m class SWATH-style service boats that is claimed to offer better transit performance and access in challenging sea conditions.
Named the Typhoon Class SWATH this 41m design is claimed to provide operators with a viable alternative to ordering larger vessels for servicing requirements.
This new design will be offered for building by Aluminium Marine Consultants of East Cowes, Isle of Wight and will also be available as the basis for patrol vessels and ferries.
Ad Hoc favours the SWATH – small waterplane area twin hull – as it enables rapid transit of personnel offshore in relative comfort, but it will require larger vessels as the next generation of windfarms migrates further offshore.
The 41m walk-to-work capable crew transfer vessel has been designed to run in significant wave heights of up to 3.5m and has been largely developed from experience with the 26m MCS SWATH 2, which is in service with Maritime Craft Services (Clyde) Ltd.
This Typhoon Class design will be powered by four CAT 3512C diesel engines which are rated at 1678kW each. This is expected to deliver a transit speed of up to 25 knots.
According to Ad Hoc: “By running on just one or two of the engines when located at the facility or just the generating sets when in hotel mode for long extended periods, operators can reduce fuel consumption.”
The new design will have the capability of remaining at sea for up to two weeks at a time and provide accommodation for up to 24 technicians in their own individual cabins. It is also capable of carrying any combination of 4 ISO containers.
The vessel will be equipped with Island Engineering’s zero heave mode built-in to the motion control system. Ad Hoc says that this will ensure that the whole vessel is ‘heave damped’ and therefore should not require heave dampened gangway for transfers.
New attempt to harness Magnus effect
Changing focus to next generation high efficiency vessel designs that are not wholly dependent on diesel to fuel their propulsion systems, C-Job Naval Architects has delivered the design for a wind-assisted general cargo vessel to Dutch shipping company Switijnk Shipping.
The 8,500 deadweight tons vessel will be equipped with two Norsepower Rotor Sails that will supplement the main engines and is expected to achieve fuel savings of approximately 14%.
C-Job was approached by Switijnk Shipping following its involvement in the European Union Interreg project S@IL, for which C-Job developed the earlier design of a 4,500DWT Flettner Freighter.
C-Job designed this smaller vessel with four Rotor Sails. However, after studying the prevailing wind patterns on Switijnk’s proposed sailing routes, C-Job decided to design a new vessel, called the FF8500, with two larger Rotor Sails.
Rotor Sails are deck-mounted rotating cylinders that utilise the Magnus effect to create a propulsive thrust. In a rotor ship the rotors stand vertically and lift is generated at right angles to the wind, to drive the ship forwards.
The Magnus effect is a force that acts on a spinning body in a moving airstream. Because the Magnus effect acts perpendicularly to the direction of the airstream, the optimum wind direction for Flettner ships is at 90 degrees to the direction of the sailing.
The Flettner ship concept is nearly 100 years old but is enjoying something of a revival.
German engineer Anton Flettner was the first to build a ship which attempted to use the Magnus effect for propulsion.
Assisted by Albert Betz, Jakob Ackeret, and Ludwig Prandtl, Flettner constructed an experimental rotor vessel. In October 1924, the Germaniawerft shipyard completed a large two-rotor ship named Buckau. In 1926, a larger ship with three rotors, the Barbara, was built by the shipyard AG Weserin Bremen.
But World War 2 and cheap marine fuels put paid to further development until around 20 years ago.
“Our experience from the Project S@IL study showed that Rotor Sails were the most viable choice compared to other wind assisted propulsion systems,” said C-Job business manager Jelle Grijpstra.
“And then, together with Finnish Rotor Sail supplier Norsepower, we concluded that two larger rotor sails were most effective for this project. This was because these would yield a comparable propulsive force to four smaller units. Also, with two rotor sails, one on the bow and one on the stern, there would be no chance of wind shadows affecting performance.”
A final decision on the ship’s main propulsion package has not been made. LNG-fuelling is being considered as an option.
With the concept design of the vessel complete, the next stage of the project will consist of testing the design at Maritime Research Institute Netherlands (MARIN).
The intention of this velocity prediction research is to validate the design and to quantify the fuel savings to be gained prior to inviting investors to take risk.
Recommended for you
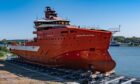