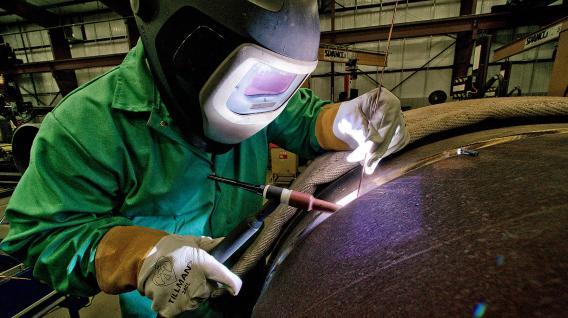
GE Oil and Gas demonstrated a clear example of the kind of collaboration the industry has been calling for with the launch of its latest high-performance wellhead system at this year’s Subsea Expo in Aberdeen.
As one of the biggest players in the subsea wellhead market, GE sought the collaboration of global operators before delivering the new SFX system, which offers a standardised, fatigue resistant system that reduces delivery lead times by 50% compared to previous ones.
GE began development of SFX in 2014 as the oil and gas industry got serious about taking costs out of the supply chain.
The company’s aim was to deliver a subsea wellhead system that improved fatigue resistance and could be used in a wide variety of applications including super-demanding deepwater environments.
GE’s global subsea services and offshore leader, Nick Dunn, said the SFX was an evolution of the field proven architecture developed in the company’s MS 700 and MS 800 wellheads.
Dunn said: “It was clear back in 2014 that to reduce costs and streamline operations a standardised approach was required.”
“We approached six major operators to understand their specifications and developed a product that would significantly reduce complexity, variability and have a far shorter lead time on project-specific applications.
“As the oil industry has evolved wells are getting deeper and longer and we’re going into harsher conditions to find oil.
“Specific fatigue concerns were leading to customer specific customisation and sucking in a lot of engineering hours and costs.
“With SFX we have pre-manufactured the components, we’ve done a lot of the standardisation and taken out a lot of the cycle cost. Customers can step in to do some configuration, dependent to their specific needs and offers variability point towards the end of the cycle.”
The entire SFX manufacturing process is verified and certified by Lloyd’s and DNV-GL. The SFX system includes wellhead, pipe, and casing connectors which meet or exceed industry standards for materials, quality, and fatigue performance.
Dunn added: “It has allowed us to create a system that covers the hundreds of different part numbers we were having to generate and yet we’ve not had to compromise on the integrity of the product we’re delivering to customers.
“We use the same suite of tools and operating procedures we developed on the MS 700 and MS 800 and built them into the SFX.
“Our aim was to deliver a simpler, faster, stronger wellhead system. SFX has a 16 times fatigue improvement and we’ve reduced lead time by 50%. For the operator, productivity and savings can cover wellhead system cost.”
Dunn added: “We have a global contract with the likes of Statoil, who we have been working with, are comfortable with what we are doing and how we’re going to control it.
“Everyone is talking about taking costs out of the supply chain but unless we start collaborating on these things, it’s just never going to happen.”
Recommended for you
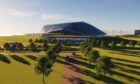