
An Aberdeen company has found a way of packaging differently, standard equipment used for the jointing and laying of steel pipelines of moderate diameter, to enable such work to be carried out aboard a standard DP2 offshore support vessel.
The technologies are tried and proven; it is their application that is different and it is Cortez chief executive Alistair Cowie who is leading the charge and believes that the cost savings of the company’s modular approach could be huge.
And at the heart of this offshore pipelay revolution potential is a pipeline sections friction connector that has been the standard for onshore fields for some 30 years, the NOV Zap-Lok.
It is routinely utilised on thousands of miles of flow lines, gathering lines, water lines and aided-injection systems.
By marrying this approach with a relatively simple modular pipelay system developed in-house, Cowie believes the company is on to a winner.
He is contemplating building a stable of four systems within four years at a total cost of some $9.6million (£6million). Development costs so far have been around $800,000 (£500,000).
Cowie sees this approach as being highly cost effective in the Southern North Sea and other relatively shallow offshore oil and gas provinces worldwide where conventional carbon-steel pipe suffices, without the need for insulation coatings.
Carbon steel accounts for the bulk of the global pipe-lay market, including as much as 80% of the Southern North Sea and Cowie says that, with Zap-Lok, the complexities and costs associated with reeled steel pipe-lay and the sophisticated welding systems currently utilised are bypassed.
Around $135billion of spend in subsea hardware is anticipated in the next five years with pipelines accounting for half of this forecast expenditure.
In this environment, access to manpower, vessels and subsea equipment will be at a premium. And one of the most expensive components of any pipeline construction project is the enormous amount of skilled man-hours required for welding.
There is no need for a reel-layer, instead a reasonably standard DP2 OSV, perhaps with a 100-tonne crane on board; there is no need for a spool base, instead standard sections of pipe can be loaded at any suitable port close to the action, such as Immingham for the SNS; and welding is eliminated; and charter rates are dramatically lower, perhaps around $80,000 per day versus $320,000-480,000 per day for a current generation reel-ship.
As pipes roll off storage racks that will form a part of the modular system, they would be pushed through an hydraulic press and then S-laid on to the seabed at a speed of three to five minutes per joint, (which is a daily rate of 5-7km).
“We believe our system will be more efficient than standard S-lay in water depths to 120m,” said Cowie, adding that a DP2 OSV.
“This means any Tier 2 contractor can carry out pipelay activities, eliminating the need to wait for dedicated pipelay ship or contractor availability and make the whole process faster and more cost effective.”
Physical testing of the package assembled by Cortez is about to go for testing in Houston and the hope is that the use of Zap-Lok in this way for offshore applications will successfully measure against the PDA10 Code and that approval will be secured by the Spring.
The first user of the system in UK waters could be Centrica, which has co-operated closely with Cortez throughout the gestation process, which started in 2012.
Cowie intends to limit first applications to 12-in diameter piping but see this limit being increased to 16-in by the end of this year.
“I see this as changing the dynamic of the pipelay market and various contractors are speaking with us. When they learn how simple our system is, heads lift and eyes open wide.”
Recommended for you
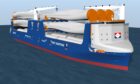