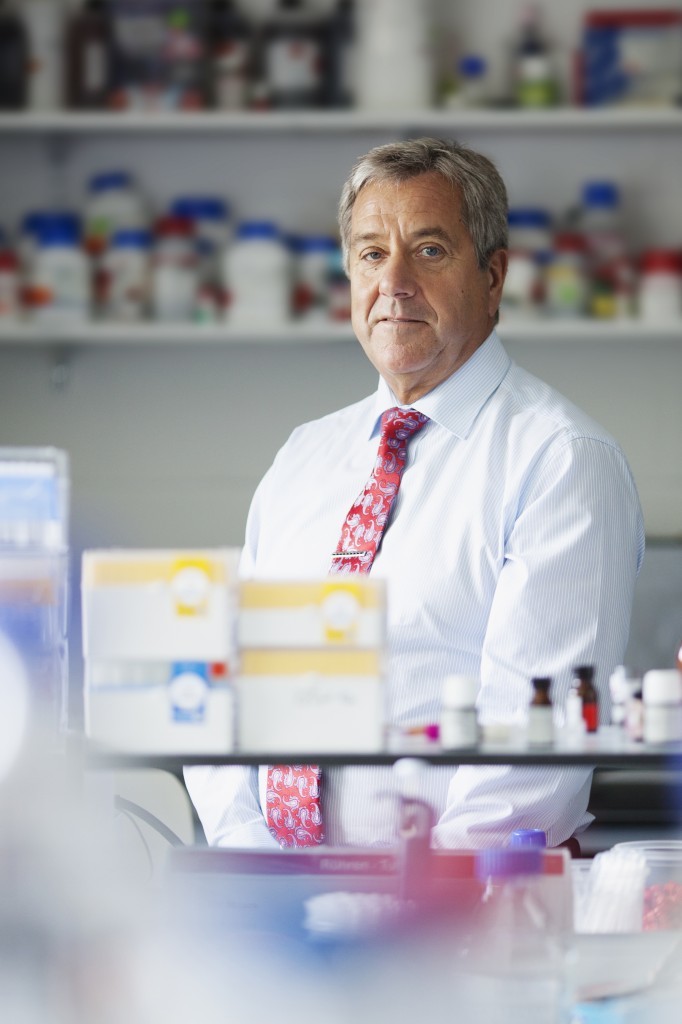
With this year marking the 50th anniversary since oil and gas was first discovered in the North Sea, the subject of ageing assets and asset maintenance is a hot topic of conversation across the industry. There is a misconception that mature assets are unreliable, unsafe and inefficient, but with a robust and proactive asset integrity management strategy in place, this is simply not the case.
The industry is well aware that corrosion poses one of the biggest threats to assets, not just offshore, but onshore too. It is also notoriously expensive and difficult to treat, and therefore understanding the corrosion prevention methods and technologies available to the industry is essential. Considering the current industry climate, and that pipelines can cost up to $3million per km to replace, putting the solutions in place which prolong the lifetime of infrastructure and avoid preventable damage is extremely valuable to operators.
The energy industry is constantly evolving, and in doing so, we look to get more from our assets as the industry drills deeper and exposes infrastructure to more hostile environments, with higher pressures and temperatures. These environments are a welcome place for corrosion, which, if not effectively managed could cause ruptures to production infrastructure. This could threaten the safety of personnel as well as posing huge environmental, regulatory and reputational risks. With the safety of personnel being a top priority across the entire global industry, operators must ensure they have robust monitoring and inspection regimes, corrosion monitoring techniques, risk assessments and active maintenance programmes in place to safeguard against risk.
Alongside these regimes and assessments, there are a number of corrosion mitigation methods available to the industry to help in the fight against corrosion. However, these solutions are often difficult to monitor and measure, and this results in unnecessary costs for operators, and the potential to damage production systems.
One of the most common corrosion mitigation methods adopted by the upstream oil and gas industry is the use of corrosion inhibitors. These inhibitors form a protective barrier on corrosion-prone surfaces and protect infrastructure from corrosive attack. This technique is effective, but only when the optimum dosage is injected into the system, which can be difficult to determine without the appropriate technology.
A simple way of explaining this is using the ‘Goldilocks Principle’; if you under dose corrosion inhibitors, you increase the risk of corrosive attack, but overdosing is costly and can cause upset to the production system and the surrounding environment. Finding the optimum dosage is therefore key, and results in the significant reduction in costs, improved and informed decision making, and less inhibitor being discharged to the environment.
The industry is well aware that collaboration is key to ensure sustainability and success, and Offshore Europe 2015 provides the perfect opportunity for the industry to share best practise and showcase new technologies which will help to keep ageing assets safe and reliable, and ultimately drive the industry’s development forward.
Charles Cruickshank is the chief executive of LUX Assure.