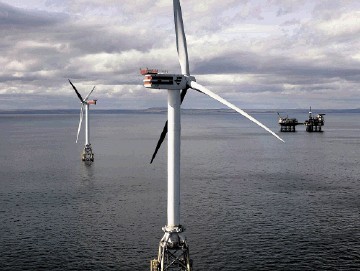
There is no doubt that the UK-based offshore oil & gas supply chain is making heavy weather of the current downturn; not just in its domestic market but overseas too.
The North Sea has been hit hard and, one year in, there are no signs of pressure easing; rather it has intensified in recent weeks.
There is a consensus developing that points towards a prolonged slump and that, to stay in business, the supply chain in Britain will have to go back to basics, get fit and learn to succeed in a very different oil price environment of little over a year ago.
Diversification has to become core business . . . not just as a diversion to get out of a tight corner as has so often been the case over the 40 years since first UKCS commercial oil production started; a bit earlier in the case of gas.
During the late 1990s slump, a core element of the 10-year plan that grew out of that crisis was diversification of the oil & gas supply chain into complementary opportunities.
The plan had been launched by the Oil & Gas Industry Taskforce and was to be overseen by the UKCS steering group PILOT.
The diversification dimension was seized upon by Aberdeen City Council and propelled by its then economic development top official, Gordon McIntosh, who, like Energy’s editor at the time, immediately saw the long-term offshore renewables potential, so leading to the creation of Aberdeen Renewable Energy Group.
However, though there has been some success on the maritime renewables front . . . from fabrication of prototype wave and tidal devices at Nigg on the Cromarty Firth; to a modicum of engagement by subsea contractors and engineering houses in Aberdeen; to jacket sub-structures for large turbines at Burntisland; to various engineering, fabrication, able manufacture and offshore support activities out of the English north-east, north-west; Humberside and the Norfolk ports . . . it has been limited by comparison to the other side of the North Sea.
If one asks the question, where does the real supply chain power in North Sea maritime renewables lie? The answer is that it unquestionably resides on Continental shores. One measure of this is to look at the names, domiciles and capabilities of the companies building and operating offshore windfarms.
By the same token, this also applies to who owns and operates the now thousands of turbines planted out there, the majority being located in UK waters.
As for significant intellectual property, big equipment and systems manufacturing brands, those too are located on the wrong side of the North Sea from the perspective of any “true blue” Brit who might believe that the UK has lost out in the renewables power generation race except in terms of the offshore turbine count.
The UK’s leadership in offshore wind claim is tissue thin; the only real leadership being the total installed capacity and current investment commitments. In almost all other respects, Britain is a follower.
Even the initial lead in offshore construction vessel tonnage was quickly lost; Energy is referring to the Mayflower Resolution originally ordered by the UK bus builder Mayflower Corporation in the early 2000s. In March 2004, Mayflower was put into administration (Deloitte Touche) with debts of £17.7million.
Resolution was sold by the administrators for £12million to a group of Mayflower Corporation’s managers who managed to get backing from Japanese bank Mizuho International. MPI is today a part of the Dutch Group Vroon.
Sea Jacks of Great Yarmouth has always been owned by foreign interests, even if it is UK domiciled; first Norwegian, then US (in effect), and currently Japanese. Also, it is exceptional in that it has always played in both renewables and oil & gas.
The UK oil & gas supply chain could reverse that, at least to some extent bearing in mind that much of its cutting edge and heavyweight capability is foreign-owned; like Acergy and Technip for example. Now for some numbers. Anyone who said wind-power was doomed to failure 20 years ago has been proven wrong, including offshore. The International Energy Agency stated at the UTC conference in Bergen this summer that onshore wind was challenging natural gas, at least among OECD nations.
The recently published 2014 European Commission – Joint Research Centre (JRC) wind status report presents the technology, market and economics of the wind energy sector with a focus on the EU. The numbers speak for themselves.
According to the JRC, wind power is the renewable energy which has seen the widest and most successful deployment over the last two decades, increasing the global cumulative capacity from 3GW (gigawatts) to 370GW.
Expressed another way and using the UK’s originally wholly coal-fired, 3GW Drax power station as the measure, capacity has leapt from one Drax to more than 120 Drax equivalents in wind energy.
Last year represented an annual record with 52.8GW of wind turbines capacity installed worldwide, a 48% increase compared to 2013 and 17% over the 2012 record of 45.2GW.
2014 saw a 23% increase in annual installed offshore turbine capacity from 1.564GW to 1 931GW, compared to a 13% decrease in 2013. Most was North Sea capacity.
The EU’s grid connected cumulative capacity in 2014 reached 129GW (43 Drax equivalents), meeting 8% of European electricity demand, equivalent to the combined annual consumption of Belgium, the Netherlands, Greece and Ireland.
Focusing offshore, the 2020 projections from the National Renewable Energy Action Plans (NREAP) suggest that maritime installations will increase from 8GW to 38GW (or an almost four-fold increase from 2014).
But the JRC doesn’t agree, predicting 27GW offshore Europe and 40GW globally. It notes that both France and the Netherlands will fail to meet their ambitious 2020 offshore targets of 6GW and 5GW respectively.
Worldwide offshore is in any case proving slow at taking off, with China failing to meet its targets of 5GW installed by 2015, with 30GW by 2030 as the long-term target. The US continues to experience a slow start with only 30MW likely in the medium term.
The JRC says the offshore market offers continuous but not “explosive” growth potential.
The main reasons include the perceived benefits from developing a new technology in terms of competitiveness, the extent of the wind resource available, the wide public support, and the clear prospects for cost reductions.
Doubts notwithstanding, the JRC states that, based on current predictions, wind will account for at least 12% electricity share by 2020 in the EU, a significant contribution to the goal of the European energy and climate package of 20% share of energy from renewable sources.
Offshore installation
One of the problems restricting the development of offshore windfarms, and increasing their cost, is the noise generated by existing methods of installing monopiles, and the impact that this noise has in particular on the hearing and navigating abilities of marine mammals.
Different methods are being explored to reduce this noise including vibro-driving, bubbles curtains and others.
The UK’s Carbon Trust under its Offshore Wind Accelerator programme is supporting the substitution of vibration piling for hammering as the most popular technique for installing monopiles.
JRC claims that older installation vessels, basically modified existing jack-ups, will not be able to install the next-generation wind turbines (farther offshore and in deeper waters) at a rate that can significantly reduce the cost of energy.
“The first generation of specialised (wind-only) installation vessels that came into play during 2010–13 are much more capable in respect of installation at the current distances to shore and water depth, but they will show their limitations with the next generation of offshore turbines and with XL monopoles,” says JRC.
“A significant part of the approximately 15–25GW of offshore windfarms that will be installed during 2015–23 will use XL monopiles and turbines whose nacelle (weighing 350–450 tonnes) has to be lifted to above 100m . . . higher than nearly any turbine installed offshore so far.
“Those turbines, mostly rated in the 6–8MW (megawatt) range, can be transported and installed by some of the existing installation tonnage – but the deck space in these vessels is limited and not many turbines can be transported in a trip.
“Next-generation installation vessels must be capable of covering those specifications, and to carry 7–9 new turbines per trip at a high transit speed (15 knots), or else alternative transport must be designed.”
The EU’s four-year FP7 project Leanwind (which started in December 2013 with an EU contribution of 10million euros) is aimed at applying lean principles to the critical project stages of offshore windfarm project development.
The objective is to streamline the flow between the different stages and to remove complex and wasteful phases during installation, operation and maintenance as well as decommissioning.
The main preliminary findings of Leanwind are:
Innovations related to offshore installation offer a potential cost reduction of around 10–15% by reducing the time needed for the various installation operations; and extending the availability period of time to operate under unfavourable meteorological conditions.
New techniques are being developed to improve the accessibility of wind turbines to technicians in order to undertake unplanned maintenance depending on weather conditions. The current typical sea-state limit is 1.5m of significant wave height and 12 metres per second wind speed at turbine hub height. However, it would be desirable to ensure accessibility to the wind turbines with waves of 3m significant height.
Increasing automation for surveillance and monitoring of wind turbines may provide a reduction in the “levelised” cost of energy by limiting manned interventions just to heavy maintenance.
Operation and maintenance activities can be optimised by applying optimal decision-making techniques based on risk-based approaches.
International standards for data capture, storage and presentation should be adopted by the wind power industry. The availability of open data protocols would enable development of new and innovative solutions. Two main variants of standardisation are described in the results of the project, namely: development of standard operations for operation and maintenance activities that would be applicable to many different wind-farms/wind turbines; and specification of the minimum requirements to ensure a sufficient safety level for personnel.
Turbine brands league
At the heart of the wind market on- or offshore, is the power head. But who dominates the market today?
Looking at just this year and last, the offshore market was led by Siemens with 68% of installations (measured in MWs) followed by Areva (Turbine M5000-116), Vestas (Turbine V112-3.0) with 13% each, and finally Senvion (Turbine 6.2M126) with 7% of the total.
Windfarms have now reached similar capacities to conventional generation plant. Currently, the largest windfarm in the world, Alta Wind Energy Center in California, has installed capacity of 1.32GW. In Europe, the largest windfarm onshore is Fantanele-Cogealac in Romania with 600MW and offshore it is the London Array with 630MW.
The five largest firms together covered 48% of the market (source: BTM, 2015), showing similar levels of market concentration during the last six years, ranging 47–55%.
However, the share of the top 10 manufacturers slowly but continuously diminished from 93–94% in 2005/2006 to 70–72% in 2013/2014.
European manufacturers increased their market share from 42% in 2009/11 to 48% in 2012/13 and then down to 43% in 2014 (source: BTM, 2015; JRC data).
Given that the Chinese market is overly dominated by local manufacturers, this means that European manufacturers had a 78% share of the global non-Chinese market. However, this share will be reduced mostly because of Chinese policies: their financial institutions that are starting to fund projects abroad require Chinese equipment to be used in those projects.
On the operations & maintenance front, most countries are now signing up for 5-15 years of maintenance; in other words long-term contracts.
According to JRC, there are various implications. For example, the longer the O&M service included with turbine purchase, the less O&M market is left for third parties.
Also, the O&M market is increasingly interesting for manufacturers. At the end of last year, Vestas had a wind turbine order backlog of 6.7billion euros (7.513GW aggregate capacity) and a service order backlog of 7.0billion euros.
The OEMs are also now influencing service vessel design, Siemens, for example, has an agreement with Danish standby vessel fleet owner Esvagt to develop, build and operate tonnage suitable for offshore wind.
Every turbine, foundation structure, transformer platform and in-farm cabling and power interconnector represents a business opportunity on both the CAPEX and the OPEX fronts.
This suggests that all companies within the oil & gas supply chain with transferable capabilities should henceforth be looking a lot closer at and winning work in maritime renewables, especially offshore wind.
Recommended for you
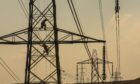