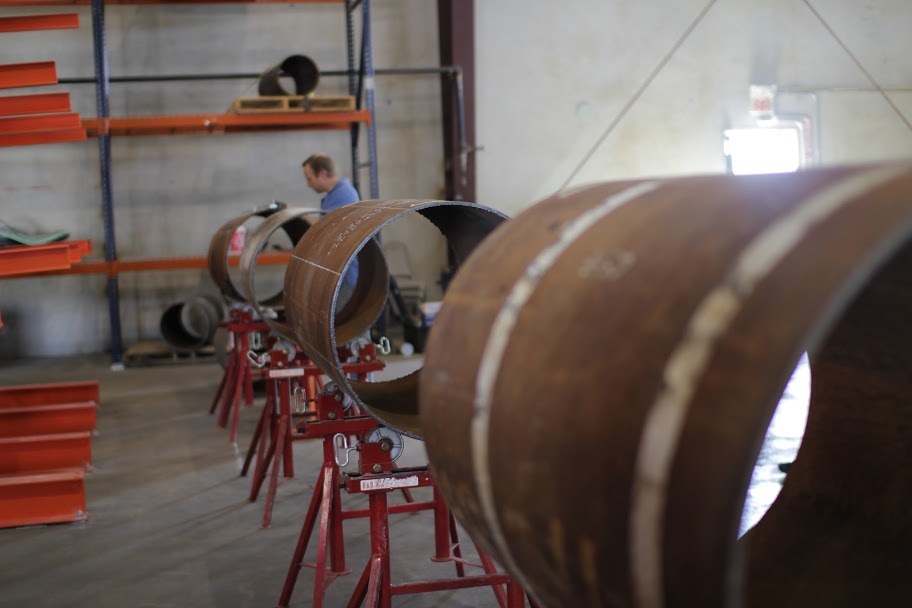
With the recent news that the UK government is looking to encourage investment in the UK Continental Shelf (UKCS) with a new competition, it is clear there is still interest in North Sea oil and gas.
Having been heavily explored since 1964, the UKCS still has fossil fuel deposits left that, with the right devices and solutions can be reached and extracted.
Testing these devices and solutions in a controlled and cost effective manner will be an important step in finding the next set of oil wells in the UKCS. Devices that are expected to spend time in these deep sea environments will consequently need to go through rigorous downhole testing.
Continued environmental and regulatory pressures have impacted manufacturers the world over.
Those in the UKCS region in particular face robust manufacturing standards under strict UK and EU law. Indeed, most oil companies now will not let new products into service unless they have gone through the Technology Readiness Level treadmill, requiring them to undergo rigorous physical testing of components at full scale and for significant time periods, to imitate real world environments.
Then there are operating cost pressures associated with the benefits of long service life. Interventions in the event of a break-down, frequently involve the mobilisation of specialised technologies and can significantly impact production.
To minimise the risk of a costly well shut-in, greater emphasis is now being placed on the reliability of subsea systems, and realistic down-hole testing of subsea components as a critical part of product development, testing and approval.
Furthermore, with an increase in the uncertainty surrounding the UKCS area, there is also a clear need for equipment to be built for use in more hostile environments elsewhere if necessary.
This kind of component testing can be difficult to conduct. Replicating the down-hole conditions that equipment will see in the field isn’t easy. Manufacturers have typically used computer simulations or modelling rather than physical testing.
This carries its own inherent risks, with unforeseen “real-life” conditions not being factored into the models. Also the computer simulation of multiphase flows is often simplistic at best, and often requires physical testing to validate the computer models developed.
Downhole testing that is onshore and able to replicate a variety of real life conditions is now being sought in the UK. UK-based facilities at BHR Group’s Cranfield facility can now offer 40bar at the base of the well, simulating a 400m fluid depth and are able to test with a variety of fluids in single or multiphase flow at elevated pressure and temperature for extended durations.
In addition, they also offer testing systems with CCTV and sensors for data collection, designers and manufactures can then see a live feed of images and data via VPN of how parts are performing.
This can be a game changer for many subsea equipment providers, particularly those in the UKCS where having a testing facility nearby can save significant amount of money and time.
Dr Carl Wordsworth is senior consultant at BHR Group