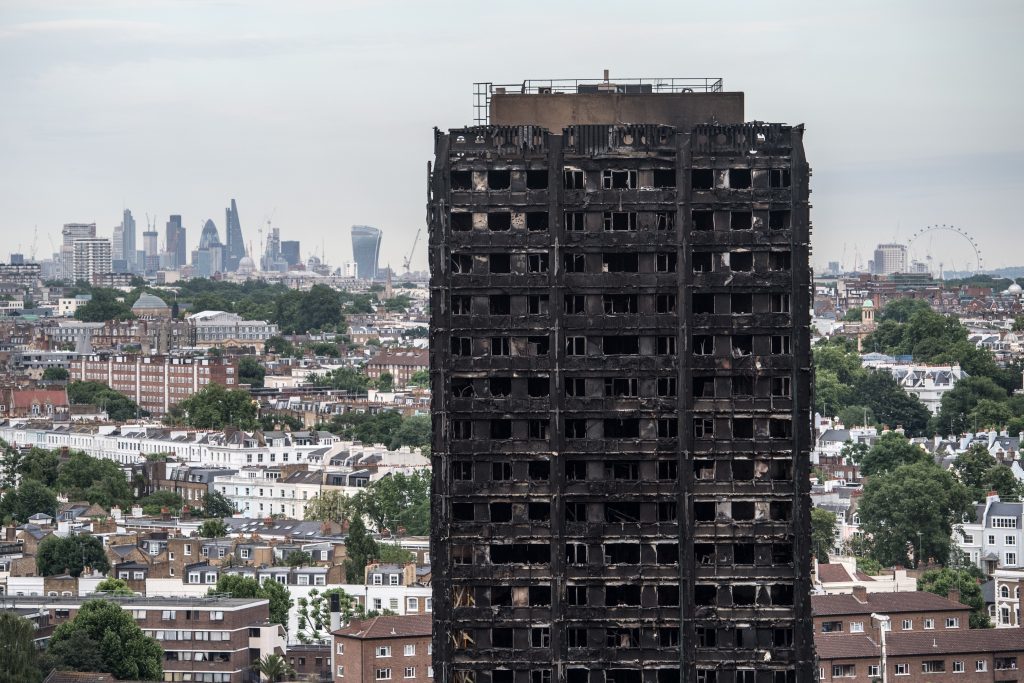
There can hardly be a single one of us who wasn’t aware of and touched by last month’s Grenfell Tower disaster. The images, stories and indeed the mere idea of people trapped within a blazing structure had a massive – and immediate – impact on our society. The resulting social unrest, calls for legislative change and national programme of health and safety checks have continued to hit the headlines in recent weeks. Unfortunately, the catalyst required to call an enquiry was a fatal disaster, but from what I read, it appears that things are moving fast to ensure that tower block fire safety procedures will now change for the better.
Now think back to Piper Alpha and see if we can draw some parallels between the two tragedies. There are the obvious comparisons – a horrendous loss of life, a community bound together in mourning and an awareness that all might not have been as it should be, in terms of safety procedures. Whilst we can’t predict the outcome of the Grenfell enquiry, I suspect that is where the similarities end.
29 years after our industry’s worst ever disaster, we are still using the offshore fire safety products and test procedures which were found to be a significant contributing failing factor noted in the Cullen Report. For as long as the North Sea oil and gas industry has existed, sprinkler heads on offshore firefighting systems have been blocking and failing. This is due to the fact that they were originally invented and designed almost 100 years ago for fresh water systems, and therefore are unable to cope with the marine by-products produced by a sea water delivery system.
These by-products not only contribute significantly to expensive and repetitive service and maintenance regimes, but have resulted in a culture of “fail and fix” compliance test procedures. A “pass” will never be set at 100% on first time system activation and normal test criteria is set well below this figure and allows for repeat testing until a pass is recorded. These regimes vary from operator to operator, but one thing remains constant; you never get a second chance with a real fire.
When an offshore fire safety system is activated it will fail on first time activation where delivery line contamination is present, due to the sprinkler nozzles blocking regardless of delivery line material: the sprinkler heads will then be removed, cleaned, re-instated and tested in this way until a pass is recorded. Hard to credit, isn’t it?
It was noted in the Cullen report that concentric corrosion and scale from delivery lines contributed to the Piper Alpha fire sprinkler system failing, pre-fire; it didn’t stand a chance during an unplanned event. And yet, that disaster was not enough of a catalyst to change offshore fire safety systems and procedures.
Incredibly, the fail and fix process remains because it’s “just how we’ve always done it”. In other words, don’t forget to hold on to handrails, make sure you put a lid on your hot drink, and – most importantly – continue to implement and use proven to fail products and test regimes to achieve a compliance approval for your safety critical system.
It beggars belief, and certainly made me end my own offshore career in order to create a solution for salt water fire safety compliance.
Earlier this week, Jeremy Cresswell noted that “we cannot afford another Piper Alpha. But the clock is ticking”. He is 100% correct. And when the inevitable does happen, who will be held responsible? The product company for failing to note on their data sheets that their nozzles will block and fail when used in a specific environment? The service company who makes repeat money out of a fail fix process with these products? Or the operator who doesn’t change its fire safety design? If a solution is available to put an end to this senseless attitude towards offshore personnel safety, someone must take responsibility and ensure a culture shift before it’s too late before our industry it brought to its knees by another fatal disaster.
Ian Garden is managing director of RigDeluge Ltd.
Recommended for you
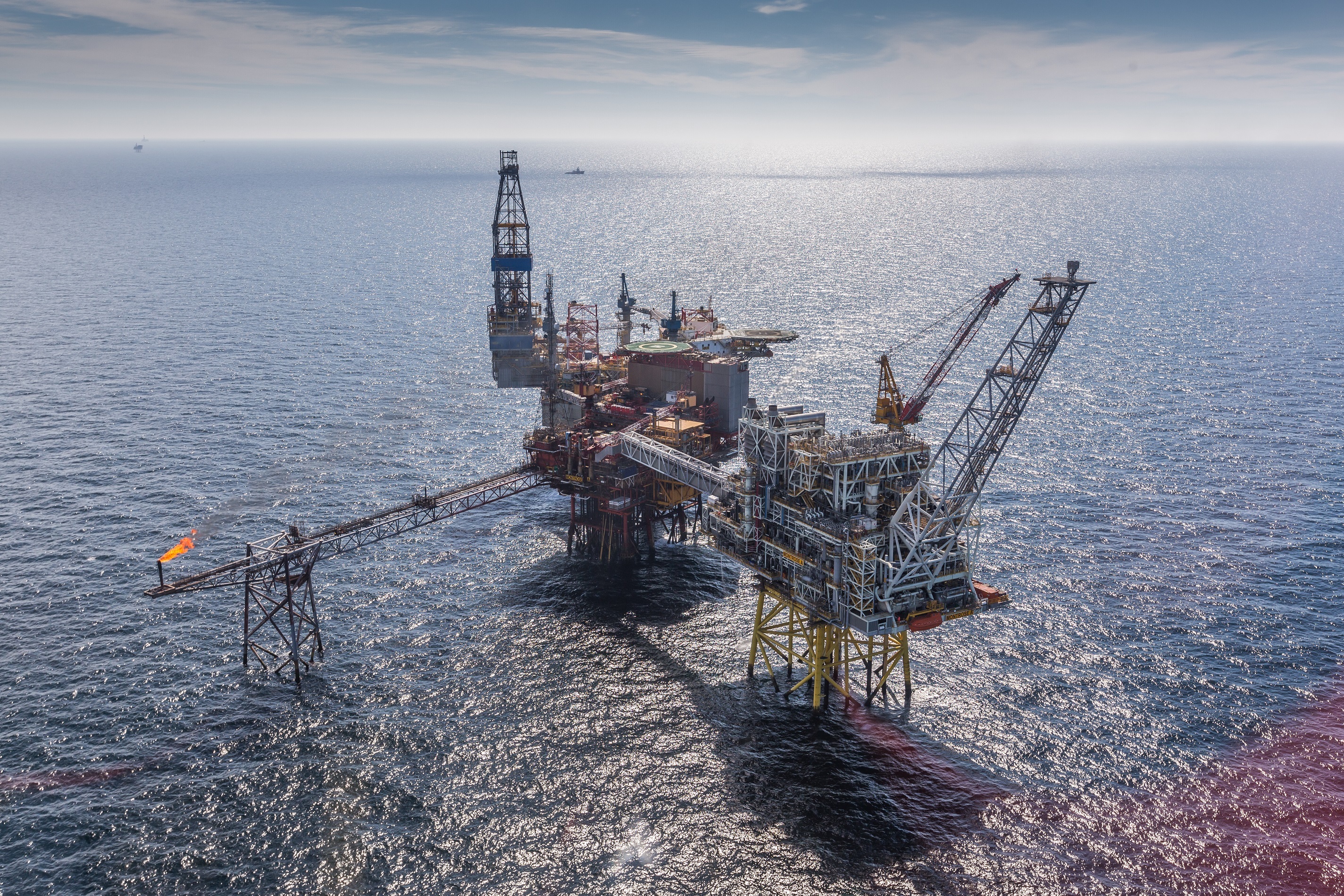