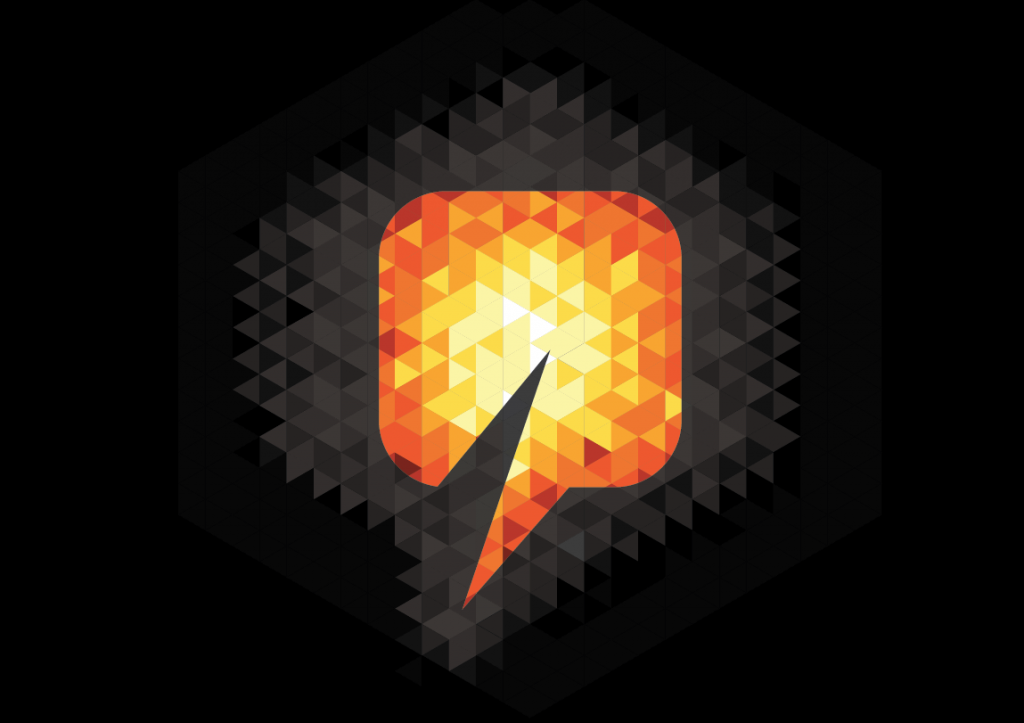
Gary Hodgson, strategic projects director at Peel Ports – who own and operate of Great Yarmouth and Hunterston ports – sets out why he believes there is a realistic model for onshore decommissioning that could reduce costs for the industry and taxpayers.
Various commentators in Energy Voice have posed questions about Scotland’s ability to develop a meaningful decommissioning sector that would help achieve cost reduction targets and create valuable jobs with export potential.
Beginning more than a year ago, we set out to answer the question, at least as far as onshore decommissioning is concerned. The results are contained in a white paper we published in November, which condenses the discussions held with more than 30 industry experts over the course of 12 months.
That listening exercise convinced us that there is a future for Scotland in this sector, but success relies on achieving several radical ambitions, underpinned by a new three-part economic model.
Firstly, on the ‘moonshots’, there needs to be a fundamental rethink of the conventional and dominant project-by-project approach. Batching work would reduce the costs of mobilisation and demobilisation. There is also the potential to secure the benefits of stacking and sequencing work to achieve smooth workflows and improve capacity usage of infrastructure and labour.
Secondly, we see the need for a ‘decom campus’ which would seek to use co-location as a means to drive efficiency improvements. It would bring together the full range of specialists involved in onshore decommissioning and repurposing, from inspection and dismantling to hazardous material management and recycling. This approach would also allow maximum value to be extracted while minimising wasted costs through transport and other logistical inefficiencies.
Finally, commitment is essential for providing the stability, predictability and certainty required for investment. The benefits of batch and scale require this. Any new solutions that will help the UK achieve its decommissioning objectives will require this investment – of money, time and faith.
As can be inferred from the above, all of these ‘moonshots’ are complementary and, indeed, highly interdependent. Investment by facilities providers and/or the government to create the necessary infrastructure is highly likely to depend on a long-term commitment by the customers of those facilities.
However, it may not be possible to secure this until the customers are clear that it will be possible to achieve the benefits required to justify this commitment. Such a ‘chicken and egg’ situation – allied with the scale of challenge – will require a greater degree of transparency, cooperation and risk than may be traditionally comfortable for many players in this market.
This means that stakeholders in the decommissioning process will need to take a different approach to co-creating solutions that the whole sector can benefit from.
Our work then went on to explore the more practical implications of our findings and some of the key enablers required to deliver it. The outcome was a three-part economic model, with each element essential to the others being viable solutions for onshore decommissioning, not only financially but in maximising safe operations, minimising environmental risk and impact, and developing exportable expertise and capabilities that can benefit the UK economy.
Economics of dry-docking
Dry docks offer potentially significant benefits for a wide range of structures that float or have a significant below-waterline component where these would be difficult to bring back directly to a quayside. Ideally, any to be used in onshore decommissioning would also have deepwater access, gate access and previous experience of either offshore structure production or decommissioning.
Economics of space
The research identified the practical challenges and limitations of small quayside footprints for onshore decommissioning activity as well as the additional costs associated with logistics and inefficiencies where complementary activities cannot be colocated. A related challenge is that it is not possible to concentrate activity on a single site, meaning it is not possible to achieve the economies of scale that are required to drive down decommissioning costs. Having adequate space is a vital prerequisite of two of the ‘moonshots’ set out above: ‘productionisation’ and the ‘decom campus’ approach.
Economics of scrap
To minimise costs it is essential to extract full value from the material salvaged through decommissioning. This means treating ‘scrap’ as an asset rather than a cost, and an activity that is seen as a job creator rather than an area where work is lost to overseas markets. Our research suggests that better use of set down, improved co-location and improved proximity to existing scrap outlets could improve yield per tonne enough to tip projects towards UK sites rather than overseas locations.
Where this leaves us is that the UK has the opportunity to drive down the cost of decommissioning, in a way that also benefits workforce safety, the environment and the UK’s export capabilities.
The three key onshore dependencies required to deliver this must all be present to allow commercial and public partners in the decommissioning process to create strategic centres that will facilitate a more efficient production-line approach. Such an approach would also present the advantage of being able to co-locate the wide variety of specialisms required throughout decommissioning.
Finally, operators and the government must make a shared and tangible commitment to realising this ambition, thus enabling supply chain and infrastructure providers to make the necessary, significant and long-term investments with confidence.