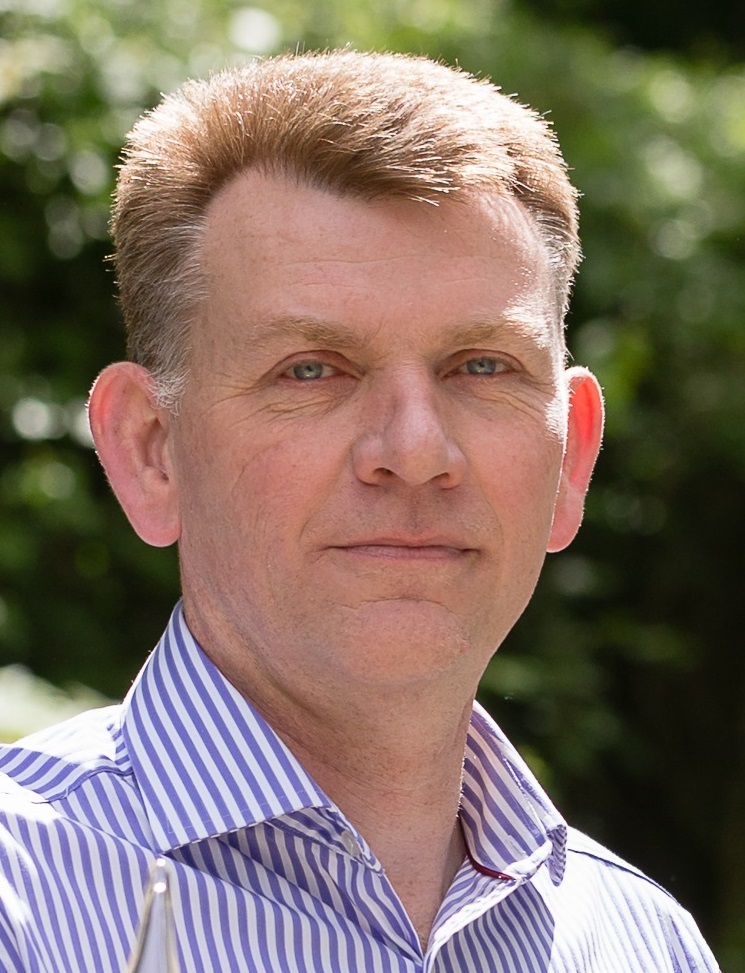
Through much of the developed world, we have come to rely on a steady flow of electricity as we have a steady flow of air. Power outages have become as unlikely as they have disruptive – we have become so used to reliable supply that most of us can no longer remember a time when we didn’t have it.
And, as the world’s population swells, the need for power is fast increasing. According to the International Energy Agency, global energy demand will grow by 30% between now and 2040, with electricity consumption accounting for 40% of the total rise .
But the continued reliability of this flow of electricity into our businesses and homes depends on the health of the system that supports it. This includes all the links in the electrical power train: circuit breakers, wiring and transformers – the latter a vital part of the grid that allows for large electrical loads to travel long distances, and smaller loads to flow into neighbourhoods and homes.
Any outages could affect quality of life, the production of goods and even GDP. It is not an exaggeration to say that uninterrupted electricity supply is fundamental to not just a company’s – but a country’s – prospects, underpinning the smooth-running of industry and development.
The price of replacement
The boom years of the 1950s to the 1980s brought with them significant investment in critical infrastructure in both the US and Europe, with power supply benefiting in particular. But as electricity demand has continued to rise, the rate of transformer installations has failed to keep pace.
The cost of installing new transformers has risen dramatically in recent years – on average 5.5 per cent annually for the last two decades, which is equivalent to a 100 per cent increase in the price of a transformer every 12-15 years .
Thus, if 30 years ago a utility spent £300,000 on asset replacement, the cost now would be closer to £1.2m.
The result? An ageing transformer fleet. In the US alone, the average age of transformer on the grid is 35 years old , which is near the end of the typical life cycle. Under ideal conditions, transformers are expected to operate for 30-40 years, while industrial transformers have a life expectancy of just 20-25 years.
This presents a growing challenge and it is in this context that asset managers need to think more carefully about how best to sustain these vital and valuable assets – ensuring that they are utilised effectively for as long as possible before the time for the inevitable replacement arrives.
Extending the life
Ageing assets can operate safely and effectively well beyond their design life, provided operators take the right steps.
While no approach will yield immortality, taking measures to prolong the life of the existing assets will be key to streamlining costs and sustaining the health of the world’s transformer fleet.
Unless thoroughly maintained, as assets age they become more prone to a range of issues that increase the risk of failure. Among these risks are overloading, a loosening of mechanical connections and the deterioration of insulation – all of which can be exacerbated over time. When a transformer reaches the end of its life – either naturally or through failure – in addition to the obvious replacement costs, the process of decommissioning one transformer and replacing it with another can lead to lengthy outage periods, disrupting the business and communities that rely on it.
The largest transformer loss on record occurred at a power plant, resulting in business interruption costs of more than $86m .
Extending asset life will be a fundamental part of financial planning when it comes to managing electricity networks – and achieving this will require proactivity and careful consideration. Measures such as more frequent maintenance and monitoring could help to buy time, but for a longer-lasting solution, a different approach is required.
A fluid approach
Dielectric fluids play a vital role in providing electrical insulation within transformers. With more than 90% of the market share, mineral oils are the foremost fluid of this kind. But, while these hydrocarbon-based oils have excellent cooling and insulating properties, they are less robust in an area that is crucial to extending transformer life: moisture tolerance. The absorption of water by the cellulose paper within the transformer over time leads to degradation, which can eventually lead to failure.
Retrofilling existing assets with ester fluids – which are able to absorb far greater amounts of moisture without compromising their dielectric strength – could be key in the fight to extending the life-cycle of existing transformer fleets.
And there are multiple benefits. Firstly, the greater moisture tolerance of ester fluids leads to a slower degradation of the cellulose paper contained within the transformer. This prevents the present status of the asset from deteriorating further, which in turn prolongs its life.
The extent to which the life is extended will depend on the degradation of the cellulose paper and the age of the transformer – but in many cases the added life could be to the tune of many years. There is also the fact that, in terms of financial planning, retrofilling is a much smaller investment than replacing a transformer. Retrofilling allows asset managers to defer the lengthy and costly outage brought about by decommissioning and installing a new transformer. In this sense, retrofilling is an invaluable financial planning tool.
Retrofilling also allows for more output from transformers. Ester fluids can operate in temperatures of up to 20°C higher than mineral oils. This allows for more power to be produced from the same footprint. In the context of rising electricity demand, the implications could be significant – though it should be noted that there are technical implications when considering retrofilling and a more detailed technical assessment may be needed for transformers above a rating of 66kV.
Transformers are among the most critical and numerous pieces of infrastructure in the electricity grid. Crucially, retro-filling transformers with ester fluids is a proactive approach which is about prevention rather than cure.
Ultimately, no matter how well maintained, a transformer will eventually need to be replaced. But with the right approach, operators can significantly extend their life cycle, defer the cost of decommissioning and help keep the lights on as the world’s electricity demand grows ever stronger.
Recommended for you
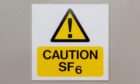