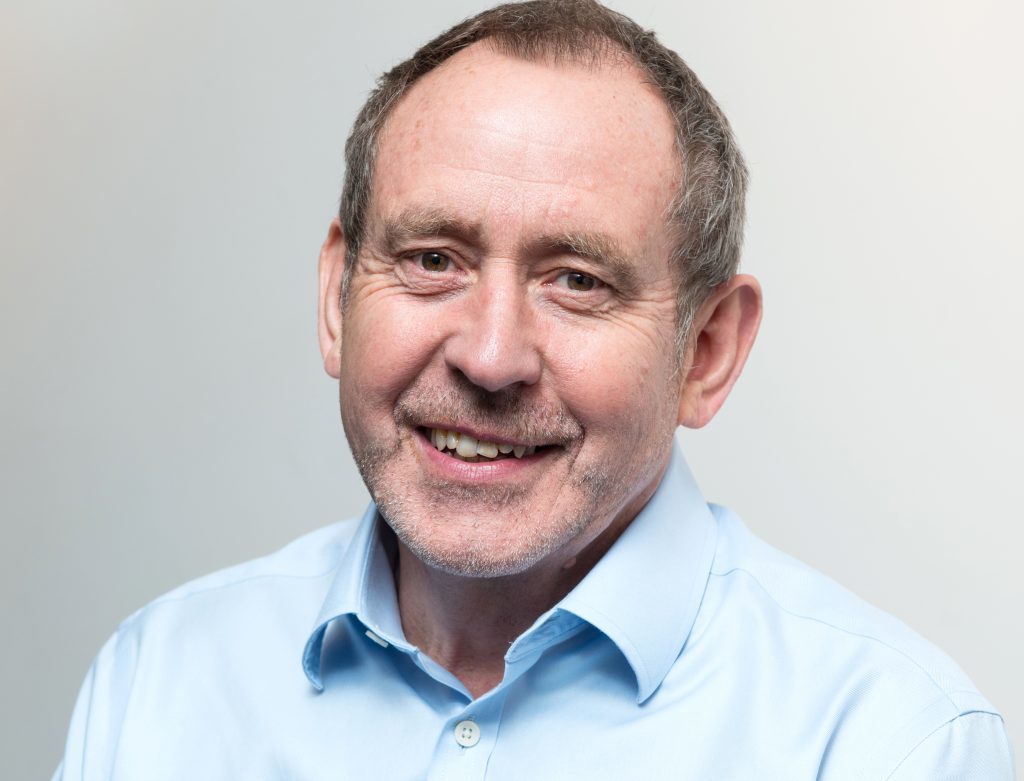
Today’s digital innovation is reshaping industries, disrupting business models and operating practices, and transforming business ecosystems.
Without a doubt, digitalisation is the engine fueling the growing adoption of Operational Excellence (OE) in the hazardous industries. Technology is at the heart of a rapidly accelerating effort to deliver unparalleled transparency, efficiency, and intelligence into operational decision-making.
Over 73% of industry leaders recognise the power of digitalisation to accelerate and deliver sustainable Operational Excellence. A reduction in operating costs, broader operational efficiencies, and fundamental transformation of the business are what’s expected. But while the benefits are clear and the tools available, the ability to realise real results is not.
Companies in hazardous industries have long struggled to deliver the desired levels of operational efficiency and effectiveness. Increasing levels of scrutiny on process safety and risk management have further exacerbated the challenge.
Over the past decade, industry’s answer has been the adoption of off-the-shelf software to streamline and automate processes. Point solutions succeeded in improving business functions, but they siloed organisations.
The industry then made significant investments in integrating systems, specifically maintenance management and planning solutions. Unfortunately, this approach failed to recognise two missing components, namely operational risk management and the reality of how work is executed and managed – which factor into wrench time and plan attainment.
There’s still time for hazardous industry operators to make a leapfrog – to get ahead of the digital transformation curve. Instead of digitising existing paper processes, there is an opportunity to deliver real, tangible business process improvements that drive towards operational excellence. But operators must first rethink the business process to get the digital transformation strategy right.
Think about the evolution of communications systems in Africa, which skipped an entire age of development and infrastructure to support landline communication, and moved straight into mobile communication.
Changing the way companies operate does not require years of investment to deliver safer, more efficient operational decisions. Rather, progress to operational excellence requires only an integrated approach to operations management.
A first step in delivering integrated operations management is to recognise the gaps between activity planning, maintenance management, operations, and the reality of how work is executed. The planning process can never be granular enough in terms of both detail and the time window to provide an executable schedule. All the ancillary tasks – usually safety-related – required to perform the planned activities are determined and managed by operational staff that is often divorced from the macro planning process.
The missing piece of the business process is engaging operations to make the schedule truly executable. By demonstrating how all ancillary tasks and the interactions between work activities come together, all levels of the organisation can manage the impact of operational activities in real-time. The quality and detail of the 90-day plan is also closer to reality, enabling much better resource utilisation and plan attainment.
Enterprise software platforms are fundamental to plugging the gaps between planning, maintenance, and operations processes – and help automate risk and activity management. New Integrated Operations Management platforms provide decision-support that significantly improves prioritisation, scheduling, and risk management. Now all levels of the organisation participate in fixing more of the right things – more closely integrating the plan to work execution goals.
Now everyone can have the context they need to support strategic operational efficiency and effectiveness goals. New platform technologies make it possible for operators to access a holistic view of their operational reality along with actionable insights that power excellent operations. Digitalisation can drive horizontal and vertical integration and successfully automate major processes. When applied correctly, digitalisation can make everyone’s job safer, better, and more efficient – a leapfrog from functional business improvements to excellent operations, enterprise-wide.
Recommended for you
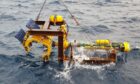