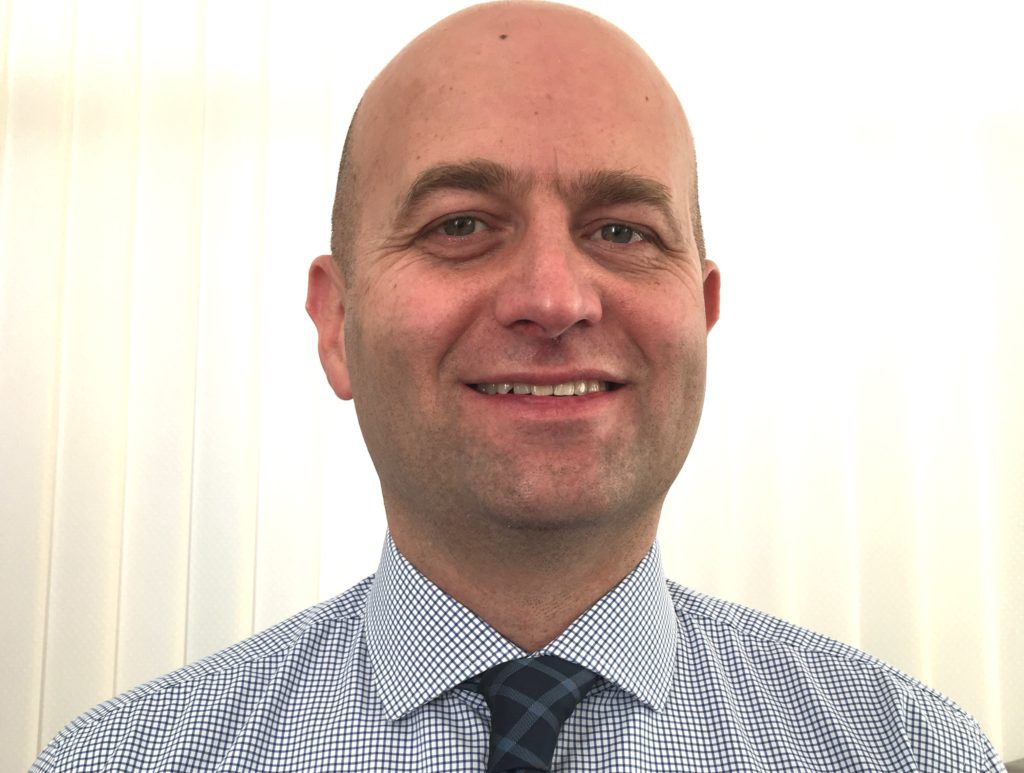
The UK’s offshore wind power capacity is set to nearly double over the next decade, as a result of a new government initiative, according to the industry.
It is said that by 2030, between a fifth and a third of the UK’s electricity could come from offshore wind power. Thanks to plummeting costs, offshore wind and floating turbines have become an increasingly affordable source of clean energy.
But in many ways, the technology experts are starting from scratch, even though it doesn’t have to be this way. Learnings from the oil and gas industry could speed up the development of floating wind turbines offshore, using existing technology that has already been tried and tested in a number of challenging environments.
Richard Pattison, technical manager at FES International, talks us through some of the learnings, the challenges and the potential expertise-sharing that could speed up the energy transition process.
There are a number of vital elements that are tried and tested in the oil and gas industry including the use of computer software for dynamic analysis. This crucial part of monitoring is well-established, has numerous highly skilled and ready-trained staff who could move across from the oil and gas industry immediately, and there are several suppliers already in existence who can provide the necessary accuracy explicit in this technology.
When offshore facilities are installed for oil and gas operators, there are also a number of codes and standards that have been developed over the years that can be easily transferred to floating wind turbine installations, speeding up the design process.
There are also numerous products, and manufacturers who have been working in challenging subsea environments for many years who produce items such as Diverless Bend Stiffener Connectors (DBSC). These products are field-proven to be structurally sound in various water depths and load scenarios. DBSCs offer the floating wind turbine operators a fully subsea autonomous connector system that is used to both connect and disconnect the electrical cable from the floating facility. This product saves both time and money as there is no need for a diver or a Remote Operating Vehicle to perform the operation.
FES is already working closely with some early adopters of floating wind turbines to ensure that products support the new technologies. For example the engineers at FES are adapting their DBSC to be more slimline, because the loads are lighter than in the oil and gas industry. This in turn reduces the manufacturing cost but without losing any of the technical specification, giving the burgeoning market a cost-effective, fully-designed solution to one of their engineering challenges.
Collaboration between the oil and gas, and floating wind turbine and renewables industries, is in its infancy although there are signs that the two are not mutually incompatible. In the North Sea, Norwegian Energy Company Equinor has revealed that it’s looking into the possibility of building a floating offshore wind farm to power two of its oilfields. With the two technologies now geographically closer than ever to each other, might we soon see engineers, products and skills being equally at home on both?
It’s likely that there are far more products that could easily support the floating wind turbine market that are in production but that the newly emerging operators might simply not know the language for and therefore engineers might be trying to reinvent the wheel! It’s up to those of us who work in the oil and gas industry, particularly subsea, to support with education, experience and signposting where we can.
Recommended for you
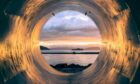