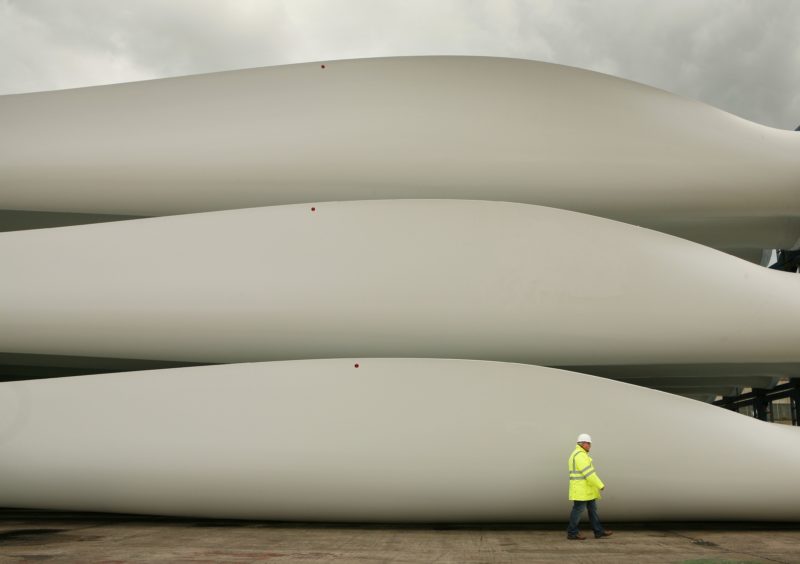
News of thousands of wind turbine blades in the US being cut up and sent to landfill as the only practical means of disposal was reported recently.
It is easy to imagine the reactions of many readers. It is potentially excellent ammunition for the pariah oil and gas industry that gets hammered by the greens at every opportunity.
Wind turns out to be not so clean, not so green. And Big Oil could capitalise on that by hitting back.
Here we have a situation where a major component of a huge number of wind turbines that are already life-expired or not far off cannot be properly recycled.
And with thousands more turbines being planted annually worldwide, the problem looks set to get worse. There are currently around 350,000 of these devices planted on- and offshore around the world.
The wind industry and NGOs like Greenpeace claim they are an excellent way of generating electricity cleanly.
To begin to understand the problem regarding the disposal of wind turbine blades it is important to get to grips with their engineering and manufacture.
To illustrate, wind turbine blades are built with epoxy resin composites while others use polyester and vinyl ester resins derived from petrochemicals such as ethylene.
The blades are fabricated in two halves and then bonded using large quantities of epoxy or modified acrylic adhesive.
The latest generation of very large blades that make heavy use of carbon fibre for main spar fabrication also incorporate large quantities of epoxy and other products developed by the petrochemicals industry.
The story by Bloomberg didn’t come as a shock to me. I’ve been aware of the recycling problem for a while and had started to do some research.
The journal WindPower Monthly raised the issue back in 2012, warning the industry that it already had a large-blades-disposal problem and that very little was being done.
It reported that the issue had been “quietly rising up the agenda” in Denmark, where a working group has been set up bringing together various key players including LM Wind Power, Siemens and Vestas, “to share knowledge about recycling options”.
Co-ordinator was to be the Danish Wind Energy Association. Well, I’ve just checked out the DWEA’s website for a clearly signposted reference to decommissioning. I failed to find anything.
I’ve also gone through the Global Wind Energy Council’s 2018 report published in April last year. Zero reference to decommissioning and only one mention of the word ‘blade’.
One of the very few companies specialising in systematic turbine disposal, Roth International of Germany is trying to find a better, more responsible destination than landfill for dead blades.
In collaboration with the Fraunhofer Research Institute and the Rohstoffwende Bayern research project, Roth says it is “further evolving” innovative techniques for rotor blade recycling.
It points out too that some composites can be reused directly after successful recycling and that the approach is sustainable. Roth also claims it will collect blades from anywhere around the world for recycling, which makes the very idea of chopping them up and dumping in landfills even more reprehensible.
Governments worldwide need to wake up and compel wind farm developers and operators to fully plan out lifecycles, which means taking responsibility for recycling.
That means the UK too. After all, the North Sea oil and gas industry is forced to do so.
The Danes, the Dutch, the Germans et al in European waters need to latch onto this and learn from Norwegian and Big Oil decom planning and implementation.
And if the Ospar Convention needs redefining to compel Big Wind to act responsibly on the decommissioning of North Sea mega-projects then that should be done too.
NGOs like Friends of the Earth and especially Greenpeace, which currently specialises in beating up the North Sea oil and gas industry, need to wake up to the already massive problem regarding the proper recycling of redundant wind turbines.
So that’s Big Wind; but what about Big Solar and Big Battery given their roles in the low carbon energy revolution?
It is important to note that Big Solar makes huge use of petrochemical-based products to manufacture solar panels too.
To make a solar panel, the silicon layers are sandwiched in between two panels, often made from the copolymer ethylene-vinyl acetate.Though there is established recycling and materials recovery for reuse, according to Green Match, there remains a need for a “proper solar panel recycling infrastructure” which can cope with the large volumes of PV modules that will be scrapped in near future.
The organisation claims that not only will PV recycling create more green job opportunities but also about £11 billion in recoverable value by 2050.
Moreover this will apparently make it possible to produce two billion new panels without the need to invest in raw materials. This means that there will be the capacity of producing around 630 GW of energy just from reusing previously used materials.
I’ll leave the looming problem of Big Battery for another day.
Recommended for you
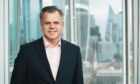