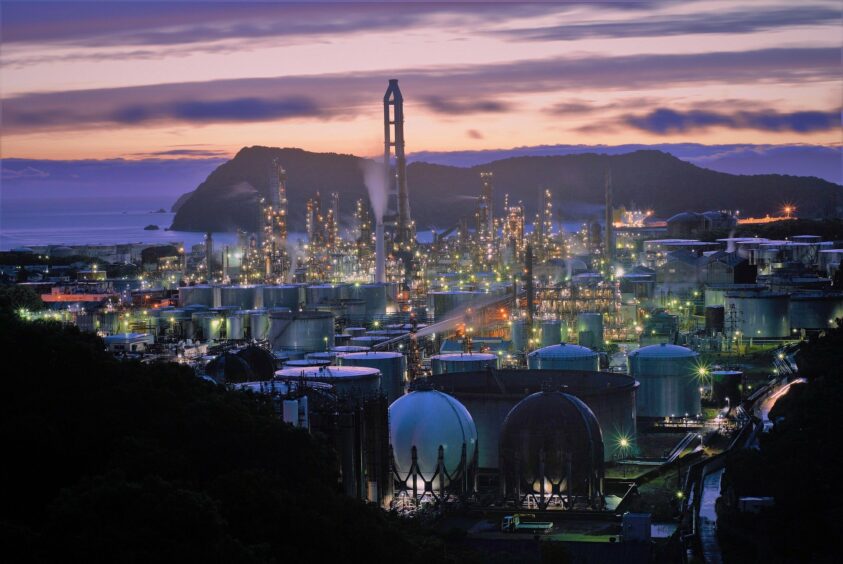
Across mature, capital-intensive industries such as oil and gas, operators typically want to sweat their assets. Asset performance and lifecycle costing are both critically important, as is minimising downtime and maximising the time that assets are fully operational.
Many of these assets are themselves mature and therefore more prone to breakages. This is exacerbated by the fact that they are often located in remote, hostile environments offshore.
The penalties for asset failure in the oil and gas industry are potentially extremely high, not just in terms of the financial cost of lost production, but also in environmental damage, personal injury and public safety. As a result, there are very few industries that are subject to the same intense levels of scrutiny from NGOs, regulators and governments. In the UK continental shelf area, for example, operators are effectively subject to strict liability for pollution damage and the cost of remedial measures up to US$250 million per incident.
An enterprise asset management (EAM) strategy has become essential if oil and gas operators are to extract maximum efficiency and value from their plant and achieve regulatory compliance. EAM is a holistic approach focused on managing all information, structured and unstructured, relating to physical assets and maintaining peak of performance throughout their lifecycle.
Adopting a successful EAM strategy requires clear scope-definition up-front. It is important that leaders and decision-makers across the wider business are actively engaged from the beginning of the process and made aware of the benefits of EAM through focused communication, workshops and other successful initiative delivery.
There also needs to be complete clarity about which business processes need to be prioritised and potentially transformed. Again, stakeholders across the wider business should be involved in this. Providers should encourage and develop this wider engagement and adoption as it will be critical to the ultimate success of any EAM project.
In essence, from a technology enablement point of view, EAM strategy can be enabled by bringing different, disparate and isolated back-office functions into one place, with a solid foundation digital core solution, covering processes such as supply chain, finance, maintenance and projects.
First and foremost, any organisation seeking to focus on EAM must address the question of data, bringing together data from assets into IT systems in a way that delivers tangible insight and business enablement.
Organisations need the right information from a broad range of sources to make good decisions. For example, they need visibility of the supply chain to prevent stock outs. If oil rig materials fail to arrive on time and equipment is not maintained, the impact on the bottom line is significant, not only increasing costs, but also in terms of the knock-on effect in lost production. A failing pump on a platform can take hours to get back up running and the revenue lost is not recoverable.
The core master data must be accurate and the data input must be timely and accurate, whether it relates to equipment or financial information, because poor data equals poor decisions or drives inefficiency in re-work. Data structures must match these requirements for timeliness and accuracy. If an inspection reveals defect or degradation in a key component, it must alert managers immediately.
Another prerequisite for EAM is process harmonisation. This is important because many organisations have gone through mergers and acquisitions resulting in them having different systems and ways of working across the asset base. A major consideration when addressing this challenge is to understand the impact of performing this process transformation by running an impact analysis to fully understand how to bring organisations to the same page and what activities must take place to facilitate this.
Implementing a core EAM solution may take no more than six to nine months, if its back-office solutions are already in place. A full enterprise solution might take longer. It depends on the scale of the company and its ambition. The determining factors are usually availability of resource, data migration, managing the operating structures and integration of “peripheral” applications key to the business.
EAM is already capable of delivering major efficiency and compliance gains for the oil and gas industry. Yet if we look ahead, we can see how technology will deliver more value beyond a core EAM solution. Automation, digital twin technologies and the growth of IoT application integration, as well as advanced predictive analytics, are some of the advanced technologies that can deliver additional value.
Within the IoT sphere, one marked trend is the standardising of data structures to harmonise data around operations. With sensor technology and automation, for example, this will enable engineers to see how the temperature in a bearing is trending in a particular way towards failure or reduction in performance, enabling them to resolve the problem during the next shutdown.
These are not new concepts, but the blending of information on which they depend is becoming more achievable, more consistent and cost effective. As solutions grow more robust and reliable and the advantages in reduced downtime and higher levels of performance become more obvious, forward-looking organisations will have a greater willingness to invest.
As we look a little further ahead, we can see that the growing sophistication of data analytics, allied to IoT technologies, make predictive maintenance a real-world solution, allowing managers to intervene just before components deteriorate and start to undermine performance.
In oil and gas, an industry of intense competition, significant gyrations in supply and demand and heavy regulation, EAM has a major role to play in increasing the efficiency of capital-intensive assets. It needs to become a core component of organisational strategy if businesses in the sector are to optimise their profitability and achieve compliance in tough conditions.
Recommended for you
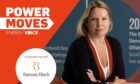