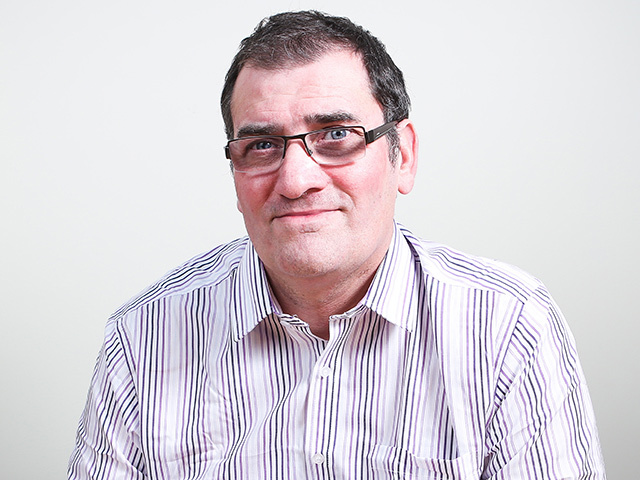
Having been involved for many years with the development of Control of Work systems, I’ve come to understand that implementing a control of work solution is always more than a “box ticking” exercise to satisfy the Health and Safety Executive.
There are multiple questions at the forefront of the customer’s thinking:
- Will this be the right system for my company?
- Will there be buy-in from staff?
- Can we afford to invest in a system like this?
One of the most common questions asked by customers is which type of Control of Work system will deliver the best results – paper-based or electronic? The answer is always the same: that there is no absolute answer. Each organisation will have individual requirements – they need to choose what’s best for them to meet their current needs while keeping one eye firmly fixed on their needs for the future.
That said, the trend in the UKCS in recent years is adoption of an electronic solution. The majority of North Sea operators – somewhere around 90% – currently use an electronic Control of Work system. However a number of support operations, such as vessels, commissioning and construction continue to use paper-based systems.
Operators recognise that electronic Control of Work systems provide a robust structure; the software simply does not allow users to take shortcuts which impact on the safety of the asset or fellow workers. Electronic systems provide and help generate a culture of consistency where everyone operates to the same, exacting standards to make work safe, and allow for information to be easily maintained and tracked. A further benefit is that the software can be linked to and interface with other corporate systems.
So, who are remaining percentage of operators still using paper-based Control of Work systems and what is stopping them from making the switch?
There is no hard and fast data on this but, anecdotally, the cost implications can be a significant barrier. It’s not as simple as buying a new system, as the cost of retraining the workforce, implementation and the potential hardware and infrastructure costs need to be factored in. The project will also invariably be competing with other budget priorities, and investment in a new system may not necessarily be a priority if the current operating system is deemed to be sufficient.
The financial argument is a relevant one, but those who use that as a reason not to give in to change should also take time to look at the bigger picture. The initial investment can be considerable, but what about the return on that investment? It’s known that those who use electronic Control of Work systems obtain cost efficiencies because they spend less time involved in ‘non-value add’ activities, for example copying a permit from a previous example by hand, and more time on ‘value add’ activities, such as reviewing a risk assessment.
There is also the natural human resistance to change. The current demographic of both front line workers and senior managers many of whom are making purchasing decisions are used to and are more comfortable with traditional paper systems and have a natural inclination to retain them. As the age demographic evolves over time, the majority of the workforce will be at ease with technology and electronic systems. For the senior managers, as well as the wider workforce, of the future, traditional paper systems will be an alien concept and take them out of their comfort zone.
There may also be other practical issues due to geography or location to consider and overcome. Where will the systems be hosted – locally or at a centralised data centre? Do we have multiple independent systems or is it centralised? Do we have the communication infrastructure with acceptable bandwidth and continuality?
And what about data back-ups – how do we cope with power outages?
Electronic systems may be more efficient, but technology does not replace the need for the correct behaviours, competence or safe thinking. An electronic system must be seen as a decision aiding tool not a decision making tool.
There is some evidence that an unintended consequence of an electronic system allows a reduction in the physical interaction and communication between workers leading to a potential increase in risk at the worksite. An electronic solution should never remove these best practise behaviours and processes, and should actually promote and provide more time to ensure that ‘eyeball to eyeball’ handovers and conversation still take place.
So what for the future of Control of Work systems? The answer may lie in hybrid systems – a mix of both paper and electronic. No system to date is 100% electronic; paper certificates are still printed and taken to the worksite. Will there ever be a fully electronic solution? This may come at some point but in the near future and although certain elements of the process will move towards a more inclusive electronic solution such as the use of mobile devices at the worksite to update work status, hazard identification exercises, etc. certain aspects of a Control Of Work solution will continue to retain a more manual or paper element and be seen as best practise moving forward.
Hybrid systems can provide the best of both worlds as they would allow for the increase in rigour and efficiency whilst retaining the practicality of non-electronic solutions to provide an increase in safety. Hybrid systems would also deliver enhanced visibility at a variable price point.
Operators should be prepared to take into account trends and prepare for any future changes that arise. Companies have to do what is right for their business both at the present time and in the future and, most importantly of all, implement change at the right pace for them.
The debate on electronic over paper will rage on, but we should never lose sight of the fact that it is all about managing the risk associated with Control Of Work, and not about the tools. Whether paper or electronic, the key focus must always be to keep work safe.
Greg Napier is product champion for international control of work specialists Cresent
Recommended for you
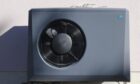