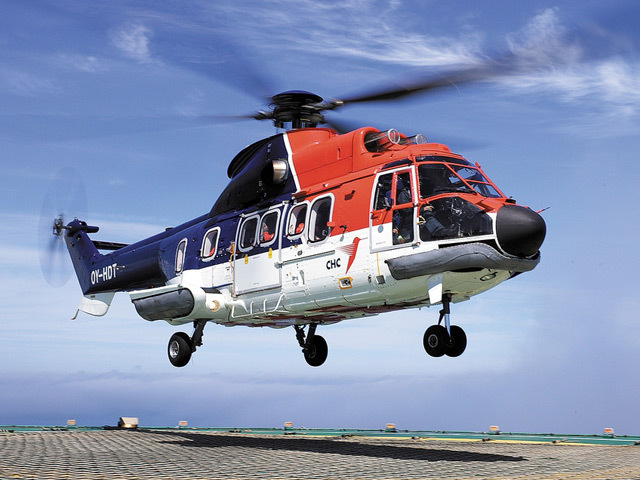
This week’s revelation that some among the UK North Sea’s leadership are to investigate whether the way “cramped” workers sit can be made safer worries me.
It is becoming clear to me here at Offshore Europe that at least some and possibly most of that leadership are unaware that most if not all of the legwork has been done.
I refer of course to the HeliSafe TA project launched in 2004 and which concluded in 2007. Its purpose was simple … to find ways of making helicopters safer for passengers to fly in.
And, as we reported in September’s Energy, Eurocopter was a participant.
EU-funded HeliSafe was based around the aeronautical industry in Europe. Its purpose was to research and develop systems capable of reducing risk of serious or fatal injuries to passengers and pilots in the event of a helicopter accident.
It investigated the application of devices used in cars, such as airbags, safety restraint harnesses, special seats and safety belt pre-tensioners, for example.
HeliSafe was led by Autoflug of Germany. The company specialises in the development and production of safety equipment, seats and electronic sensors for helicopters.
The initiative was a reaction to the US where competitors started some years earlier to intensify their research on pilot/passenger survivability, European helicopter manufacturers were forced into addressing this subject in order to maintain competitive.
The original HeliSafe consortium initially included eight partners from seven EU member countries, but as the project advanced, four further partners joined.
The first step was to gather all the available information throughout the world on helicopter accidents. Autoflug was then able to devise standard crash scenarios that were used to perform accident tests in “real-life conditions”.
Objectives of HeliSafe included:
- Development of appropriate prediction tools covering total airframe behaviour, the cabin and occupants in a crash.
- Develop supplemental realistic aviation-related occupant injury criteria
- Building on prior research to further improve survivability and mitigate severe injuries like offset, second and third impact and side impact effects.
- Improving knowledge of the detailed course of helicopter accidents via motion analysis of occupants and resulting contacts with the cabin structure during an impact
- Considering intelligent crash management concepts able to predict an accident; choose the
- necessary safety devices before and during a crash and identify post crash scenarios
- Transferring the high level of passive/active safety standard of automobiles into occupant safety in helicopters and tilt rotors and later into fixed wing aircraft
- Making airworthiness recommendations for certification requirements in the future
North Sea industry please note, particular attention was paid to then current crash statistics.
A full-scale baseline drop test was carried out in May 2005 with a full-scale helicopter fuselage supplied by Eurocoper. The impact scenario was calculated to cover the most typical helicopter accidents.
Two full-scale test rigs were designed and assembled representing the most common helicopter cockpit and cabin area geometries.
The geometry incorporates all injury related details of the interior to be as close as possible to the reality.
These mock-ups were used for the hardware sled tests where as basic condition current standard safety items were used to validate the HOSS (helicopter occupant simulation software) concept and to establish a starting point to compare later improvements.
Dummies were developed based on the injuries data harvester, including the so-called HeliSafe FAA Hybrid III dummy.
Eventually, this resulted in development of a digital simulator, which paved the way to designing a safety and protection concept that was then translated into mock-ups that were then tested.
The final safety concept was ultimately tested in a second full-scale test at the end of the project to confirm the improvement under real crash loads.
The shocking bit of this work is that, by 2007, HeliSafe had come up with a safety concept which was years ahead of anything available in Europe.
It also generated a validated numerical simulation tool to predict typical crash scenarios and to simulate the response load on the human body with respect to the interaction of safety equipment.
Apparently, this simulation tool is able to analyse and optimise any cockpit and cabin with respect to response loads to human bodies.
Says HeliSafe in a summary of its final report: “Helicopter manufactures can now design safe cabin systems as well as getting recommendations for retro-fitting to existing helicopter for improving survivability of occupants in typical crash scenarios.”
In short, a safe cabin concept has been developed and which includes special safety seats, airbags, optimized safety restraint harnesses with automatic inertia reels, safety belts with pre-tensioners and load limiters.
So what’s my point?
Quite simple really; there is a body of work out there that the UK offshore industry’s HSSG (Helicopter Safety Steering Group) needs to become a lot more au fait with than currently seems to be the case, before it does anything else. Otherwise there is a risk of reinventing the wheel.
I’ve flown in Super Pumas from time to time and appreciate how cramped they are. Instinctively I’ve always avoided the seat in the middle at the back. I’m not surprised that it is hated by many offshore workers.
Recommended for you
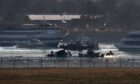