
As advances in exploration and subsea technology make existing reservoirs and marginal fields more viable, it is not only the age of your platform that counts – what you know about its condition is vital too.
After nearly 40 years of production in the North Sea, many of the offshore platforms in the UK Sector are moving towards, or indeed have already exceeded, their original design lives.
But what may seem a difficult issue, is not a fundamental problem in itself, if the operator is fully in control of the ageing process of an asset and responsive to how their installation and subsea infrastructure is ageing over time.
Nowhere is this more apposite than for second tier operators, who may have a limited window to get the right degradation management system in place.
Many of these new operators will have inherited legacy issues such as missing or incomplete design and “as-built” data, which needs to managed.
Perhaps the gaps are not readily transparent yet as experienced platform staff, Tupe’d across as part of the acquisition agreement, keep the systems operating.
However, operators must bear in mind that many of these linchpins are rapidly approaching retirement and along with that milestone, much of the knowledge and capability may disappear.
As innovative, new subsea systems are tied back and hook up to existing platforms with older topside and subsea infrastructures, dealing with the issues of asset integrity and age degradation becomes crucial.
In order to show its continued operation is fit for purpose, such infrastructure requires robust and effective management processes and controls. This is also important in areas such as personnel succession planning, training and competency processes.
Not only does this display competency and confidence, it also demonstrates to the regulator an assured commitment to managing life extension, while showing a sound understanding of the implications of health, safety and environment risks and the mitigation measures which are aimed at preventing major accident hazards.
Degradation management has been a major item on the Health and Safety Executive’s agenda for over a decade now.
Between 2000 and 2004, its Offshore Safety Division (OSD) ran an initiative, known as Key Programme 1 or KP1, aimed at reducing hydrocarbon releases and focusing on the integrity of process plants.
The results were revealing. Although they saw a considerable reduction in the number of major and significant hydrocarbon releases, the OSD had become concerned about an apparent general decline in the condition of fabric and plant on installations as a whole.
And what was its response? KP3, a project directed more widely at asset integrity, which ran for the next three years.
The key messages from this programme have informed further strategy and HSEQ policy, most notably The Ageing and Life Extension Inspection Programme (July 2010 which concluded in December 2013), as well as the associated Offshore External Corrosion Project (2010).
Throughout their development, the key objectives of these programmes were “to promote awareness and management of the risks associated with ageing plants in the offshore oil and gas industry” in support of four identified priority areas: asset integrity, competence, safety culture and leadership.
An interim report issued 14 months ago identified that duty holders had asset integrity management (AIM) systems in place and were beginning to integrate asset life extension (ALE) into that process.
Acronyms aside, operators are spending considerable sums on inspection, repair and maintenance possibly as a direct consequence of the KP3 programme.
But is this enough? The answer presents slightly differently topside to subsea.
The majority of topside structures and equipment is visible, allowing easier access for inspection and the collection of data, facilitating repair or replacement of deteriorating parts. Subsea on the other hand is more of a challenge and ultimately more expensive.
Hence it is important that senior management ensure that their AIM and ALE processes are robust, that intelligent pigging frequencies and temporary repair registers are maintained.
Data from their risk-based inspection and corrosion threat assessments should also be acted on in a timely manner.
A further demand for senior leaders is that information derived from this analysis is only useful if experienced inspectors and engineers of the correct discipline are involved in its interpretation.
Good practice is to have an independent resource present to act as the team’s conscience at the assessment workshop sessions. So, it is a question of reliable data, appropriate assessment and dissemination by an impartial team and most importantly effective decision making.
George Melvin is associate director of HSEQ at FQM Ltd. See you all at Subsea Expo 2014, February 5-7.
Recommended for you
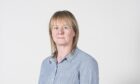